Welcome to the Onshape forum! Ask questions and join in the discussions about everything Onshape.
First time visiting? Here are some places to start:- Looking for a certain topic? Check out the categories filter or use Search (upper right).
- Need support? Ask a question to our Community Support category.
- Please submit support tickets for bugs but you can request improvements in the Product Feedback category.
- Be respectful, on topic and if you see a problem, Flag it.
If you would like to contact our Community Manager personally, feel free to send a private message or an email.
What are your part number schemes?
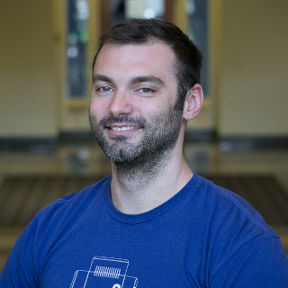
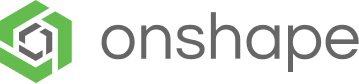
Hi all,
Can we get some feedback on what your ideal part number schemes look like? This includes, but is not limited to how/what numbers get assigned to:
Also, how is this managed today? Excel/Sheets? PLM? Magic eight ball?
Thanks!
Can we get some feedback on what your ideal part number schemes look like? This includes, but is not limited to how/what numbers get assigned to:
- Parts specific to a project
- Internal parts that are reused across projects
- OTS/supplier parts
- Non-geometric parts
Also, how is this managed today? Excel/Sheets? PLM? Magic eight ball?
Thanks!
Support & QA
3
Comments
i.e:
MT-123456 (For material)
DWG-123456 (For Drawings)
We're allowed to manually overwrite the sequential number, with the purpose of matching the sequential # to match related items. This exception is both good and bad, because it's logical, but creates inconsistencies.
I've also implemented a more "meaningful" scheme for R&D projects (typically not released in PLM system), that uses Custom Properties to auto-rename parts and assemblies in CAD. It pulls the Project Name, Product type and a unique sequential identifier, for example:
Project: Taurus
Product type: Wearable
Part Number:
TAUR-Wx-1234
There's a master table that defines the 4 character project and 2 letter product aliases. I wish there was a way in Onshape to build this type a scheme without code.
CAD Engineering Manager
XXXX-XXX-AXXX for assemblies
XXXX-XXX-WXXX for weldments
XXXX-XXX-DXXX for details (parts)
First 4 digits are the job#
Second 3 are unit#
Last 3 are for each item
So if a customer needs a spare part, they can give us that number and it will point to the exact folder on the server. Since our server is a bunch of nested folders that use the same number scheme.
So there is no need for revisions or tracking. Every time we get a repeat order, we duplicate the job folder (relevant info at least) then make improvements from lessons learned.
This allows us to stay agile and make every machine custom for that customer without them worrying about revisions either.
I also save a link to the main Onshape assembly for each unit, so Onshape also fits comfortably next to Solidworks jobs
MFGNAME-MFG#-SHORTDESCRIPTION
fasteners we just call out generically
So
MCMASTER-CARR - 60355K708 - 1in BALL BEARING
or
HHCS (M8x1. 25 x 25 lg)
This seems to be an issue that often solicits as many different opinions as there are people chatting about the subject - I think there are reasons for that, including historical industrial practices as well as users' varied personal experiences. There's a crowd that loves and won't let go of intelligent part numbers. They have their reasons, but I also think they often haven't been shown a better way. Typically because they aren't yet in a position to invest in the additional software required.
It seems to me that intelligent part numbers originated in the drafting board days, and for good reason. Physical drawings were stored in a filing cabinet, and appending the drawing-size letter to the numeric portion of the part number (12345A for example), empowered an employee to know which filing cabinet (A size, B size, C size, etc.) to search for a drawing in. That made perfect sense at the time. With modern CAD software systems there's no added benefit, as the drawings are no longer located in a physical cabinet. When that practice is carried over to cad software, however, it hinders the designer from swapping out to a larger drawing format when needed without first pulling a new part number. Since part numbers are generally issued on drawing creation rather than completion, and designers are hesitant to pull a new number just to get a larger drawing size, this often results in either overcrowded drawings containing annotations whose text size set too small, or unnecessary additional pages that are inherently more difficult to navigate.
