Welcome to the Onshape forum! Ask questions and join in the discussions about everything Onshape.
First time visiting? Here are some places to start:- Looking for a certain topic? Check out the categories filter or use Search (upper right).
- Need support? Ask a question to our Community Support category.
- Please submit support tickets for bugs but you can request improvements in the Product Feedback category.
- Be respectful, on topic and if you see a problem, Flag it.
If you would like to contact our Community Manager personally, feel free to send a private message or an email.
Part numbers in configurable subassembly
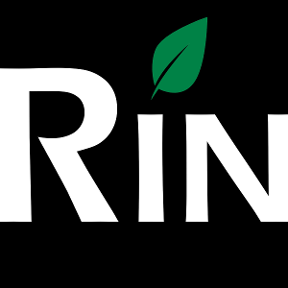
I'm trying to get better on matching part numbers between erp and cad but I find it difficult with so many re-usable parts in our designs. Multi-part studios is the best way to design our (furniture) products as they have a lot of connectors that require certain tooling on connecting panels and we already have some feature script automation to create these in part studio.
So separating each part to it's own studio is not solution for us.
We use often configurations to combine similar designs into same and then configure also part data (name, desc, part.no) for each. It's ok but sometimes a bit frustrating if there is say 3 parameters with 3 options on each and only one parameter has real affect on certain part; so 3 part versions exist in erp but we need to create 27 rows to define part number for each possible combination.
I have already sent improvement request to be able to choose 'any' as configuration value if it has no affect on certain part.
But the real problem is with subassemblies that are defined with ~10 different parameters to create 'standard unit' used on main assembly. Part studio with predefined configurations lives in another document and a version of it is used to create 'standard unit' subassy.
How to write part data for such parts?
Current way where part data is handled in part studio's configuration table is awkward especially when parts live in other document and each new subassembly configuration requires new part versioning even though it has zero affect on existing designs. And it's a disaster with any higher amount of parameters driving the design.
The most convenient way would be adding part data directly from assembly where all these configuration values are defined. We can already access part 'properties' from assembly part list RMB menu but if part lives in version data is greyed out. And if part is in same document property will be added as 'general' for all configurations.
First step would be possibility to add part data for only specific configuration that is used in assembly. It could automatically create table into part studio configurations.
But how to set part data per configuration for version locked part without creating new version every time?
—
Simple example for those who got lost:
You have document A with piece of wood panel that has configured values for X and Y dimension.
Then you have document B where you add this panel and use configuration values to get the desired size — and then you wan't to add name, description and part number for this certain size without creating a new version for doc A.
Any thoughts?
Comments
If you edit the BOM in your assembly you get the automatic creating of a row of "configured properties", unfortunately you cannot edit the name or part number of a version (i.e. you cannot check the "edit in version" check box for these properties)…
For your request of setting "any", you can now set the configuration input to "exclude from properties" which removes it from the configured properties table (only currently available for part studios though…)
In our case we became a bit frustrated by the hard rules of the part number property (we often want to use the same PN for an assembly and a part, specifically for sheet metal parts with PEMs inserts) and we have a separate property called "vendor part number" (and one called "vendor"). For our own "custom" parts, we set the vendor as ourselves and effectively duplicate the part number value into the "vendor part number property". This "vendor part number" is the one we use in BOMs rather than the built-in part number.
It does add a layer of "manual" entry (and a source of mistake) but it does give us the flexibility to set the property directly from the BOM. We also don't really care too much about the "name" as we rely on the description field. You could use a feature to set the name to include the "X and Y" dimensions automatically (and dynamically). See property explorer FS.
Thanks for the input @eric_pesty I haven't really used bom too much as we still have too many parts without proper data but I need to look if we could do something similar using 'vendor code'.
I think using option 'any' would be better than 'exclude' in part studio with multiple parts as I suppose 'exclude' will affect them all and any could be used in different columns for different parts.
For example a simple shelf with top, bottom and sides. Parameter 'frame width' doesn't affect on side parts but it can't be excluded as it affects to top and bottom length.
We don't benefit from including dimension into name as the main idea would be to synchronize part id between cad and erp .. and not to create bunch of copies of already existing parts in the long run.
I will still model some copies in multi-part studios when convenient but I will name them dummies and replace with coded part in assembly.
Right, if you have some parts that need different parameters in your part studio then the "exclude" could be an option.
One potential workaround (not sure how much setup it would require to get there…) would be to keep your "master" part studio that generates all the parts and then derive each "type" of part into a new part studio from there where it only has the "required" configuration inputs (linked to the part master part studio).
Here are some examples of this workflow:
https://cad.onshape.com/documents/d2d3382aa18189471db96624/w/bfdb4819bc7e743e462a92ad/e/09d28899141e7820ed474b95?configuration=List_CfK1kQIjtoTHRj%3D_1&renderMode=0&tangentEdgeStyle=1&rightPanel=configPanel&uiState=671aaf99037c9c522fe0965d
Performance can be an issue with the added step of deriving the part, however you can always set the derived part to reference a version (rather than workspace) of the master part studio, which would mitigate that.
If you use these derived part in an assembly you get around the extra config input issues, the issue is that you have to set the configuration of the different parts independently (can't just import the whole part studio with the same config if that's what you were doing…)
We use derive with drawers to insert standard parametric box into part studio and then model desired front for the box to avoid having copies of other parts.
This then becomes subassembly which is still parametric and can be configured for different chests of drawers.
Drawer boxes live in separate document to make it more convenient structure to use in different product design documents.
I have now created custom properties and make my own default bom and leave out built-in part no. etc - this might be the solution I'm after.
Now I have 'PartCode' and 'PartName' on top of my property list and BOM with Item, Qty, Pcode, Pname.
I can now set these directly from assembly and when I change configuration it only clears out values from parts that actually change. Hooray!!
I'm actually impressed how it turned out - well done Onshape and shame on me not following all the updates close enough.