Welcome to the Onshape forum! Ask questions and join in the discussions about everything Onshape.
First time visiting? Here are some places to start:- Looking for a certain topic? Check out the categories filter or use Search (upper right).
- Need support? Ask a question to our Community Support category.
- Please submit support tickets for bugs but you can request improvements in the Product Feedback category.
- Be respectful, on topic and if you see a problem, Flag it.
If you would like to contact our Community Manager personally, feel free to send a private message or an email.
Very large bend radius in sheet metal
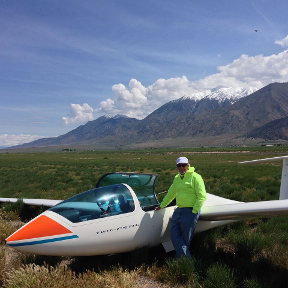
I'm having a hard time imagining how to do this in the sheet metal feature:
https://cad.onshape.com/documents/c906a6bdcf50136ee9dbb9e1/w/9f6d794f5ac613eb6ba6aa67/e/46b04f2749c981d246970793
The part is to be made of several sheets of 1/8" steel welded together. I can easily see how to model the flanges but the large 9" bend radius is not clear. There will be alignment tabs on the sheet parts to make the welding more accurate.
https://cad.onshape.com/documents/c906a6bdcf50136ee9dbb9e1/w/9f6d794f5ac613eb6ba6aa67/e/46b04f2749c981d246970793
The part is to be made of several sheets of 1/8" steel welded together. I can easily see how to model the flanges but the large 9" bend radius is not clear. There will be alignment tabs on the sheet parts to make the welding more accurate.
0
Best Answers
-
konstantin_shiriazdanov Member Posts: 1,221 ✭✭✭✭✭
for now only possible approximate solution
https://cad.onshape.com/documents/c9557f3e5ba998390a3ba684/w/9fda3d90ee14408120113961/e/201ae0ce628c588ca2aa9eb0
5 -
bryan_lagrange Member, User Group Leader Posts: 887 ✭✭✭✭✭
Hey Bill
To create this part we create it two ways in the shop.
1) bend the 90 degree tabs then make slight bends at the tangent of the large radius. The slight bends indicate a start and stop point when we bring the part to the slip roller to roll it.
2) we use what is called a bump bend method which is to make incremental hits until the large radius is achieved.
If you want to gage bendline dimensionally and the angle to hit I have use the method of creating a polygon with large amounts of sides. The more sides you have in the polygon the smoother the radius will be.
Here is an example I quickly did.
https://cad.onshape.com/documents/6d8dd61c55bb52c67c801026/w/70d3460e1114046d5a0674ca/e/4572cd1dd62c7697d7c36d82
Hope this helps
5 -
bryan_lagrange Member, User Group Leader Posts: 887 ✭✭✭✭✭
@bill_daniels Check out part studio 2. I did a tighter ploygon to smooth it out. If you had the time you could smooth it out even more but making more sides to the polygon. 50 is the limit I see for the polygon tool in Onshape so you have to go manual to go further than 50.
https://cad.onshape.com/documents/6d8dd61c55bb52c67c801026/w/70d3460e1114046d5a0674ca/e/37ae4a93e995b4501d125517
5
Answers
https://cad.onshape.com/documents/c9557f3e5ba998390a3ba684/w/9fda3d90ee14408120113961/e/201ae0ce628c588ca2aa9eb0
To create this part we create it two ways in the shop.
1) bend the 90 degree tabs then make slight bends at the tangent of the large radius. The slight bends indicate a start and stop point when we bring the part to the slip roller to roll it.
2) we use what is called a bump bend method which is to make incremental hits until the large radius is achieved.
If you want to gage bendline dimensionally and the angle to hit I have use the method of creating a polygon with large amounts of sides. The more sides you have in the polygon the smoother the radius will be.
Here is an example I quickly did.
https://cad.onshape.com/documents/6d8dd61c55bb52c67c801026/w/70d3460e1114046d5a0674ca/e/4572cd1dd62c7697d7c36d82
Hope this helps
Twitter: @BryanLAGdesign
https://cad.onshape.com/documents/6d8dd61c55bb52c67c801026/w/70d3460e1114046d5a0674ca/e/37ae4a93e995b4501d125517
Twitter: @BryanLAGdesign
At the moment going from rolling the part or bump forming the curves is something the shop I send these to has a conversation with me on a case by case basis. Allowing us to model the rolled parts with bump forming would allow us to simulate the bump forming and pass that on to the shop as an option with us deciding ahead of time what bump steps sizes are acceptable to us.