Welcome to the Onshape forum! Ask questions and join in the discussions about everything Onshape.
First time visiting? Here are some places to start:- Looking for a certain topic? Check out the categories filter or use Search (upper right).
- Need support? Ask a question to our Community Support category.
- Please submit support tickets for bugs but you can request improvements in the Product Feedback category.
- Be respectful, on topic and if you see a problem, Flag it.
If you would like to contact our Community Manager personally, feel free to send a private message or an email.
Making Stringer Notches

I'm making a model RC plane and need help with making the fuselage. I want to make a structure similar to this with stringers notched into the formers/bulkheads: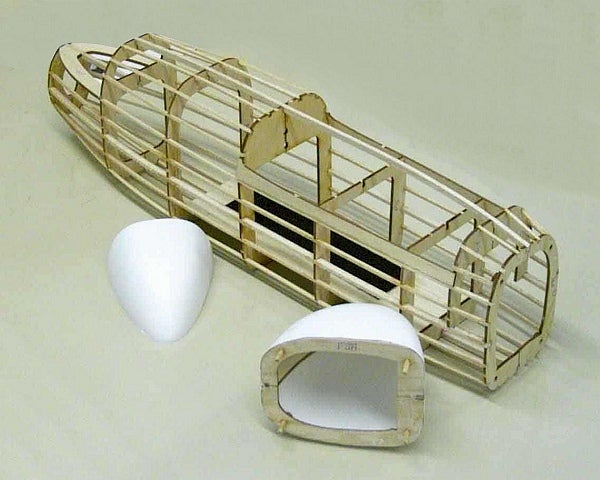
This is how my structure currently looks like:

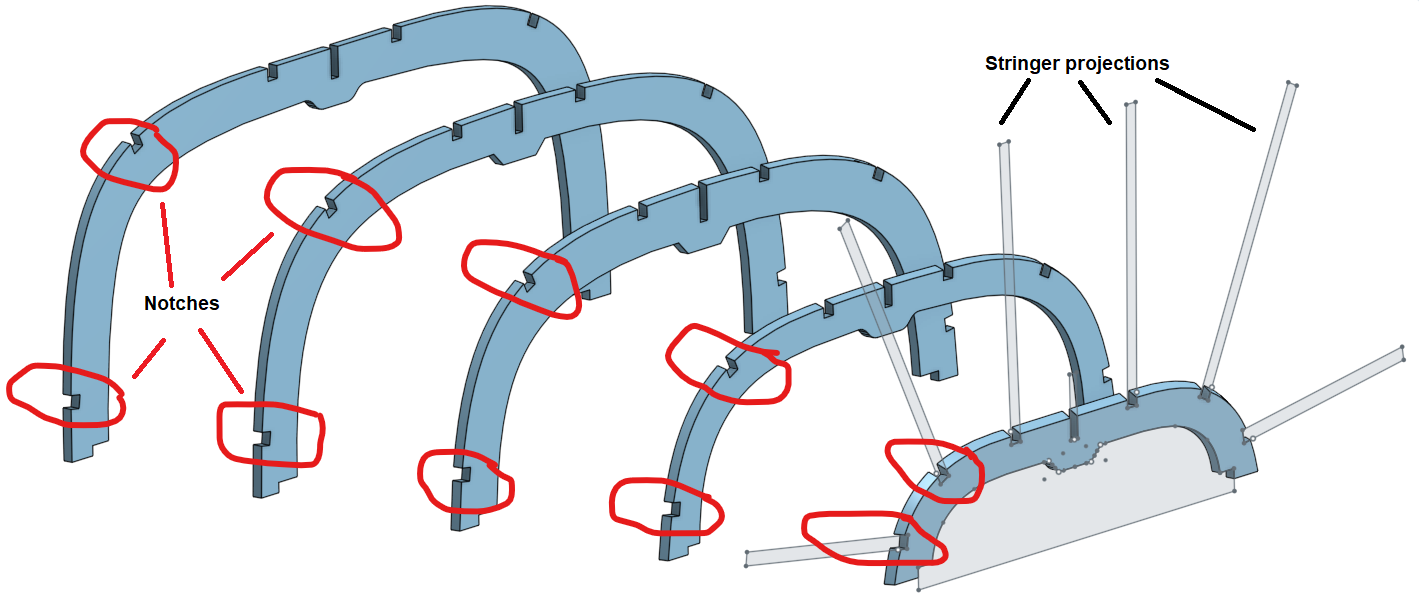
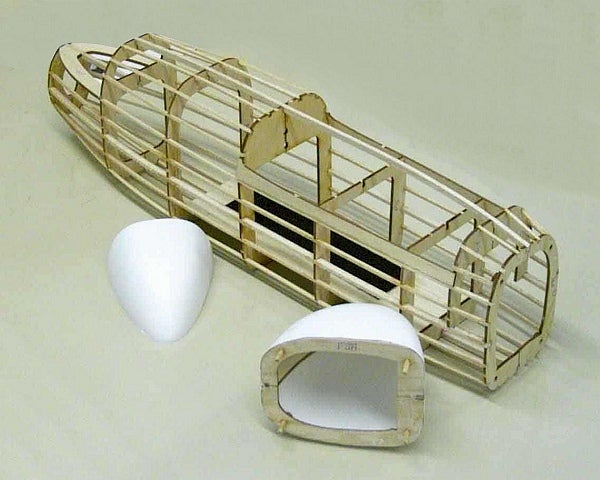
This is how my structure currently looks like:

