Welcome to the Onshape forum! Ask questions and join in the discussions about everything Onshape.
First time visiting? Here are some places to start:- Looking for a certain topic? Check out the categories filter or use Search (upper right).
- Need support? Ask a question to our Community Support category.
- Please submit support tickets for bugs but you can request improvements in the Product Feedback category.
- Be respectful, on topic and if you see a problem, Flag it.
If you would like to contact our Community Manager personally, feel free to send a private message or an email.
Right order of doing things in onshape?
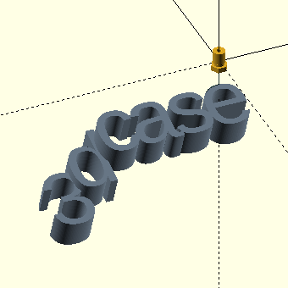
Hello everybody,
I am new to On-shape, about 2 months now. I am a machine design engineer by profession with a back ground in 2d cad. I taught myself 3d cad. First I was using OpenScad for a few years, but I decided that it has a ceiling too low for what I need. So I learn On-shape, and loving it. I did several of the learning courses already and they are really good. In just a few weeks I was designing things that I could not design in Openscad even after a few years. On-shape is clearly the better choice in this sense.
Problem is, with my background I do not possess the ingrained hardwired methods that clearly are needed to design things so all the parametric functions keep working. Even when you change something later on, you do not want to lose features or positions of parts.
Further more, I built machines from existing models, you can call it modifications if you like. So my approach is very hands on with lots and trial and error. This results in a working machine, but in On-shape it results in a fine mess.
Please can somebody point me to some learning material that specifically deals with the order in which you should be designing parts that have lots of inter-relationships with other parts?
I am afraid I cannot point you to examples, since it happens every time with almost all of the things I do. It works fine, until I decide that the base-plate on which all is mounted needs to be shorter and longer, and BAM, all my hard work from before gets undone and repairing it takes more time than starting over from scratch.
Many thanks in advance.
Yours sincerely,
Kees "3dcase" Bijker
0
Best Answers
-
eric_pesty Member Posts: 2,296 PRO
This is a bit of a tough one as there is nothing quite like experience (i.e. making a mess and doing it better the next time). You might want to check out the "top down design" learning pathway. Even if you don't end up using many of the techniques presented, it's very much a part of the larger "mindset" of parametric design and you might find it helpful.
The good thing is that I have found Onshape to be quite tolerant to changing approach mid-way through: it's generally easier to fix errors and broken stuff than other CAD system.
One really useful trick you make a change that breaks a bunch of stuff (but you can't just "undo" it because you want to keep the changes) is to open up the same thing in a separate window and go back to the history before it was broken and you can then use that to go through step by step and fix the broken one.3 -
S1mon Member Posts: 3,460 PRO
Some guidelines to keep in mind:- Think very carefully before you start modeling what orientation makes the most sense for your part/project
- Sketcher solves its constraints simultaneously
- Features are sequential
- When choosing references for sketches or features, try to use the earliest/most unlikely to change thing
- Just because you can build something a certain way, doesn't mean that it is the most robust
- When you are adding features or sketches, think about what the most likely things are to change, and allow for that
- Fewer entities in sketcher or fewer features in the model tree are often better for ease of management and rebuild time
- Make all of your sketches fully constrained, and make sure those constraints are intentional
- Name key features early - or at least when you find yourself going back and trying to remember whether that protrusion was created by Extrude 1 or Extrude 2
- At least put groups of features in folders with names that help you and others understand the model
- As your feature tree gets longer, put things in folders so that you can see the whole feature tree at a high level without scrolling
- Don't be afraid to experiment or "make one to throw away"
I tend to try to use a few layout sketches early in the tree on the default planes to control the overall size and basic shape of a part. Parts or part studios with any complexity will often have sub-areas which build off of their own set of sketches and planes. I prefer not to add planes unless absolutely necessary - I prefer to control depths of extrudes etc with orthogonal sketches. You can always go back and change the dimensioning scheme of a sketch to capture design intent better or make it easier to make the modification that you need to do. It's harder to go back and change the references of a bunch of offset planes. And whatever you do, do not have a plane called "10mm offset" which is actually now 5mm away from its reference.Simon Gatrall | Staff Mechanical Engineer | Carbon, Inc.
6
Answers
The good thing is that I have found Onshape to be quite tolerant to changing approach mid-way through: it's generally easier to fix errors and broken stuff than other CAD system.
One really useful trick you make a change that breaks a bunch of stuff (but you can't just "undo" it because you want to keep the changes) is to open up the same thing in a separate window and go back to the history before it was broken and you can then use that to go through step by step and fix the broken one.
Job 2 is to understand the parametric nature of a parametric feature based solid model.
The hardest part is to learn solid modeling (job 1) and getting the geometry correct. The next step is to allow change by creating the proper design intent and understanding long chains of depencies. Breaking up these chains and controlling them using a structured methodologies takes time to develop.
The 3 planes (top, front, right) Onshape gives you is a great start for developing a reference strategy. The simplest parametric reference is a symmetry plane using the "right plane" in onshape making the left match the right side. There are many basic training examples that reference a symmetry plane. Once you get the simpler concepts down, then you can move to the top level assembly to define references that'll drive down through the assembly stack and allow meaningful part creation.
