Welcome to the Onshape forum! Ask questions and join in the discussions about everything Onshape.
First time visiting? Here are some places to start:- Looking for a certain topic? Check out the categories filter or use Search (upper right).
- Need support? Ask a question to our Community Support category.
- Please submit support tickets for bugs but you can request improvements in the Product Feedback category.
- Be respectful, on topic and if you see a problem, Flag it.
If you would like to contact our Community Manager personally, feel free to send a private message or an email.
When does shell create radii to hold uniform wall?
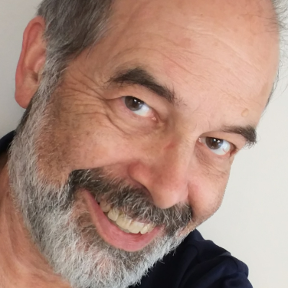
@armindilo Has a nice elegant solution for intersecting pipes at https://cad.onshape.com/documents/f6fec9930959f5e092add16f/w/cd8884dce5ef97e6734a4977/e/651a8e3cd8465d8cbf73b4ef see forum discussion at https://forum.onshape.com/discussion/comment/24264#Comment_24264
Shell working here was a surprise to me. I expected radii would be created at internal intersection (see picture). So my question is - What are the rules for shell? When will a fillet/round be created to hold even wall thickness?
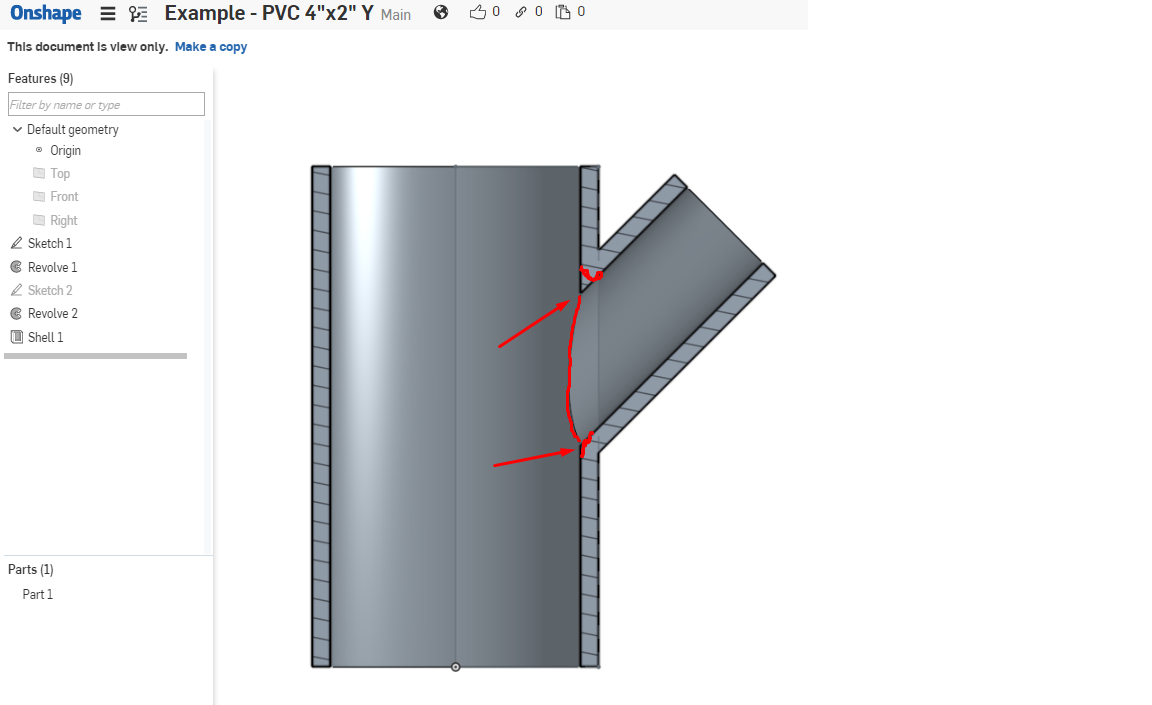
Shell working here was a surprise to me. I expected radii would be created at internal intersection (see picture). So my question is - What are the rules for shell? When will a fillet/round be created to hold even wall thickness?