In the current state-of-the-industry, I presume the intelligent-part-numbering advocates' toolset is often limited to a seat of CAD software, a file server share where they store their models and drawings, and an excel document (or three) where they list all the part numbers they've created. Since there's not a robust way - when using a windows file server share as your CAD data repository - to scroll through a directory and quickly determine which drawing is associated with which model, they often use the same identification number for both the model and the drawing, relying on the file extension to differentiate the two files (there's an argument for serializing drawings independently from their models, but that's another topic of discussion entirely..). To add to that, since windows doesn't permit an easy way to quickly scan or search for a file's metadata, engineering staff are forced to include all relevant information in the file name. Being forced to incorporate metadata into the filename seems to be the root cause of these multi-component, intelligent part-numbering schemes.
While they usually work for an indefinite period of time, the problem with intelligent part numbering systems is they result in one of two scenarios; a) they're simple enough that those who use them will eventually come across a situation where there is a part number duplication, or b) they are so unyieldingly complex that they're hard to use, hard to train on, and generally present a diminishing return the longer they're employed. To add to that, they are only as "intelligent" as the person who defined them, and are often only effective as long as that person is still employed at the company.
PDM systems (which are built on a database infrastructure rather than a NTFS directory) have introduced the ability to create an incredible amount of metadata associated with each part number. This meta data lives in "Custom Properties"/"Variables" in SolidWorks/SolidWorks PDM, or in "Properties" in Onshape. All of the data that the intelligent-part-number aficionados try to include in the filename - material, vendor, project, etc. - can be, and should be, recorded in the file's metadata rather than it's filename. This facilitates sequentially issued, strictly numeric part numbers (often 5, 6, or even 7 digits, depending on the amount of part numbers a company anticipates creating over the course of it's existence). These non-intelligent part numbers can be compared to a database table's 'primary key' - it becomes impossible to have duplicate part numbers. There's no need for any prefixes, suffixes, or any other information appended, but the key to making this approach work is to have a sufficiently defined UI the users interact with. The users need to be able to enter metadata (material, project, supplier, etc.) upon new CAD file creation, which can then be used to search for said document at a later date. Without a well designed user interface, the storage repository becomes a garbage-in-garbage-out "black box" where CAD files go to die, never to be found again by anyone, aside from maybe the user who originally created them (and happens to remember the part number).
Other CAD software companies have had to step gingerly around this topic because, as stated above, PDM is often an additional piece of software with an additional cost associated with it. Without sufficient explanation/education, many customers feel they are simply being up-sold yet another piece of software they don't really understand. Worse yet, is the fact that by the time they realize they do need some sort of PDM, they've often created a large amount of legacy data requiring complex manipulation prior to migrating to a PDM system. Additionally, the training required to facilitate a paradigm shift in their staff's thought patterns is significant...
The good news for Onshape is that you've integrated CAD and PDM into one offering and, as a result, you're in a unique position to be able to educate your customers right from the start without the fear of being perceived as up-selling something that isn't needed.
That said, the fact that input is being solicited seems to indicate that the documentation could use some polishing; hopefully this was helpful.
Mike
Think of a cars VIN number of a car, for a casual citizen is just a long number, but for the DMV, Law enforcement, and car service industry, the meaning ads a lot of value.
Not every employee in an organization needs to be trained or has to understand the meaning if it ads no value to their function, they can treat that number just a X amount of character, just like they would a sequential numeric component.
The simplicity of a meaningless numbers has implications downstream, many department only get a PDF of a drawing and no metadata, in order for most of them the get the custom property information, also would represent adicional software cost, and in my experience when you have 300 engineers spread over 20 different teams and multiple site, you also need a software system to generate and manage the simplest of numbering schemes.
The problem with "smart" numbers is when they are poorly designed, like in the cases you mentioned; but I wouldn'y discard a concept just because it has been poorly implemented. Any data that could "change" thru the lifecycle of part, (sheet size, mfg process, site...) should not be part of a ID number for a component.
CAD Engineering Manager
Never let the sales team manage anything!
The Engineering team should create and manage all parts and part numbers. If the sales team wants to create a part number that noly makes sense to them, then have them create a spreadsheet or something that points to the actual part number.
CAD Engineering Manager