Welcome to the Onshape forum! Ask questions and join in the discussions about everything Onshape.
First time visiting? Here are some places to start:- Looking for a certain topic? Check out the categories filter or use Search (upper right).
- Need support? Ask a question to our Community Support category.
- Please submit support tickets for bugs but you can request improvements in the Product Feedback category.
- Be respectful, on topic and if you see a problem, Flag it.
If you would like to contact our Community Manager personally, feel free to send a private message or an email.
Frame Tooling 2.0

So I started to create a product with the frame tool with the intention of creating a series of similar products.
However once I started getting into PLM (OpenBOM) in this case. I realized that designing in this way would not be scalable.
Since only the composite part is inserted into the assembly OpenBOM would only import the frame as a single part not an entire cut list.
Additionally even if I could get the cut lists into OpenBOM I would still have the issue in that the frame parts would be recognized as
separate parts between different assemblies.
I could get around this with some good naming conventions, properties etc. but that seems to me like it would be an error prone approach.
I developed an alternative approach that I feel might work better but being relatively new to OnShape I don't know if this is a good approach.
Here's what I did:
I created a single frame length where I could configure the length, width and also the type of profile:
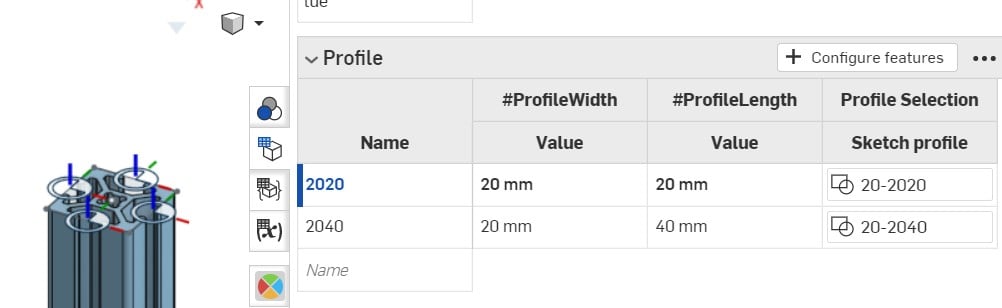
I could then simply start building my frame by inserting this part and reconfiguring it for the different dimensions:
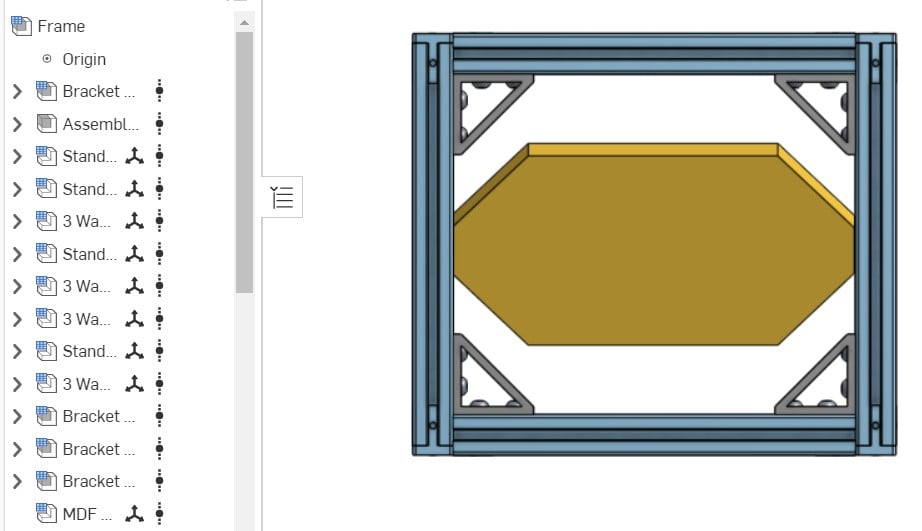
The mate connectors set with the profile work great as I could make fastened mates with the end caps on each corner,
these mates are not directly related to the edges of the profile so I can change for example from a 2020 to a 3030 frame and my mates will not break.
All the parts are configurable, which is also going to help a lot in managing my inventory that I don't carry to many different kinds of parts in stock.
There are also other advantages for example I can only use integer values for the length of the profiles.
Lastly, by building an assembly this way it should also work great for performance since everything is versioned with no part studios.
The only problem I now have is in configuring the board that goes in between my frame. It is easy to configure the width of the board but the height is trickier.
Without having measured variables in the assembly I have to create an equation for the height of the board in the configuration panel for the board itself.
Doable, but it seems to me like this workflow could be improved.
So in short I have a few questions:
1. Are my assumptions correct is this actually how my assembly is being recognized by OpenBOM or am I missing something?
2. Is this approach to creating a design recommended, I can see a lot of upsides to this way of creating an assembly
but I haven't worked that extensively in OnShape and CAD in general. I have followed the tutorials for configurations but I haven't seen them taken to this extreme.
