Welcome to the Onshape forum! Ask questions and join in the discussions about everything Onshape.
First time visiting? Here are some places to start:- Looking for a certain topic? Check out the categories filter or use Search (upper right).
- Need support? Ask a question to our Community Support category.
- Please submit support tickets for bugs but you can request improvements in the Product Feedback category.
- Be respectful, on topic and if you see a problem, Flag it.
If you would like to contact our Community Manager personally, feel free to send a private message or an email.
How to mate a cross beam to slide loose / loosely in a cross slot

I'm trying to figure out how to mate a cross beam (a long beam with a cross section of a cross, plus sign, etc...) so it accurately slides in a slightly larger cross cut in a plate. The goal is something that can move up and down, tilt slightly to the left, right, forward and back, but not rotate (although in reality it would rotate slightly, this does need to be precise). This picture should explain it better than I can with words:

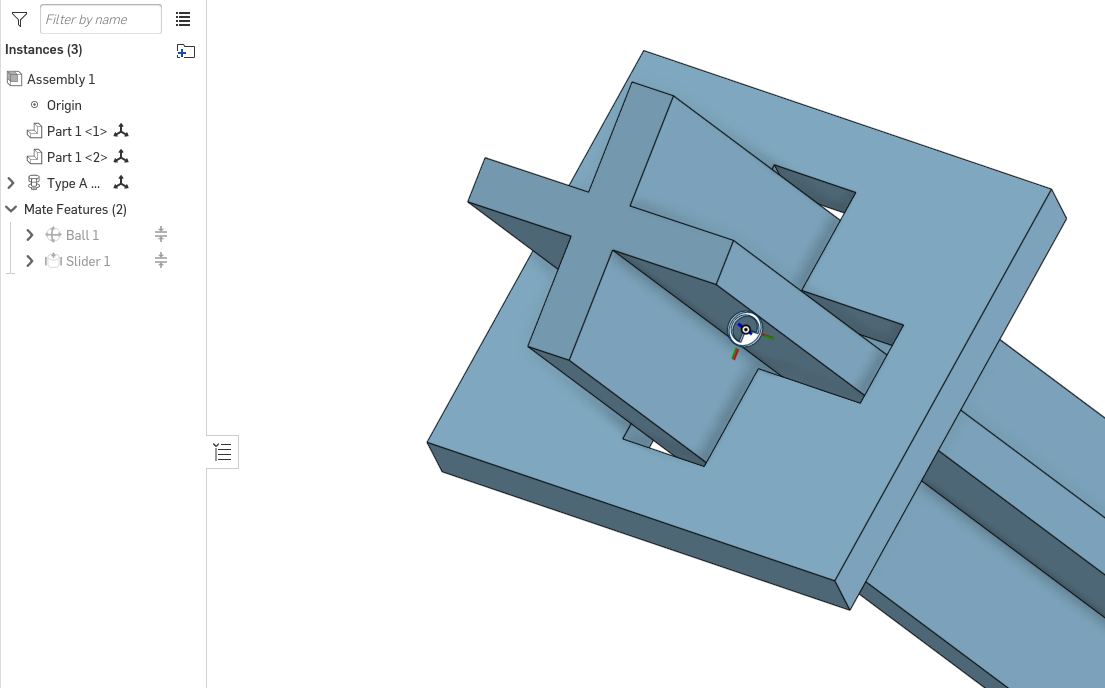
Currently, I have a washer hidden in there, and I've ball mated it to the origin, with a 20 degree limit. The I mated the cross beam to the washer with a slider. So far so good, but... It can rotate. Facepalm. The ball mate allows rotation as well as "tipping" (is that the right word?). The same sort of thing would be true of a box tube in a slightly larger square hole; it would slide, tip to the side a bit, but not rotate. This allows more tipping, less rotation, but it's the same idea. Any thoughts on how to make that move like it really would if those parts were real?
