Welcome to the Onshape forum! Ask questions and join in the discussions about everything Onshape.
First time visiting? Here are some places to start:- Looking for a certain topic? Check out the categories filter or use Search (upper right).
- Need support? Ask a question to our Community Support category.
- Please submit support tickets for bugs but you can request improvements in the Product Feedback category.
- Be respectful, on topic and if you see a problem, Flag it.
If you would like to contact our Community Manager personally, feel free to send a private message or an email.
Mold Split

I am trying to make a mold split to a mold, that has already been splited. But it's not really working.
Is it not possible or am I making a mistake here?
It's the middle part, which I would like to split in half using Surface 1 as a split line.
I have also tried the normal split function without result.
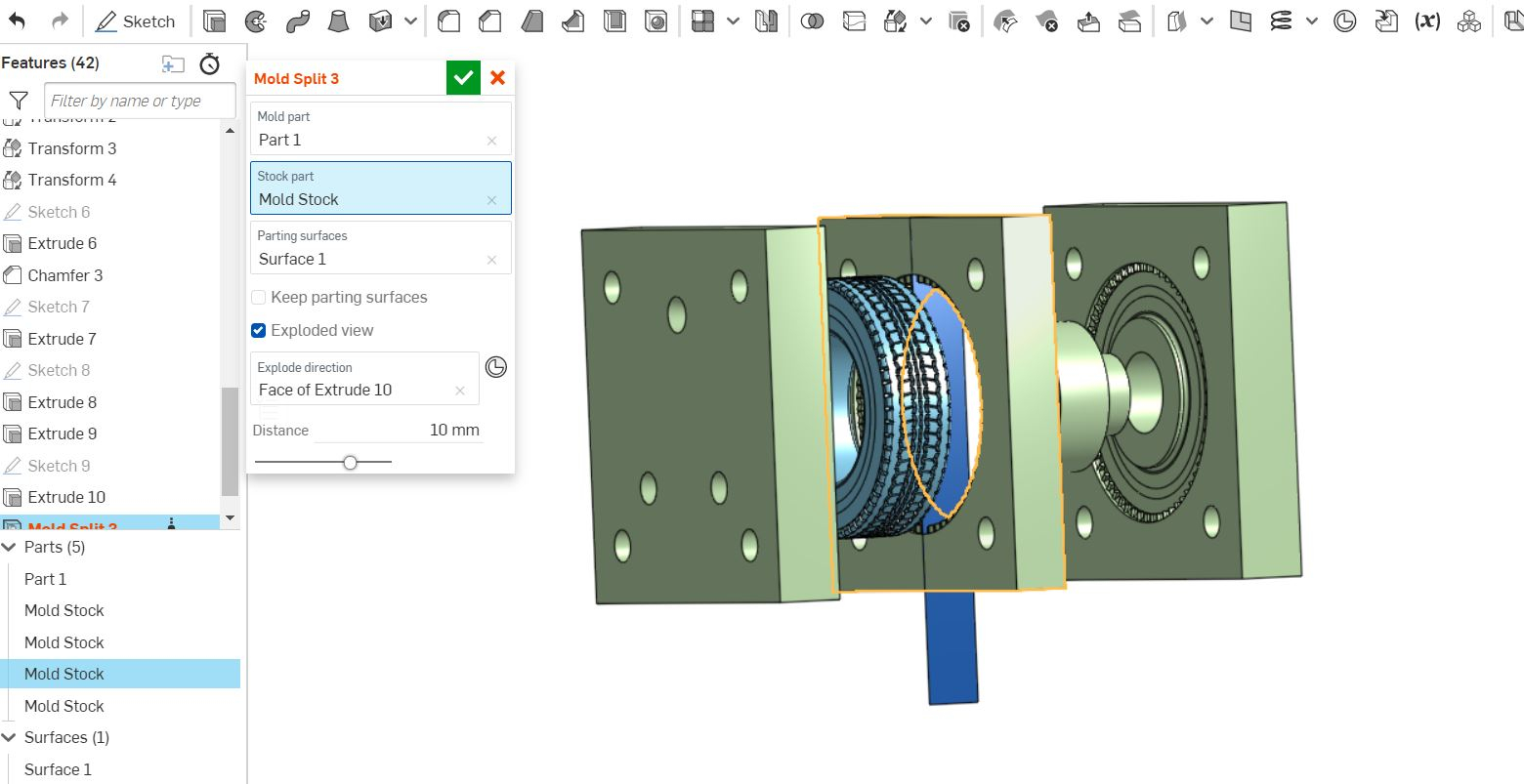
Is it not possible or am I making a mistake here?
It's the middle part, which I would like to split in half using Surface 1 as a split line.
I have also tried the normal split function without result.
