Welcome to the Onshape forum! Ask questions and join in the discussions about everything Onshape.
First time visiting? Here are some places to start:- Looking for a certain topic? Check out the categories filter or use Search (upper right).
- Need support? Ask a question to our Community Support category.
- Please submit support tickets for bugs but you can request improvements in the Product Feedback category.
- Be respectful, on topic and if you see a problem, Flag it.
If you would like to contact our Community Manager personally, feel free to send a private message or an email.
Random Onshape User Challenge #1: Cropped depiction of a cylindrical component

How the Part Studio should look:
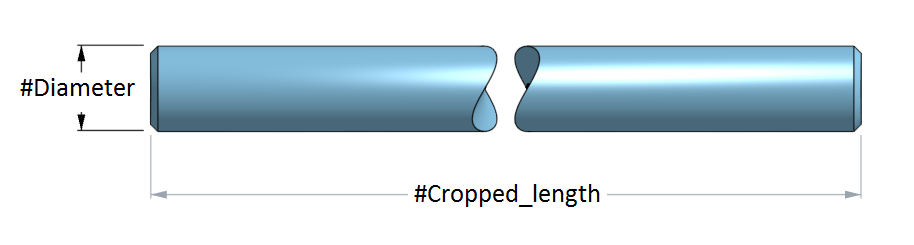
Model is to be driven entirely by the two variables named in the graphic; the cropped portions are both the same length.
Imported parts or surfaces not permitted.
ON later EDIT: the method can build the result depicted "from scratch"; it needn't be capable of modifying an existing rod.
Chamfer is optional: if included, it should be one twelfth of "#Diameter", rounded to the nearest half millimeter (or .020")
Two submissions max per user
Separate Citations for
1) simplest geometry creation
2) most unexpected concept
3) most elegant implementation
4) fewest features (as counted at the top of Part Studio feature list)
Challenge is open to users who have never been Onshape employees...
(sorry .... but employees are welcome to make informal submissions before the citations are published!)
Please share finished submissions with me but do not make them public - Message me for my email address.
Submissions close in one week from the posting date and time of this message
(hover over the date at the top of this post to see that time in your own timezone)
Tagged:
0
Comments
Good question. I intended the former, and fortuitously, that's how the first (dazzling!) submission has interpreted it.
ON EDIT: your interpretation would certainly be more useful, but I imagine the methods which will emerge from the challenge could relatively easily be applied to the real-life situation you describe.
The promptness and pace of entries so far puts me in mind of the famous line in Jaws, when he sees the size of what he's dealing with for the first time (the famous "Bigger boat" soliloquy), so I just might have a shark by the tail....
Twitter: @onshapetricks & @babart1977
If not, (and if the boat doesn't get swamped with submissions - cross fingers!), I was planning to copy a representative sample of them as renamed tabs to a single public document, so that people would only have to make a single copy in order to inspect the methods. That would also permit the judging panel (ha!) annotating or drawing attention to interesting but non-obvious aspects of particular models, without munging the original files.
Twitter: @onshapetricks & @babart1977
If no-one comes up with a better plan, I'll stick with the single public doc approach.
It would make the result available to all interested parties, in perpetuity.
That's a really ingenious idea.
You have my warm thanks (and my permission to remind me forcefully, if I have forgotten in a week's time)
Now that I think about it:
in order to do that I would have to modify a Delorean and travel back in time, in order to click on a different button ("Ask a Question" rather than "New Discussion") when I set up the topic.
What I could do instead is set up a new topic entitled "RANDOM ONSHAPE USER CHALLENGE #1: Citations and Link to submissions", and a link to that topic at the end of this topic, and vice versa at the beginning of that topic.
https://upload.wikimedia.org/wikipedia/en/3/36/GE_Turboencabulator_pg_1.jpg
https://upload.wikimedia.org/wikipedia/en/d/dc/GE_Turboencabulator_pg_2.jpg
Modelling that could be the next random challenge
As the deadline approaches I'm starting to sort through the approaches.
There's an interesting variety, and I will try to summarise the high points to save everybody having to dissect every model (which will be made public, in the form of a metric document and an inch one, with each submitted studio as a separate tab)
My summary will be on a tab in each document.
