Welcome to the Onshape forum! Ask questions and join in the discussions about everything Onshape.
First time visiting? Here are some places to start:- Looking for a certain topic? Check out the categories filter or use Search (upper right).
- Need support? Ask a question to our Community Support category.
- Please submit support tickets for bugs but you can request improvements in the Product Feedback category.
- Be respectful, on topic and if you see a problem, Flag it.
If you would like to contact our Community Manager personally, feel free to send a private message or an email.
Strategies for modelling injection molded parts

in General
Hi all I'm having a hard time figuring out a workflow for adding features to constant wall injection molded parts. I will share a very simple example for discussion of strategy. Of course a real part the geometry would be much more complex. The example is a straight wall of an injection molded part that has a square area sticking out. Outer side of the wall is shown in the first picture. Section of wall is shown in the second picture. This is the desired shape.
I made this by drawing the wall, then drawing the box, then trimming each to each other, then boolean union the two surfaces together. Then thickening the resultant surface to the nominal wall of the part.
This works great. What I'm having trouble figuring out is how to make the same shape if the straight wall has already been thickened earlier in the tree. For example a part is far along in modelling and development, and then a feature like this square is decided to be added on. It often doesn't make sense to roll back before the main wall is thickened to add a new small feature.
Here is the public document. One workspace shows the strategy shown here called "thicken after merging" The second workspace, "thicken before square" is my attempt to make the same shape after the main wall has been thickened. I did not get all the way to the end, and it seems I have a lot of steps.
Public document:
I'd appreciate any strategies to deal with this concept! Thanks all!
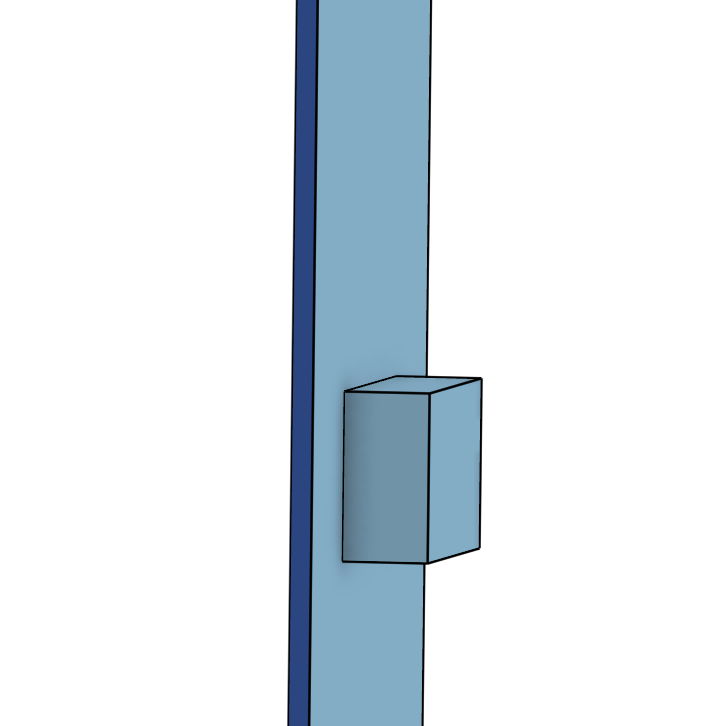
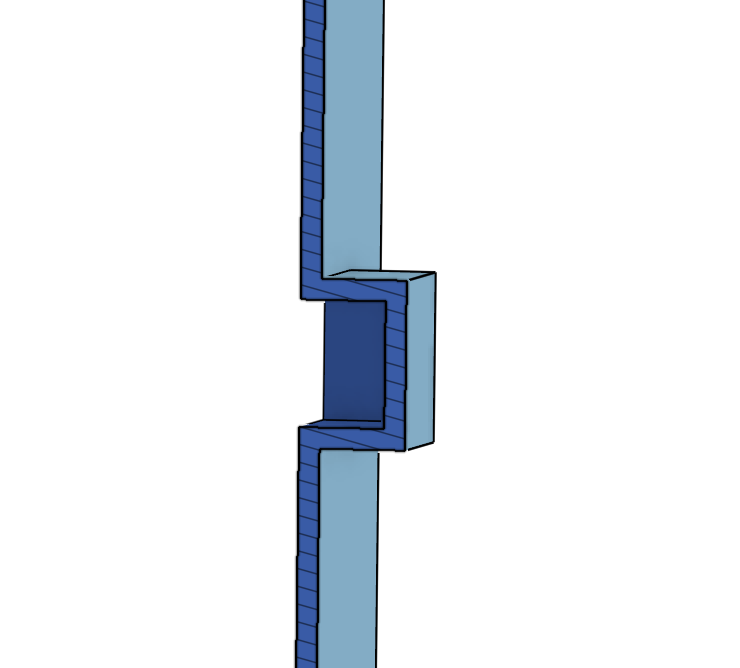
0
Comments
Looks like a lot of work to use surfaces and thicken for the sample given.
Some draft is already included in this sample.
Try adjusting #wall and every thing will update.
https://cad.onshape.com/documents/44300b8443e31a8a7552cb4e/w/9ece92663a727e60560de254/e/bd0929f55e8be2408b615bb8
Nice use of shell. I like that better than my multi extrudes.
The point is to use the simplest technique for what your working on. In the sample given solids would do the job nicely with out as much complexity.
Use both surfaces and solids to as needed to accomplish your task.
I personally like a shorter feature list. Parts can become quite complex and convoluted on their own with out my technique adding to that.
https://cad.onshape.com/documents/44300b8443e31a8a7552cb4e/w/9ece92663a727e60560de254/e/bd0929f55e8be2408b615bb8
The Onsherpa | Reach peak Onshape productivity
www.theonsherpa.com
PS, is your recording something built into onshape? Or is it a regular screen capture tool? I see a few people have similar in their posts. I'm not sure how its done.
https://www.cockos.com/licecap/
The Onsherpa | Reach peak Onshape productivity
www.theonsherpa.com