Welcome to the Onshape forum! Ask questions and join in the discussions about everything Onshape.
First time visiting? Here are some places to start:- Looking for a certain topic? Check out the categories filter or use Search (upper right).
- Need support? Ask a question to our Community Support category.
- Please submit support tickets for bugs but you can request improvements in the Product Feedback category.
- Be respectful, on topic and if you see a problem, Flag it.
If you would like to contact our Community Manager personally, feel free to send a private message or an email.
How am I supposed to do this without a hinge mate?

Coming from a SolidWorks background, this was easily achieved with a hinge mate that had limits on how much it opened. I know I can mate the connectors with limits, but none of the connectors end up being aligned with each other in either the closed or open position. From my understanding, I cannot realign a mate connector with another part. So it's hard to know what pair of connectors to use for the limit and what the angle limits are. There are 7 different hinges in this assembly. How would you do this?
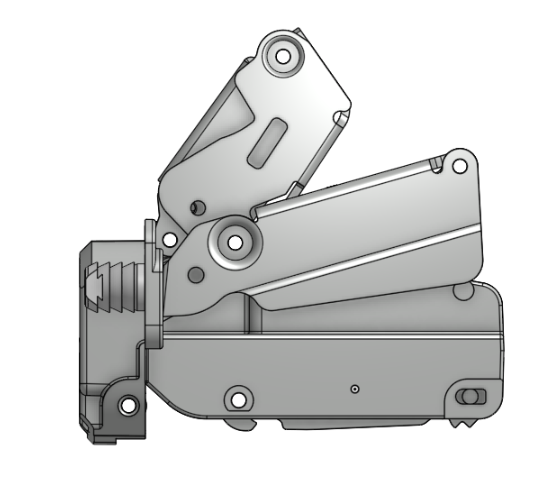
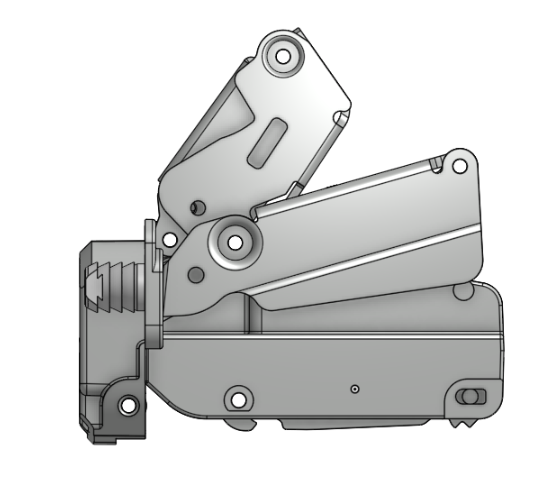
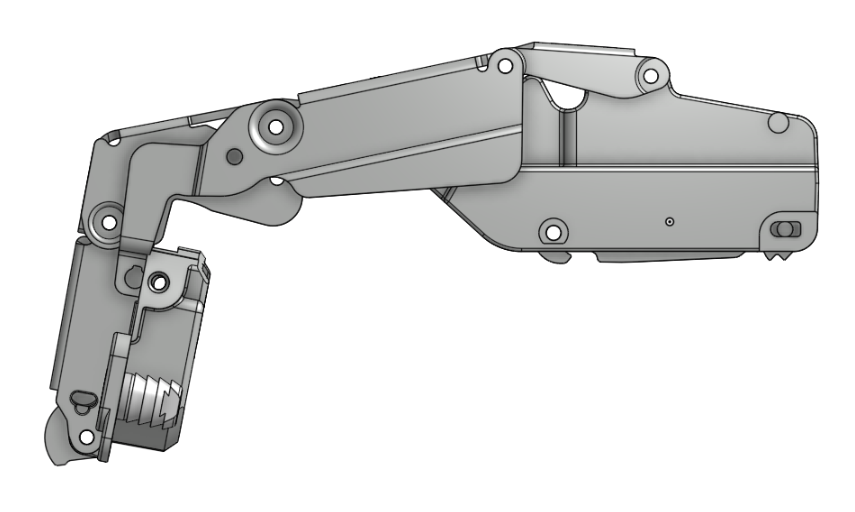
0
Best Answer
-
martin_kopplow Member Posts: 858 PRO
william_lacey140 said:For more clarification, the total angular travel distance for the cup hinge is 165 degrees. There is no singular point of rotation to define this.Hi William,I guess that is exactly what can be achieved using the parallel mate. In my above sample I applied revolute mates to all the joints, with no limits set, and applied only one single parallel mate to the two mounting plates to control the overall angle of the mechanism and deliberately limited the angle at 25 or something within the parallel mate, just to demo, for I used less joints and won't get your 165° at all. I'm sure this works with your model, too. The parallel mate does not require an explicit point of rotation to be set. Leave all other limits blank, only fill in the max. and min. Z-Angle.
1
Answers
Also presumably you drew these all in the same part studio, and possibly using a master sketch? If so, you can use those sketch points for the MC's. Then use the FS multimateconnector to assign one MC to multiple parts that all pivot about the same axis.
I want to limit the movement to be only 165 degrees, but the mate connectors are all an eight decimal place number, and there is no way that I can find to say I want the hinge cup plate to move from 0 to 165 degrees. In SolidWorks, I could put a hinge limit mate between the face of the cup plate and the front plane and that works just fine. I'm at a loss as to how to do this in OnShape.
- -142.219352
- 145.76248
- 132.93167
- -136.474798
- 168.543128
- 109.283875
- 141.352205
None of them have a difference of exactly 165 degrees. As a work around, I limited one of the revolute mates to the minimum and maximum angles based on the closed and open conditions, but it doesn't feel like this is an optimal solution. If I'm missing something obvious due to my ignorance of OnShape, please let me know. I've got almost 3 decades of drafting experience using SolidWorks and AutoCAN'T, but I've only used OnShape for about 2 months now. I wouldn't doubt it at all if this was an ID-10-T error on my part.Mates in Onshape takes a bit to get used to. Basically a mate defines degrees of freedom between tow coordinate systems (the tow mate connectors). Any degree of freedom that isn't "locked" by a specific mate type has limits available.
For example you can use a cylindrical mate and turn it into either a Revolute by adding identical limits on Z or a Slider by adding limits on rotation.
The parallel mate only locks the rotations along x and y axes so all the other values have limits available.
In most cases Onshape only needs one mate between two components but sometimes it helps to have two separate ones and the second one should be chosen to have the fewest locked DoF as possible to avoid over-constraining (hence using parallel mate in this case instead of a "planar")
Also note that you could consider not adding a limit to the hinge itself and limiting the angle the door itself in a higher level assembly (this does help performance as the software doesn't have to simultaneously solve the limits on the top and bottom hinge of a door.
That is how I use it in SolidWorks. I leave it as a flexible assembly and use the doors to control the opening and closing of the hinge. This was done more as an example of how to overcome a more complicated hinge mate and learn how OS handles it. If I am going to use this, I would certainly leave the hinge as flexible and control the limits in a higher level/parent assembly.
Simon Gatrall | Staff Mechanical Engineer | Carbon, Inc.
One more tip I found useful is to not get to "hung up" on the name of the different mates: think of the names as example of an application that requires these specific degrees of freedom. The "pin slot" is one of the more interesting example as it has applications much beyond a pin sliding in a slot. Here's a discussion on that topic: