Welcome to the Onshape forum! Ask questions and join in the discussions about everything Onshape.
First time visiting? Here are some places to start:- Looking for a certain topic? Check out the categories filter or use Search (upper right).
- Need support? Ask a question to our Community Support category.
- Please submit support tickets for bugs but you can request improvements in the Product Feedback category.
- Be respectful, on topic and if you see a problem, Flag it.
If you would like to contact our Community Manager personally, feel free to send a private message or an email.
assembly pattern breaks original mates.

If I pattern a mated part, the original mates fail.
how come.? anyone else experienced the same thing?
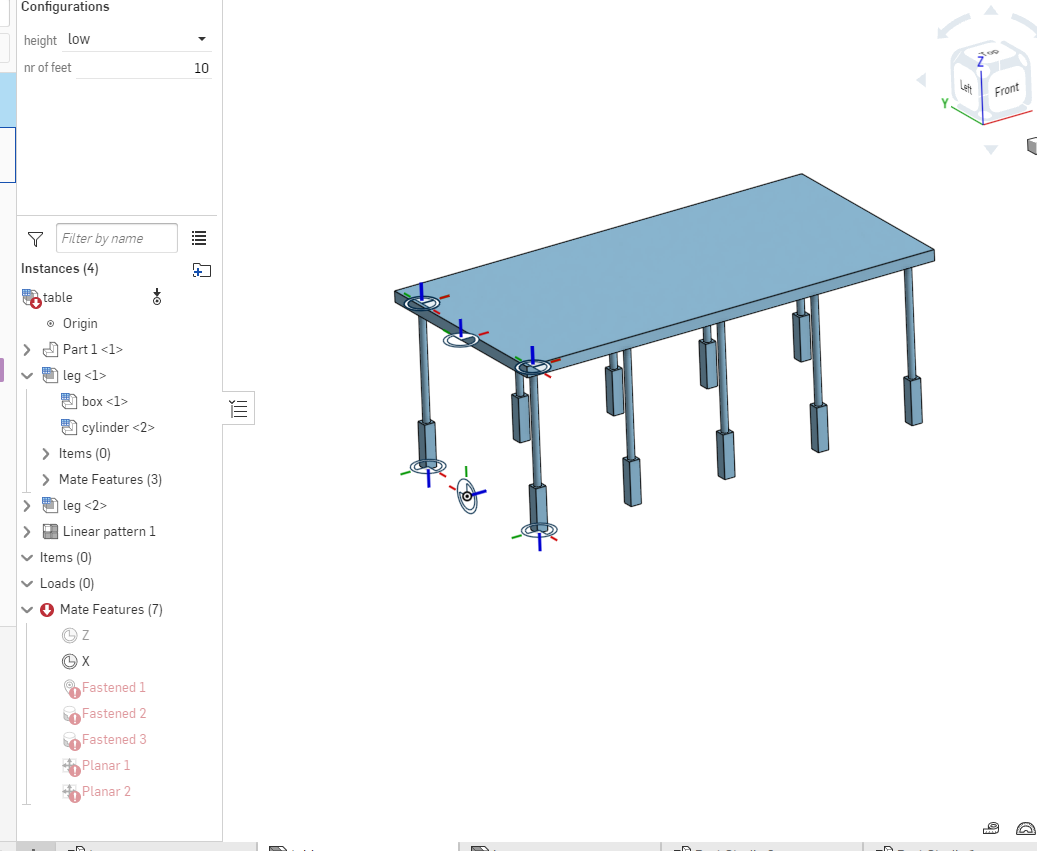
simplified example: Untitled document | table (onshape.com)
Tagged:
0
Answers
thanks fot the answer, Indeed this works. But I actually need the x&z mates... they uniquely define the position of the assembly / foot. I just don't see why patterning a constrained element should break the original constraints... The aim is to automate the design os a certain product through configurations.
This however prevents from doing so, because then must manually position the first element before applying the pattern. I havent found another way of instancing elements in an assembly other than patterning. I wonder if there is a workaround as I can't really imagine I'm the first one with this kind of challenge.
You also don't need to explicitly define mate connectors everywhere (for example at the end of the legs).
https://cad.onshape.com/documents/b8da0f74fb0555c70f580c80/w/9999557e0f4aa83e07dc9f3e/e/42d5b43bb5075efa11639671
Just curious have you used the "replicate" command much - it doesn't work exactly like a linear pattern , but can be useful for quickly populating an assembly with multiples of the same part, as long as you have some kind of reference geometry or sketch entities. I'm pretty sure this would work - but not sure if it is a time saver for you, (you would probably have to create and configure a sketch in the table top part - then use sketch points to constrain the first leg in the assembly, then "replicate" all other leg instances). I like to use replicate as much as possible - it keeps assemblies simple, but is by no means the only way to get results. Remember there is no right or wrong way to do things, only fast or slow ways.
will be looking into this.