I'm not sure what the most durable and universal format would be - probably .pdf , but I'm open to suggestions)
There's one suggestion in my "specification" no-one has yet nailed - but remember, you're allowed two submissions!
<<Model is to be driven entirely by the two variables named in the graphic; the cropped portions are both the same length.
Imported parts or surfaces not permitted.
The method can build the result depicted "from scratch"; it needn't be capable of modifying an existing rod.
Chamfer is optional: if included, it should be one twelfth of "#Diameter", rounded to the nearest half millimeter (or .020")>>
Is that not in keeping with the rules set out in the post?
You did not specify that the minimum chamfer should always be 0.5 mm, just that it should be rounded.
Again, apologies!
If anyone wants to resubmit, please let me know if it's to be considered alongside, or instead of, a current submission.
Thanks a lot to all participants: there have been (from memory) around ten submissions from seven Onshape users, which is great, and it's a fertile crop of ideas and methods.
It will take me a day or two to collate the methods and document a few of the more interesting and useful revelations.
I'll start a new thread when there's something for the forum to look at and discuss.
I was intrigued by the fact that ALL the submissions which used variables to quantify the chamfer size used "lookup" to prefix any variable name wherever it appeared in the formula for the chamfer.
I'd love to know how people knew about this. It was news to me. It occurred to me possibly the Onshape app was either suggesting this, or inserting it automatically, but I can't get it to duplicate this for me, so I guess that's not it.
The strange thing is, that (at least in simple cases) the expressions seem to work just fine without it.
Twitter: @onshapetricks & @babart1977
Thanks, @ilya_baran, you're a champ.
There were many ingenious entries, and some of the ingenuity is not obvious, taking some digging before anything valuable is exposed.
It seems to me it would save a lot of wasted effort for others, now and in the future, for me to do the preliminary digging, and share that, rather than putting all the models out first and have other busy people spending time duplicating the same menial and repetitive labour.
This is particularly true on the topic of rounding the chamfer values.
Several people did this in a not very obvious but very ingenious way, in one case using multiple variables containing cascading calculations.
But the above-mentioned bug when workspaces are copied, caused these formulae to be translated (in the public document) into more complex syntax involving "Lookup" functions, making the thinking more difficult to follow.
So I'm correcting the results of that bug in the model I will be posting, as well as documenting how those formulae work.
I am also "testing" the models by changing the parameters (in a consistent way for all models) and documenting (with screenshots) how well they cope.
It seems to me that process will do justice to the effort and intelligence applied to the submissions, and make the resulting insights available to the maximum number of present and future users.
I'm back in the office now and clearing my backlog and hope to have something to show you all within the next couple of days.
FOLLOW-UP CHALLENGE ANNOUNCEMENT
(I'll start another forum thread laying out the results of the first Challenge, within the next day)OK, people, I've just about finished taking the models apart and seeing what made each one tick, and documenting what I found to save everyone else some time.... It was pretty interesting to see the different methodologies, and yet there were some striking similarities in some aspects of the outcomes.
What nobody happened to submit (and I'm a bit surprised) was a model which looked like the sample provided, AND where the two 'broken' ends fitted together when the half-shafts were butted. (That was NOT a challenge requirement, so it doesn't affect the results)
Most of them would look from the outside as though they (nearly) did, as this shows :
However sectioning reveals that they really do not fit at all :
And here's one way of trying to explain why: (note that the "bow tie" is the edge of the cut face.
NOTE that it does not coincide with the silhouette of that face, shown in alternation when the
cursor moves over the face. They need to coincide, and the bow tie needs to be symmetrical,
for the shapes to fit together)
And here's another way of looking at it (because it's a bit difficult to demonstrate :
So here's the follow up Random Challenge #1.1:
Model a shaft break which looks just like the (OP) sample for Challenge #1,
but where the half shafts are identical, AND butt perfectly together.
Please arrange things so the FRONT view corresponds to the OP sample orientation
For ease of model comparability, please model a shaft diameter of 25mm or 1 inch, a gap of 12mm or 1/2", and a chamfer of 2mm or 0.080"
No need for a variable-driven model, no need to tolerate re-sizing, no rounding of chamfer size to preferred dimensions.
Just a pure geometric challenge.
Entries close one week from the date and time of this post