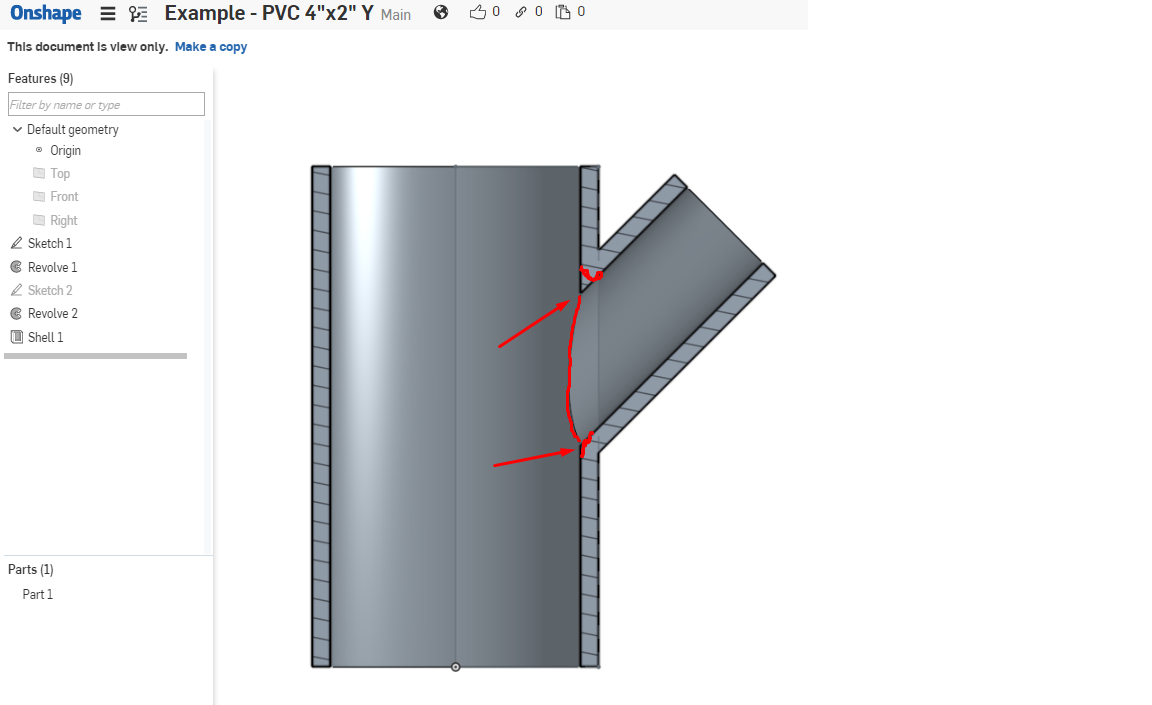
www.accuratepattern.com
1
Best Answers
-
Jake_Rosenfeld Moderator, Onshape Employees, Developers Posts: 1,646
Hi Bruce,
This isn't my area of expertise, but I tried something else as an experiment. I copied @Armindilo 's document and added a fillet to the joint between the two pipes before the shell and got the following result:
I suspect that our geometry kernel has a hard decision to make when faced with a non-tangent intersection, and solves it by extending the intersecting faces and taking an intersection of their shells. If you need constant wall thickness for something in the future, I would suggest adding a very small (or larger, appropriately sized) fillet to any non-tangent edges.Jake Rosenfeld - Modeling Team6 -
bruce_williams Member, Developers Posts: 842 EDU
I did some experimenting and answered my question. A fillet is required to force shell to round the corner holding 'even wall'. Now I see this is a very good behavior as it gives an option for the corner on inside. Note the pictures below, I have the smallest fillet allowed (greater than 3.938 e-4; or 1 micron) and then shell creates a radius to hold wall thickness. By suppressing the fillet, shell creates a sharp corner on inside of part. NICE! Have it your way....
www.accuratepattern.com3
Answers
This isn't my area of expertise, but I tried something else as an experiment. I copied @Armindilo 's document and added a fillet to the joint between the two pipes before the shell and got the following result:
I suspect that our geometry kernel has a hard decision to make when faced with a non-tangent intersection, and solves it by extending the intersecting faces and taking an intersection of their shells. If you need constant wall thickness for something in the future, I would suggest adding a very small (or larger, appropriately sized) fillet to any non-tangent edges.