Welcome to the Onshape forum! Ask questions and join in the discussions about everything Onshape.
First time visiting? Here are some places to start:- Looking for a certain topic? Check out the categories filter or use Search (upper right).
- Need support? Ask a question to our Community Support category.
- Please submit support tickets for bugs but you can request improvements in the Product Feedback category.
- Be respectful, on topic and if you see a problem, Flag it.
If you would like to contact our Community Manager personally, feel free to send a private message or an email.
Configurations vs Configurable
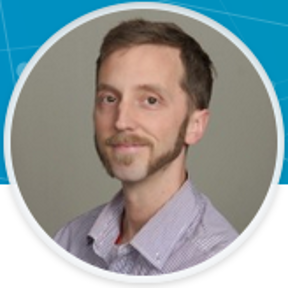
In production having configurations for various Hardware is
awesome. Washers/spacers/pins/shoulder screws/orings/bumpers/cable
management/ ... name it. I can assign PNs and Descriptions for discrete
items.
However, in R&D I often just
want to try various sizes of washers/pins/screws/... without having to
go in and make a new discrete configuration with PNs/Descriptions/...
and then version the part. So for this, the Configurable Variables are
great. I just look on mcmastercarr (or wherever) for a size that fits my
need, then I go in and type the necessarily values into the
configuration, generate, and it populates. No need for versioning or PNs
and descriptions or whatever.
However, I
can't see how to have both in the same part studio. My workaround is
that I duplicated my Part Studio and named one "Configured" where HW
with Part numbers, descriptions, ... exist with parametric variables.
And a 2nd part studio called "Configurable" where I can easily pull an
infinite variety of parts in for playing with in my WIP assemblies
without having to make configurations.
Another
work around I've used is just importing the STEP file from places like
mcmastercarr and then if I keep it I go and add the configuration and
give it a PN/Desc/.... then replace it in my assembly.
Anyone else solve this in a better fashion?
0
Best Answer
-
tim_hess427 Member Posts: 648 ✭✭✭✭
@Jolls - after reading your comments above again, I think I did misunderstand what you're looking for.
To phrase your request a different way, it sounds like this: When inserting a part into an assembly, you want the option to select a pre-configured part or define a new configuration?
I just did a quick test and think you might be able to use branches for this. In one branch, you can set up your models with configuration variables. Then, create a new branch of the same workspace and replace the configuration variables with parametric variables controlled by a configuration list with your detailed items.
Then, if you ever have to add features to your model, you can model them in one branch, and merge the changes from the first workspace into the other - the configuration differences should remain. NOTE: This only works if you only merge in one direction. If you ever try to merge back the other direction, you'll end up with both branches configured the same.
Now, when importing into an assembly, you just select the correct branch and you can either select a part from a list or define the variables directly.
EDIT: I was working on this while you were working on your post. I think this will work for you if the extra step of pulling up the version graph and selecting the right version of the part studio is OK.1
Answers
This may not allow for only one part studio, but it may make things more automated and less configured.
Here is a method that I like to use:
- Derive all of the "Bolts" to one studio.
- Configure the derives
- Composite all parts with Composite Selected by @monroe_weber_shirk
- Configure the names with Set Name by Randy Ngo
No matter what configuration it is in, it will always have the same composite part, and same mate connector.Learn more about the Gospel of Christ ( Here )
CADSharp - We make custom features and integrated Onshape apps! Learn How to FeatureScript Here 🔴
I set up a part studio with configuration variables for diameter and thickness for a simple disk. I gave properties to three different specific configurations (first image). I am also still able to pull the disc into an assembly and give it a configuration that isn't listed with specific properties (second image).
That is an interesting method for combining imported parts. I may use that for some things. It doesn't quite solve the problem I'm attempting to solve but the solution you proposed can make some other things I do more efficient. Thanks!
Another Option is to use a Configuration Variable which allows you to create a custom configuration when inserting into an assembly. This allows you to make a spacer of any length, OD, ID. However once you settle on a size you like for your design, this part is NOT re-usable anywhere else.
So those are the two methods. What I basically want is the feature from BOTH of the above methods. I want to be able to generate any Spacer I want in an assembly until I finalize the design; and then to make that part into an actual configuration that is re-usable anywhere else with it's complete information (PN, Desc, Vendor PN, Vendor, ...)
To phrase your request a different way, it sounds like this: When inserting a part into an assembly, you want the option to select a pre-configured part or define a new configuration?
I just did a quick test and think you might be able to use branches for this. In one branch, you can set up your models with configuration variables. Then, create a new branch of the same workspace and replace the configuration variables with parametric variables controlled by a configuration list with your detailed items.
Then, if you ever have to add features to your model, you can model them in one branch, and merge the changes from the first workspace into the other - the configuration differences should remain. NOTE: This only works if you only merge in one direction. If you ever try to merge back the other direction, you'll end up with both branches configured the same.
Now, when importing into an assembly, you just select the correct branch and you can either select a part from a list or define the variables directly.
EDIT: I was working on this while you were working on your post. I think this will work for you if the extra step of pulling up the version graph and selecting the right version of the part studio is OK.