Welcome to the Onshape forum! Ask questions and join in the discussions about everything Onshape.
First time visiting? Here are some places to start:- Looking for a certain topic? Check out the categories filter or use Search (upper right).
- Need support? Ask a question to our Community Support category.
- Please submit support tickets for bugs but you can request improvements in the Product Feedback category.
- Be respectful, on topic and if you see a problem, Flag it.
If you would like to contact our Community Manager personally, feel free to send a private message or an email.
How to use 3D prints made of PLA for simulation
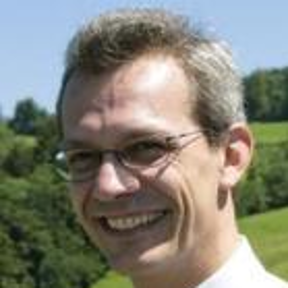
I used to create models of my parts for basic tests. A part of these tests are also stress tests. Now that there is this great possibility of simulation I would like to first calculate the effect of different load scenarios and then compare with the real values measured on the model.
To do this I need to find 2 things: First I need to find the (generally) most robust way of printing a part from an stl. Then I would like to find the material values needed. I checked in the existing library but did not find any values for PLA, so I guess I need to start from scratch?
Any input welcome
To do this I need to find 2 things: First I need to find the (generally) most robust way of printing a part from an stl. Then I would like to find the material values needed. I checked in the existing library but did not find any values for PLA, so I guess I need to start from scratch?
Any input welcome
0
Answers
Selective Laser Sintering (SLS) - SLS typically offers relatively strong parts with less anisotropy because the powder material is fused together using a laser, creating strong bonds in all directions.
Digital Light Processing (DLP) / Stereolithography (SLA) - These resin-based printing technologies create parts by curing liquid resin with a light source. While the parts can be strong and exhibit good isotropic properties, the anisotropy in the Z-direction can still be a concern if the layer adhesion is not optimized.
Fused Deposition Modeling (FDM) / Fused Filament Fabrication (FFF) - These filament-based printing technologies are the most common and affordable, but they tend to have the most anisotropic strength qualities due to the layer-by-layer deposition process. Strength in the Z-axis can be significantly lower compared to the X and Y axes, which can result in weaker layer adhesion and part strength.
Binder Jetting - In binder jetting, a liquid binding agent is selectively deposited to join powder particles. While the process allows for complex geometries, parts often have weaker anisotropic properties due to the reliance on the binder for structural integrity. Strength can be improved through post-processing techniques, such as infiltration or sintering, but may still not reach the levels of other technologies."
FEA uses:
-is this design better than that design?, I never validate a design using FEA, you have to build a prototype to validate
-I use flexural modulus of elasticity for strength to match loading case, I never yank something apart, I never use tensile strength
-Use the proper Poisson's ratio for the material
-Try to get the mesh correct
Once I get a prototype, I measure everything trying to understand material properties and dial my analysis in to be more predictive.
Linear analysis are:
-only good to 2% strain
-can't handle non-linear loading, materials & geometry (basically the real world)
If you're going to try and use FEA, then get use to analyzing, prototyping and then validating. You'll never want to enter into a design review with your analysis only. There are too many guys like myself that'll question your methods. Just one simple validation will put a smile on some old fart's face when reviewing your design and the approach you use.
There's a lot going against FEA for an engineering tool, but it's better than guessing.
The Onsherpa | Reach peak Onshape productivity
www.theonsherpa.com
Is FEA accurate? Probably not, you just have to get comfortable validating your assumptions and never skip this step.
When I sold analysis tools I'd always ask how accurate is your guess?