Welcome to the Onshape forum! Ask questions and join in the discussions about everything Onshape.
First time visiting? Here are some places to start:- Looking for a certain topic? Check out the categories filter or use Search (upper right).
- Need support? Ask a question to our Community Support category.
- Please submit support tickets for bugs but you can request improvements in the Product Feedback category.
- Be respectful, on topic and if you see a problem, Flag it.
If you would like to contact our Community Manager personally, feel free to send a private message or an email.
Options
Buggy Surfaces

I made this surface using a revolve. The profile used is that curve tangent to the inner circle. It is just a section of a circle. After making this surface,
it does not behave properly. The thicken, loft, sweep, and split features do not work on this surface.
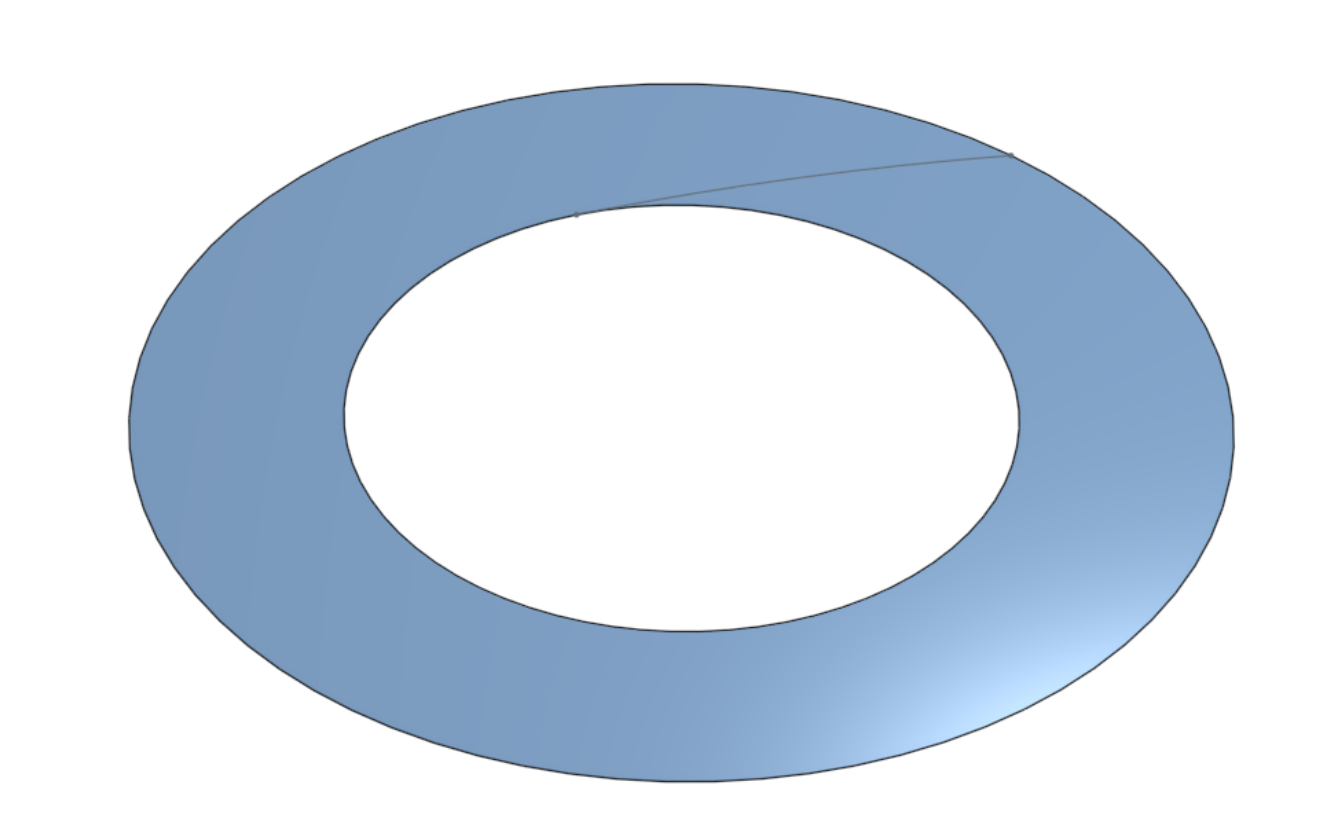
it does not behave properly. The thicken, loft, sweep, and split features do not work on this surface.