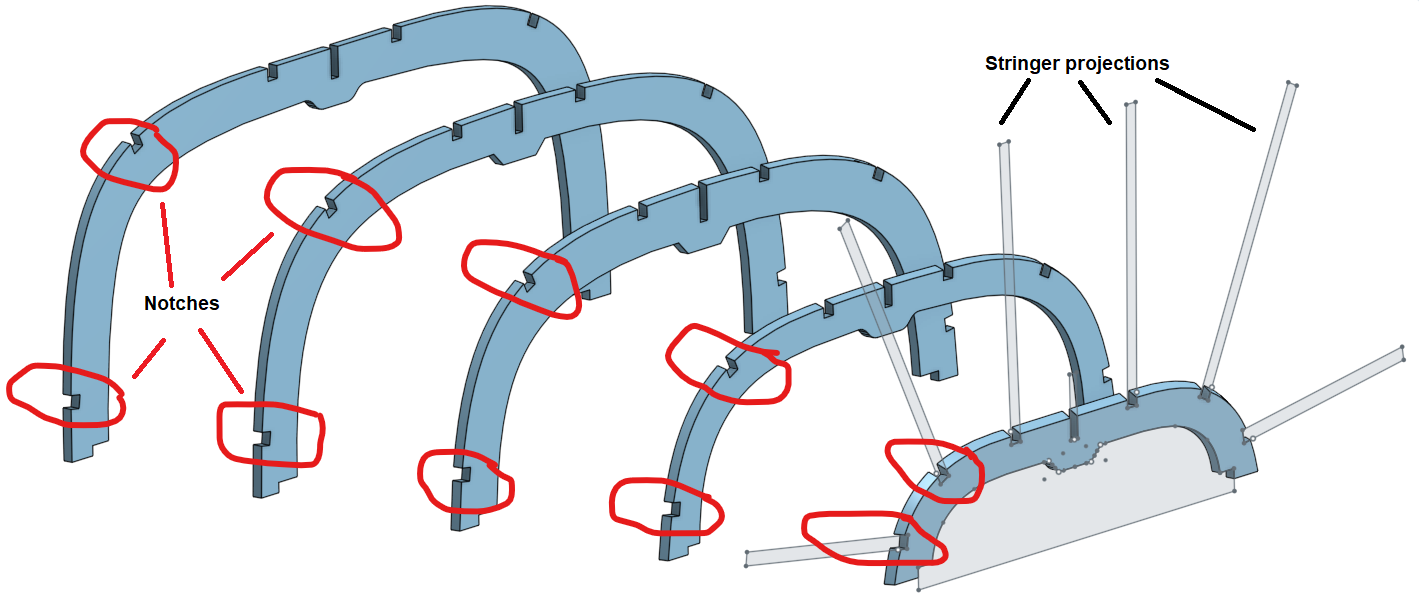
I'm using the following steps currently:
1. Start a sketch on the first former and sketch the projection of the stringers in the desired locations along the perimeter.
2. Define dimensions of the width and depth of cut for each stringer notch in the former.
3. Extrude this sketch to cut out notches in the first former.
4. Sketch on the next former using the first sketch as a reference then extrude and cut out the notches in the second former.
5. Repeat steps 1-3 for each former
Constraints for making the notches are:
1. A straight stick of wood is used for each stringer so notches must accommodate that.
2. Notch depth on each former must be constant.
This method seems to be repetitive and time-consuming. Can someone suggest a better method to go about it?
1
Comments
Create your stringers, then subtract the stringers from the other parts.
Learn more about the Gospel of Christ ( Here )
CADSharp - We make custom features and integrated Onshape apps! Learn How to FeatureScript Here 🔴
If you can provide a public link to your document (so that other folks can review / copy / make suggestions) it will be easier to show you what I mean.
Here's an example I put together that shows the process I describe above.
https://cad.onshape.com/documents/a9c6ff3adb3b697195131225/w/49ed434d89237c141a748621/e/edacc31bfae6411886307008
- make the entire fuselage as a singe solid loft
- split the notches into the face and use move face to get a single notch depth
- split the loft into separate parts
- extrude the faces of the new split parts (i assume you'll laser cut these or something, so you want them straight)
- delete the extra stuff.
p.s. some of my practices are "bad" here for speed, so just reference it and do your own thing.The Onsherpa | Reach peak Onshape productivity
www.theonsherpa.com
The Onsherpa | Reach peak Onshape productivity
www.theonsherpa.com
I like your approach of lofting the hull as one part (my approach had no way to create the actual correct hull shape), the serpentine split surface, and the "extrude multiple faces in one extrude feature".
However, I think the split face + move strategy for creating the notches produces some unwanted twisting in the notch faces:
(If the stringers don't need to be planar, this is no problem, of course).
I wonder if some extra steps to replace your step 2 might help:
...then move on to: split the body, extrude each rib etc etc
[edit to add this]
Here's my cleaned-up version using your approach, with planar stringers. Much cleaner than my first go.
Improvements for sure. I like that you get the stringers with this one too. I can't help but think of some Featurescripts I'd want to write if I had to do this often.
The Onsherpa | Reach peak Onshape productivity
www.theonsherpa.com
What?! Multi-Mirror? How did I miss this??
We need a better way to keep up with people and features. Is there a subscribe button I'm missing?
Learn more about the Gospel of Christ ( Here )
CADSharp - We make custom features and integrated Onshape apps! Learn How to FeatureScript Here 🔴
Hi,
I know this is an old post but are there any sample documents still around?
Thank you.
at it turns out, I don't have access to my example anymore since exiting my agency.
The Onsherpa | Reach peak Onshape productivity
www.theonsherpa.com
Ok thanks @EvanReese - worth asking!