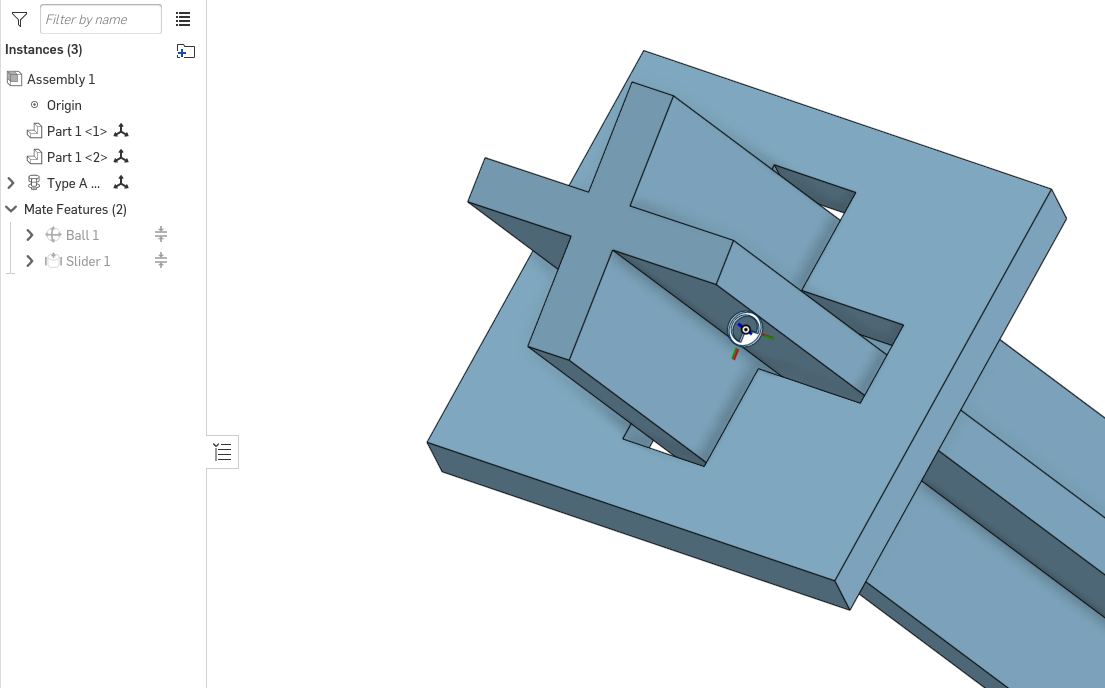
Currently, I have a washer hidden in there, and I've ball mated it to the origin, with a 20 degree limit. The I mated the cross beam to the washer with a slider. So far so good, but... It can rotate. Facepalm. The ball mate allows rotation as well as "tipping" (is that the right word?). The same sort of thing would be true of a box tube in a slightly larger square hole; it would slide, tip to the side a bit, but not rotate. This allows more tipping, less rotation, but it's the same idea. Any thoughts on how to make that move like it really would if those parts were real?
Tagged:
0
Best Answer
-
MichaelPascoe Member Posts: 2,482 PRO
Here is a combination of planar, ball, linear, and tangent mates:
https://cad.onshape.com/documents/56e99002182c670ef3ccd6bd/w/a85ec12e648b07e29cde7e93/e/373f0fd52ad5d0590392d9d6?renderMode=0&rightPanel=namedPositionPanel&uiState=63efaf7316c19e0b2f60239eSetting up the mates:
- Create a variable studio with a variable for your planar mates in case you need to adjust all at the same time.
- Create planar mates with limits on side of the slot part. This uses the dummy surface technique @eric_pesty mentioned except I used surfaces instead of sketches.
- Use another dummy part that has a straight edge running along its center and a 90 degree face for clocking. Create a ball mate, no limits, between this part and one of the mate connectors belonging to a dummy surfaces (One of the surfaces with the planar mates)
- Create a tangent mate from the center edge of the dummy part to the center vertex of the other dummy surface.
- Create a tangent mate from the 90 degree surface of the center dummy part with on of the orthogonal vertices of the side dummy surface.
- Finally, create a slider mate with limits.
Learn more about the Gospel of Christ ( Here )
CADSharp - We make custom features and integrated Onshape apps! Learn How to FeatureScript Here 🔴3
Answers
The "best practice" for this not to use a physical part like a washer but instead use a sketch or "dummy surface" to avoid having extra part(s) that could be "in the way" in the future.
Now that I think of it you can probably do it with just one part: use a pin slot mate instead of the slider for it (re-orienting the mate connectors and using limits) and then a revolute with limits (axis 90deg from the pin slot rotation axis) instead of your ball mate.
Here is a combination of planar, ball, linear, and tangent mates:
https://cad.onshape.com/documents/56e99002182c670ef3ccd6bd/w/a85ec12e648b07e29cde7e93/e/373f0fd52ad5d0590392d9d6?renderMode=0&rightPanel=namedPositionPanel&uiState=63efaf7316c19e0b2f60239e
Setting up the mates:
Learn more about the Gospel of Christ ( Here )
CADSharp - We make custom features and integrated Onshape apps! Learn How to FeatureScript Here 🔴
@eric_pesty using the sketches as guides is great input! On a similar note, here is a Fake mate connector feature for instances like this. It creates those dummy mate surfaces and excludes them from the BOM and sets them to Not revision managed.
Learn more about the Gospel of Christ ( Here )
CADSharp - We make custom features and integrated Onshape apps! Learn How to FeatureScript Here 🔴
You went all out with this! I like the "fake mate connector", arguably you could just have one a document somewhere and keep re-using it but it's convenient to be able to create one on the go like this!
That is truly amazing! You are setting an excellent example. I'm a tiny big confused as to how you decided on the value for planerLimit? Is that based on the gap between the two parts? Or also based on the thickness of the first part? e.g. if I wanted to make the plate less thick, what adjustments would I need to make to retain accurate limits?
You could draw a sketch representing the beam at its max angle. Measure the Z distance for the tolerance, then divide that by two.
Or, you could change the size to what you want, then just eye ball it
Also, depending on how often you need this kind of connection, you can just insert this assembly into whatever other assembly you need it in.
Learn more about the Gospel of Christ ( Here )
CADSharp - We make custom features and integrated Onshape apps! Learn How to FeatureScript Here 🔴