Remember, parametric feature based solid modelers remember everything you pick, so pick wisely.
Parametric feature based solid modelling is the ultimate design style allowing predictable changes to occur. It's harder than you might think but will come with time.
- Think very carefully before you start modeling what orientation makes the most sense for your part/project
- Sketcher solves its constraints simultaneously
- Features are sequential
- When choosing references for sketches or features, try to use the earliest/most unlikely to change thing
- Just because you can build something a certain way, doesn't mean that it is the most robust
- When you are adding features or sketches, think about what the most likely things are to change, and allow for that
- Fewer entities in sketcher or fewer features in the model tree are often better for ease of management and rebuild time
- Make all of your sketches fully constrained, and make sure those constraints are intentional
- Name key features early - or at least when you find yourself going back and trying to remember whether that protrusion was created by Extrude 1 or Extrude 2
- At least put groups of features in folders with names that help you and others understand the model
- As your feature tree gets longer, put things in folders so that you can see the whole feature tree at a high level without scrolling
- Don't be afraid to experiment or "make one to throw away"
These are all guidelines not rules.I tend to try to use a few layout sketches early in the tree on the default planes to control the overall size and basic shape of a part. Parts or part studios with any complexity will often have sub-areas which build off of their own set of sketches and planes. I prefer not to add planes unless absolutely necessary - I prefer to control depths of extrudes etc with orthogonal sketches. You can always go back and change the dimensioning scheme of a sketch to capture design intent better or make it easier to make the modification that you need to do. It's harder to go back and change the references of a bunch of offset planes. And whatever you do, do not have a plane called "10mm offset" which is actually now 5mm away from its reference.
Simon Gatrall | Staff Mechanical Engineer | Carbon, Inc.
There are a couple of courses in the Onshape learning center, search for 'parametric', 'master' or 'direct modeling'. This should point you to courses about parametric modeling, working with a master model or master sketch and the very powerful tools of direct modeling on (imported) models.
You can also find video's on YouTube on these topics.
Master Model Workflows
After 30 years of parametric modeling, I've never heard it called "master modeling workflows". I ended up watching the whole coarse and it's very good. If you're trying to learn parametric modeling, I'd watch it & do it.
If you're wondering if you're any good at parametric modeling, when you go to a design review and at the end of the review your model has been updated to include all the changes, then I would say you've made it.
Kees,
Misschien mosterd na de maaltijd. Onder bit.ly/3d-eboek vind je een gratis Nederlandstalig lesboek.
Thanks for posting the question. I've often wondered about this myself and I'm going to check out some of the learning materials that were suggested in the answers.
A few tips I find helpful:
(1) I start with a high level master Part Studio that contains the basic geometry of the part that is subject to high level change. For example, if I were designing a chair, I'd start with a very primitive chair design that captures the basic shape, the seat height, the seat depth, the back height, etc, etc. For some designs this takes the form of a coarse silhouette. Then in other Part Studios downstream I derive from that master Part Studio and design in the detail. If I'd need to make changes to the seat height, back height, etc, then I'd do that in the original high level Part Studio. This way I'm separating out the high level geometry from the detail. And it means when I'm designing the detail I'm naturally considering things like whether the chair feet are a fixed height, or a proportion of the seat height above the ground.
In my early days of CAD design I was effectively designing in the way that somebody would make something out of Lego, and that got me into the kinds of trouble you described in the question - my designs were fragile and difficult to modify without breaking things downstream. This tip (1) helped me a lot with this.
(2) I've found it's OK to capture the detail in the way it'd be manufactured.
Some design purests will have a different opinion and would prefer to be unconstrained by manufacturing processes, but there is no universal right or wrong way - it's situation dependent. In your case you come from a machining background so you will have built up the instincts to be able to look at a part and quickly understand how to break it down into its machining steps. You could apply the same instincts to modelling to leverage your existing skills and account for Design-for-Manufacturability at the same time. You'd need to account for additive / subtractive appropriately. It doesn't need to get down into the detail of how a milling bit would trace a g-code path (or maybe it does, up to you). But it does mean that you can sketch a pocket, understand the milling bit you'd use to make that pocket, and dimension the inner corners of the pocket appropriately. And order the machining steps (read 'parametric CAD steps') in a way that minimises the number of times the workpiece needs to be manually moved between machines so as to optimise tolerances and manufacturing workflow. All in a way that many designers might not give consideration to.
(3) Not sure if this can be universally applied, but for my designs I organise features in a very specific order. Variables always go first. Fillets and chamfers (unless they serve some specific functional purpose) go last. Drafts that are needed to support mold release are always second last. Mates are always third last. For me, this helps with the way I put assemblies together in Assembly Studio. It does mean that I can't effectively use a filleted / chamfered / drafted surface to assemble a part together, but for me doing that would be bad practice from a DFM point of view. Consider ways to order your features to be intrinsically 'DFM safe'. And to help you to be able to efficiently navigate your way around a complex design.
(4) I have a high level Variable Studio that contains all the high level control parameters for the design - clearance values, wall thickness values, etc, etc. Unfortunately Variable Studio in its present form has limited functionality compared with local variables so this one may not be appropriate. (eg: you can't presently (1.190) search within a Document Studio for all uses of a variable studio in the way that you can for a local variable).