Welcome to the Onshape forum! Ask questions and join in the discussions about everything Onshape.
First time visiting? Here are some places to start:- Looking for a certain topic? Check out the categories filter or use Search (upper right).
- Need support? Ask a question to our Community Support category.
- Please submit support tickets for bugs but you can request improvements in the Product Feedback category.
- Be respectful, on topic and if you see a problem, Flag it.
If you would like to contact our Community Manager personally, feel free to send a private message or an email.
Best way to add a hole pattern to a round sheet metal part?
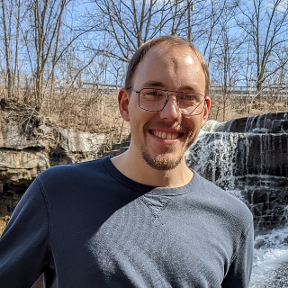
I am trying to create a sheet metal cylinder with drainage holes in the sides as shown in the attached screenshot. I created the cylinder as an extrusion of an arc that almost creates a complete circle. Then, in the flat pattern made a sketch with 2 circles and patterned it to fill the flat. Then I extruded that sketch. As you can see in the screenshot, this took over 37 seconds to compute. I'm sure there is a more efficient way to create this feature, I'd be grateful for some suggestions.
0
Answers
I don't see any screenshots or a link to your project. Either would better show us what you are trying to accomplish.
Creating a vertical "slice" of your part with just one row of holes (pattern in one direction only in the sketch) and patterning the part should be significantly faster but will require more features...
Simon Gatrall | Staff Mechanical Engineer | Carbon, Inc.
The holes are all perfectly round in the flat so can be dimensioned on a drawing (which could be annoying if they are slightly out of round).
I'm not sure why face patterns aren't allowed in sheet metal though, maybe it's a Parasolid limitation?
So i do a line to point dimension and it comes out good for the drawing, so i don't care.
The fact it isn't absolutely perfect does bother me, but that is so mild i doubt you could manufacture it closer with our laser table...