If there is a better approach I'd be happy to be proven wrong.
3. If the approach is good I am wondering how often other people use this sort of design? I have no problem making the required
documents for this public or even making a feature Script if I have time.
Thanks,
However once I started getting into PLM (OpenBOM) in this case. I realized that designing in this way would not be scalable.
Since only the composite part is inserted into the assembly OpenBOM would only import the frame as a single part not an entire cut list.
Additionally even if I could get the cut lists into OpenBOM I would still have the issue in that the frame parts would be recognized as
separate parts between different assemblies.
I could get around this with some good naming conventions, properties etc. but that seems to me like it would be an error prone approach.
I developed an alternative approach that I feel might work better but being relatively new to OnShape I don't know if this is a good approach.
Here's what I did:
I created a single frame length where I could configure the length, width and also the type of profile:
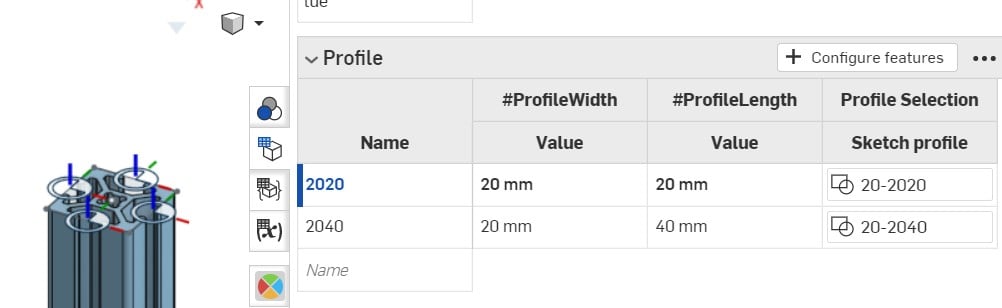
I could then simply start building my frame by inserting this part and reconfiguring it for the different dimensions:
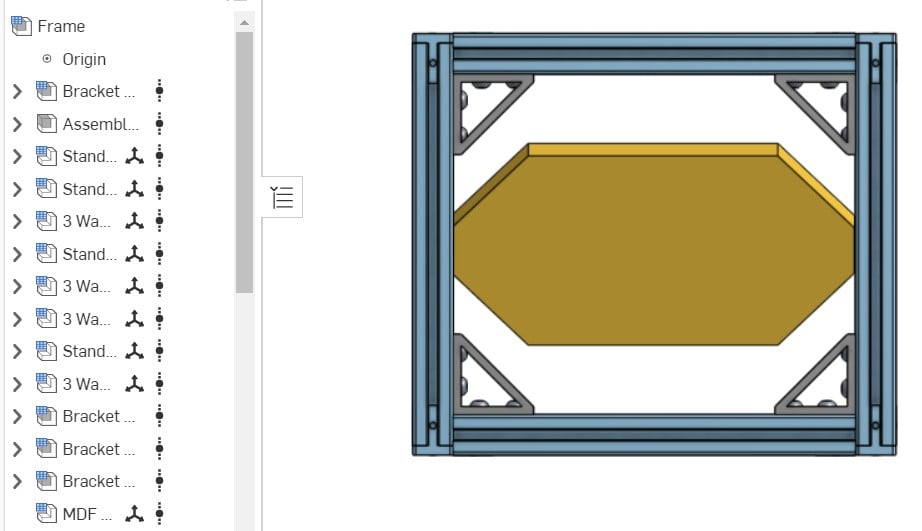
The mate connectors set with the profile work great as I could make fastened mates with the end caps on each corner,
these mates are not directly related to the edges of the profile so I can change for example from a 2020 to a 3030 frame and my mates will not break.
All the parts are configurable, which is also going to help a lot in managing my inventory that I don't carry to many different kinds of parts in stock.
There are also other advantages for example I can only use integer values for the length of the profiles.
Lastly, by building an assembly this way it should also work great for performance since everything is versioned with no part studios.
The only problem I now have is in configuring the board that goes in between my frame. It is easy to configure the width of the board but the height is trickier.
Without having measured variables in the assembly I have to create an equation for the height of the board in the configuration panel for the board itself.
Doable, but it seems to me like this workflow could be improved.
So in short I have a few questions:
1. Are my assumptions correct is this actually how my assembly is being recognized by OpenBOM or am I missing something?
2. Is this approach to creating a design recommended, I can see a lot of upsides to this way of creating an assembly
but I haven't worked that extensively in OnShape and CAD in general. I have followed the tutorials for configurations but I haven't seen them taken to this extreme.
If there is a better approach I'd be happy to be proven wrong.
3. If the approach is good I am wondering how often other people use this sort of design? I have no problem making the required
documents for this public or even making a feature Script if I have time.
Thanks,
0