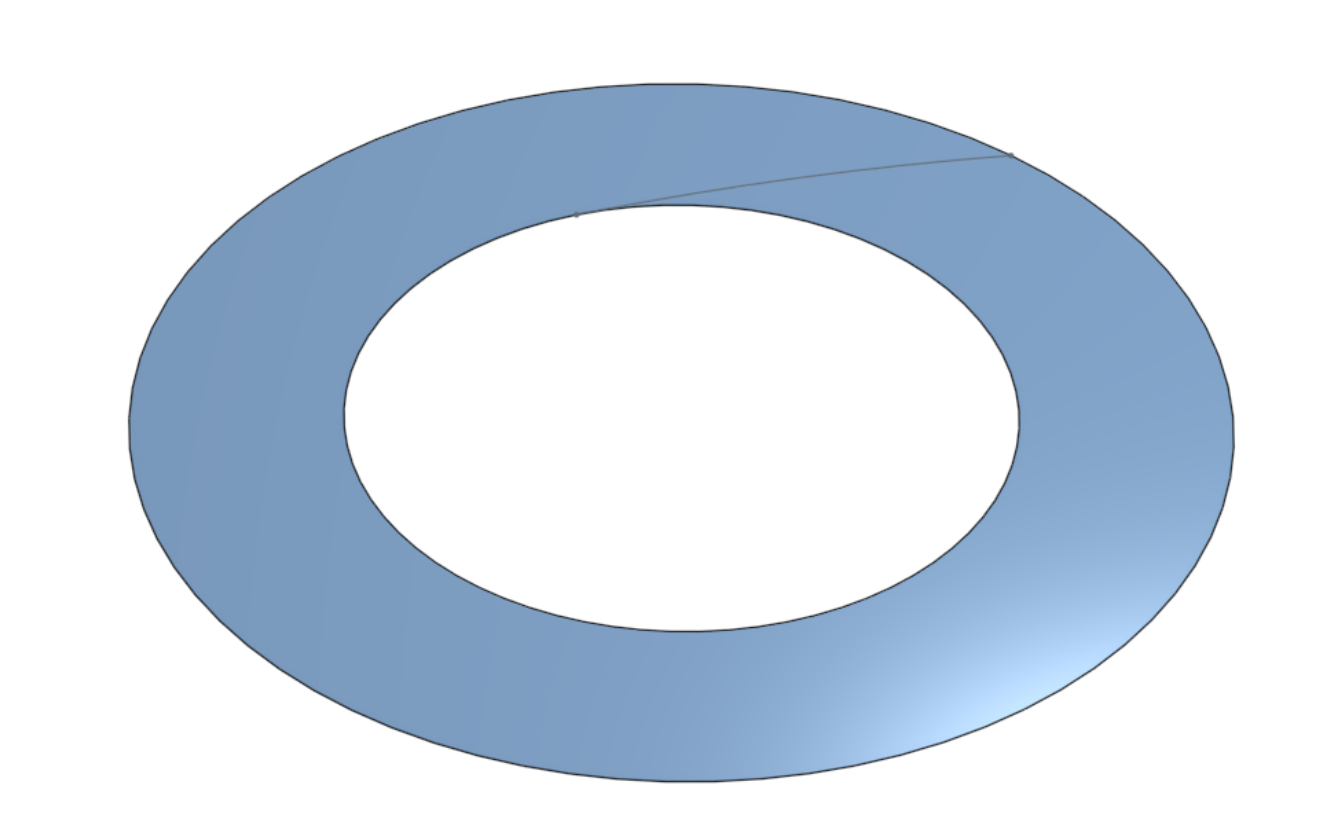
0
Answers
I created two configs: "fails" and "works". "Works" just barely works (e.g. it will only thicken in one direction), but it starts to show the issue. I added the Face curves to show how the surface is twisted and bunches up near the inner diameter.
To add to this:
Faces and surfaces that are a closed loop, like this face (or like a cylinder), must be split in two different locations. This is a current limitation due to the way Onshape handles surfaces.
So you could offset a line from your tangent line, so that there is a very small gap. This would allow it to work.
https://cad.onshape.com/documents/7c315baff9a32802372f04ee/w/f9b84c0b70daa134a57b22cc/e/447462fff2...
Learn more about the Gospel of Christ ( Here )
CADSharp - We make custom features and integrated Onshape apps! Learn How to FeatureScript Here 🔴
As for Solidworks, you might be right, but fundamentally Solidworks and Onshape, (Creo too, I think) are built on the capability of the Parasolid 3D kernel, and therefore they share may off the same challenges, limitations, and workarounds.
The Onsherpa | Reach peak Onshape productivity
www.theonsherpa.com
Now, if the discs had some kind of a curve on the surface, well right now, I don’t think it would be much different once you came up with your disc shape
At least in this case there’s not much to it.
And I’m sure somebody could find a way to shave down the amount of features or the amount of steps
https://cad.onshape.com/documents/d1a98606e25278085ca72d0d/w/fdf966ee8352ea13f91fdaaf/e/584b327585088590766df952
The Onsherpa | Reach peak Onshape productivity
www.theonsherpa.com