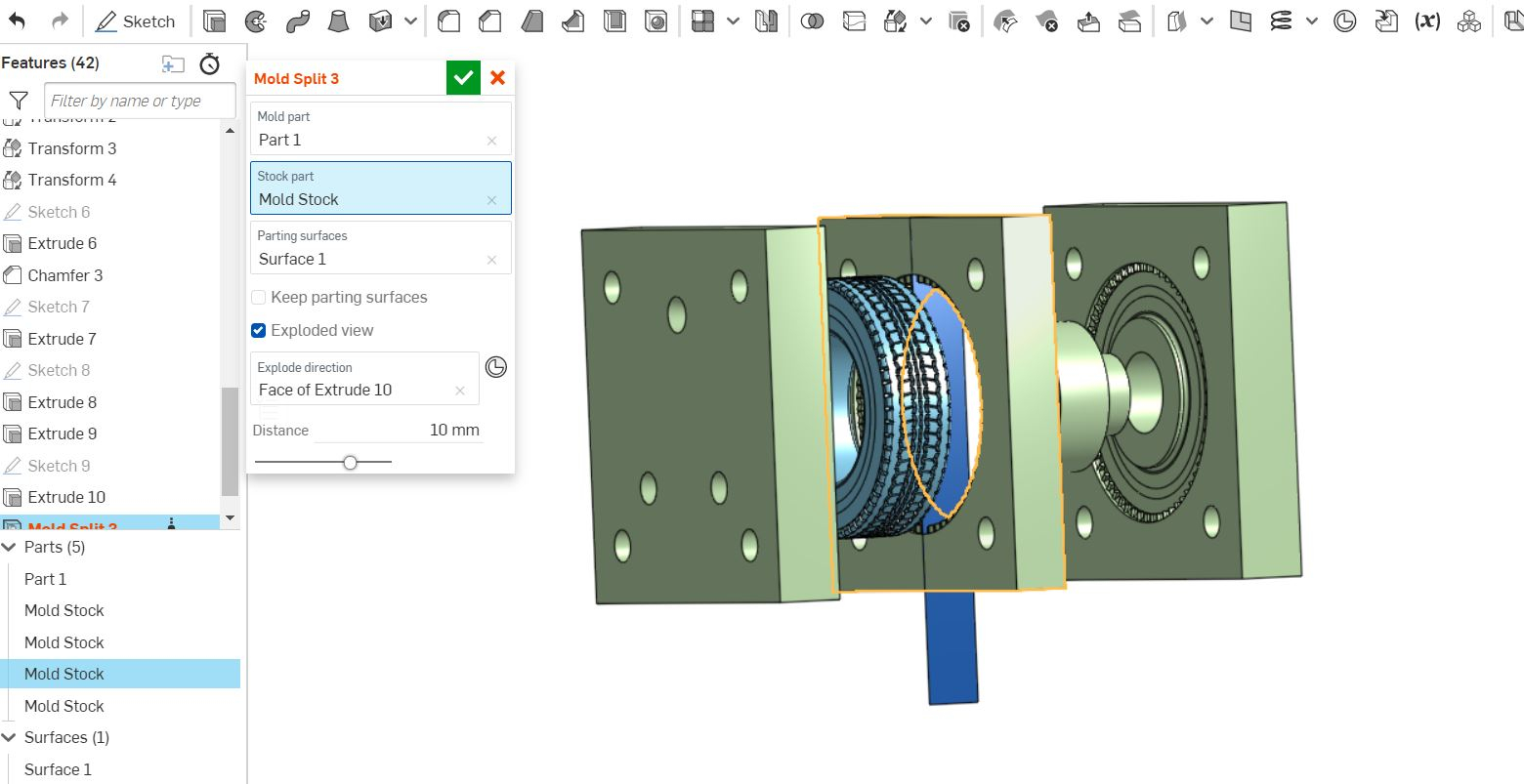
0
Best Answer
-
romeograham Member, csevp Posts: 715 PRO
The problem is that the tire tread creates "non-manifold geometry" when you split with the Front and Top planes:
You can see that the corners of the treads are coincident with the split plane. Once you make the cavity tooling, those areas can't be split.
A simple solution could be to add fillets to your existing treads, so the corners are no longer coincident with the split plane:
Here's a document showing this in action: https://cad.onshape.com/documents/c86cb25c34b7a77dcd7dccfe/w/1d6dc4efcb1cae5df0a9ebda/e/d706e67e264f0ba172c1a0b3
There's also a slightly different approach to part studios: you may find value in separating the Part modelling from the Mold modelling.
Hope this helps!0
Answers
The Onsherpa | Reach peak Onshape productivity
www.theonsherpa.com
It would probably be best to use the regular Split feature from the toolbar for this feature and use the Right Plane as @Evan_Reese suggested above.
Use the Mold tools at the beginning of your feature list (and probably only once per Part Studio), and use regular features after that. There is good documentation for the Mold tools, but they are a tough to get working in some difficult situations.
I got to know about the Mold Stock and Mold Split in a webinar featuring Neil Cooke, and he used a surface to split the mold, and I also split the mold twice using a surface.
I have also used the regular Split feature with a plane as parting surface. Also no luck.
I have split the part using 3d part studio in Windows - that us usable, but I would like to work more on the parted parts in Onshape. It's still a work in progress....
If you can share a public link to your model, we can have a look and see if we can help.
The Onsherpa | Reach peak Onshape productivity
www.theonsherpa.com
Here is a link to my model. It is the part B which I would like to split. And ideally in 4 parts using the Front and Top plane as split lines.
https://cad.onshape.com/documents/a1ec71c942c235a8a585444f/w/d09780828fd5d7e4f9b9f4cd/e/b0e40daad5f47a96b1cd0c4c
You can see that the corners of the treads are coincident with the split plane. Once you make the cavity tooling, those areas can't be split.
A simple solution could be to add fillets to your existing treads, so the corners are no longer coincident with the split plane:
Here's a document showing this in action: https://cad.onshape.com/documents/c86cb25c34b7a77dcd7dccfe/w/1d6dc4efcb1cae5df0a9ebda/e/d706e67e264f0ba172c1a0b3
There's also a slightly different approach to part studios: you may find value in separating the Part modelling from the Mold modelling.
Hope this helps!
A simple solution to a complicated (for me) problem.
I have replicated your design changes in my model without problems.
I plan to try and print the mold and use it to cast the tires.
Your point about rotating the tire makes good sense. This is the result after a 3 degree rotation.
Now the split line is free of the thread pattern. If it makes any problems in the casting, then I can adjust the number of thread patterns to increase the distance between them.
Thanks for the input.