Welcome to the Onshape forum! Ask questions and join in the discussions about everything Onshape.
First time visiting? Here are some places to start:- Looking for a certain topic? Check out the categories filter or use Search (upper right).
- Need support? Ask a question to our Community Support category.
- Please submit support tickets for bugs but you can request improvements in the Product Feedback category.
- Be respectful, on topic and if you see a problem, Flag it.
If you would like to contact our Community Manager personally, feel free to send a private message or an email.
Options
Flexure that allows for Configurable Positions
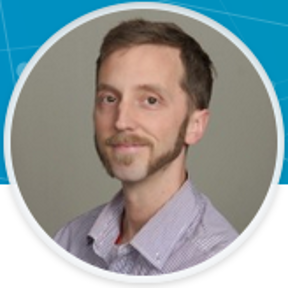
I have a parallelogram flexure and for visualization purposes I'd like to have the assembly with a couple different configurations showing the flexure with different bends. How have you guys done this in the past? The only "bend" I really know of is sheet metal and while that might work I thought I'd ask here before I put in the work to make a flexure into "sheet metal" (even though it's not sheet metal) just for visualization purposes.
A simple example would be a cantilever with fixed position on one side and a variable force on the other side. It'd be nice to bend the cantilever showcasing various bent positions.
Tagged:
0
Comments
I would model the legs of the parallelogram in a way that you can easily vary a dimension to drive the different positions, and I would loft the flexure portions between the legs. You'll have to be somewhat clever about controlling the length of the neutral axis in your layout sketch (if you're going for accuracy).
Thanks. I was considering doing something like that too. It's just drastically more complicated than a simple single sketch extrude which is how this flexure is designed now. But I may just have to do it. I also just considered making an assembly and effectively cut it into 3 parts (fixed, flexure, moving part) so I could at least better illustrate how the device works. Clunky but easy. And not as clunky as just having a static flexure.
You could also create separate bodies for the straight and bent positions of the "legs" and then configure the selection of a boolean to create the different positions (and still use a transform to move the part that doesn't deform).
A 2D skeleton sketch showing the start and end positions would really help here as well though...
The Onsherpa | Reach peak Onshape productivity
www.theonsherpa.com
The Onsherpa | Reach peak Onshape productivity
www.theonsherpa.com
I think that could work in some of the single-axis flexures for sure! I did a flexure like this over a year ago and didn't configure it like this but probably could have and gotten some good results. My current flexure is 2D so I'm not sure how a sketch would work. What I ended up doing was splitting the base from the other side of the flexure and just configured the offset. The flexure looks broken that way but at least the parts are positioned in the right location.
The Onsherpa | Reach peak Onshape productivity
www.theonsherpa.com
I completely remove the flexing bits and do a transform of the middle section to move it to its deflected position and then try to model the "ramps" in the deformed position but in such a way that would still work with zero deflection (if that makes any sense).
The Onsherpa | Reach peak Onshape productivity
www.theonsherpa.com