Welcome to the Onshape forum! Ask questions and join in the discussions about everything Onshape.
First time visiting? Here are some places to start:- Looking for a certain topic? Check out the categories filter or use Search (upper right).
- Need support? Ask a question to our Community Support category.
- Please submit support tickets for bugs but you can request improvements in the Product Feedback category.
- Be respectful, on topic and if you see a problem, Flag it.
If you would like to contact our Community Manager personally, feel free to send a private message or an email.
How do I get smooth slots from splines?

Hello, when I sketch a spline and use the slot or offset tool, the slot or offset lines becomes rather jagged and they don't follow the curves as you would expect.
I've read that this could just be Onshape simplifying the sketch for a better performance and is just visual, selecting the slot will automatically smooth the lines so that confirmed it for me. However, if I export this slot as a DXF and prepare to cut the slot in sheet metal, it exports the jagged lines and creates a rough edge like this: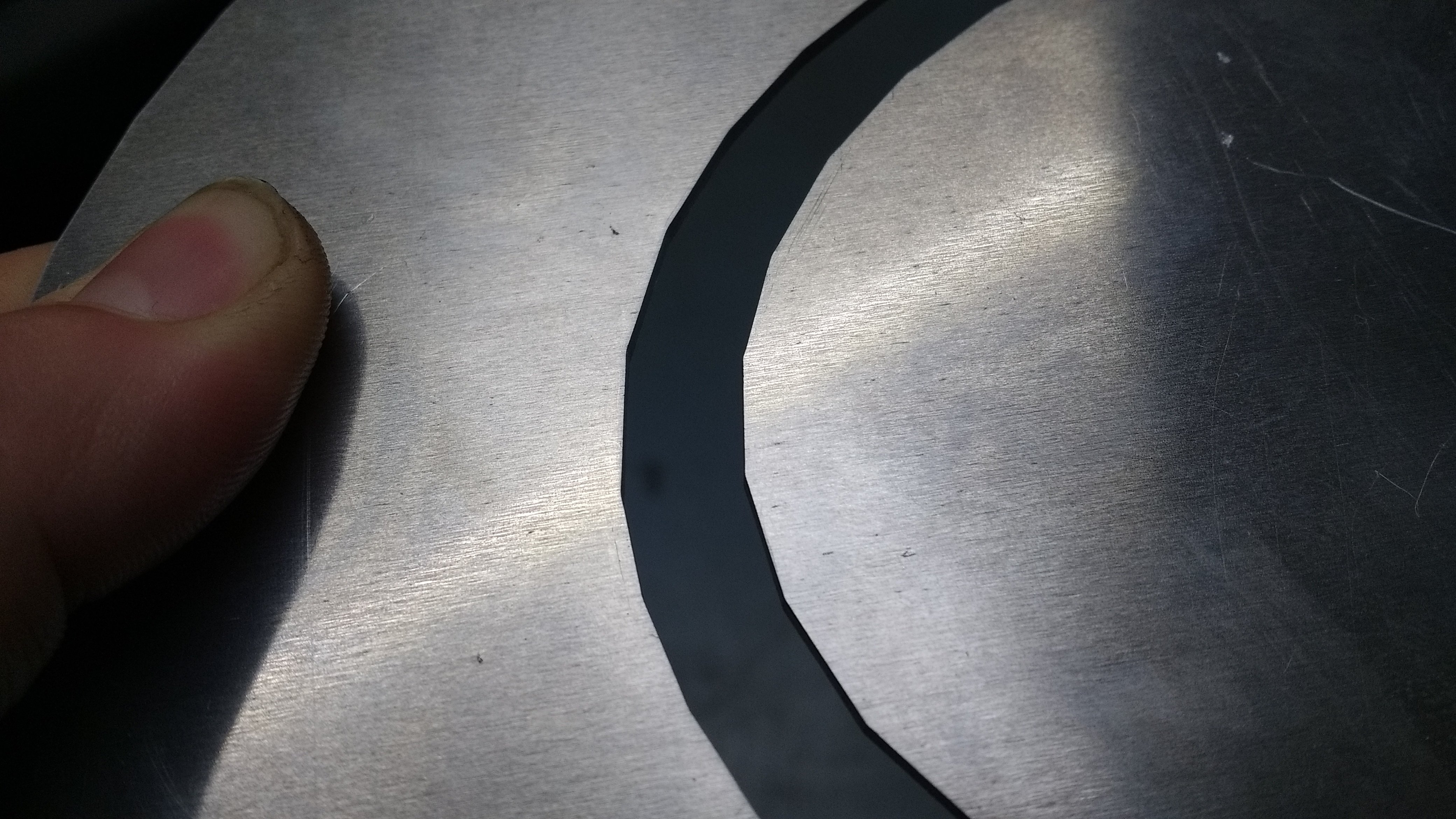
How can I create smooth lines like they should be?
I've read that this could just be Onshape simplifying the sketch for a better performance and is just visual, selecting the slot will automatically smooth the lines so that confirmed it for me. However, if I export this slot as a DXF and prepare to cut the slot in sheet metal, it exports the jagged lines and creates a rough edge like this:
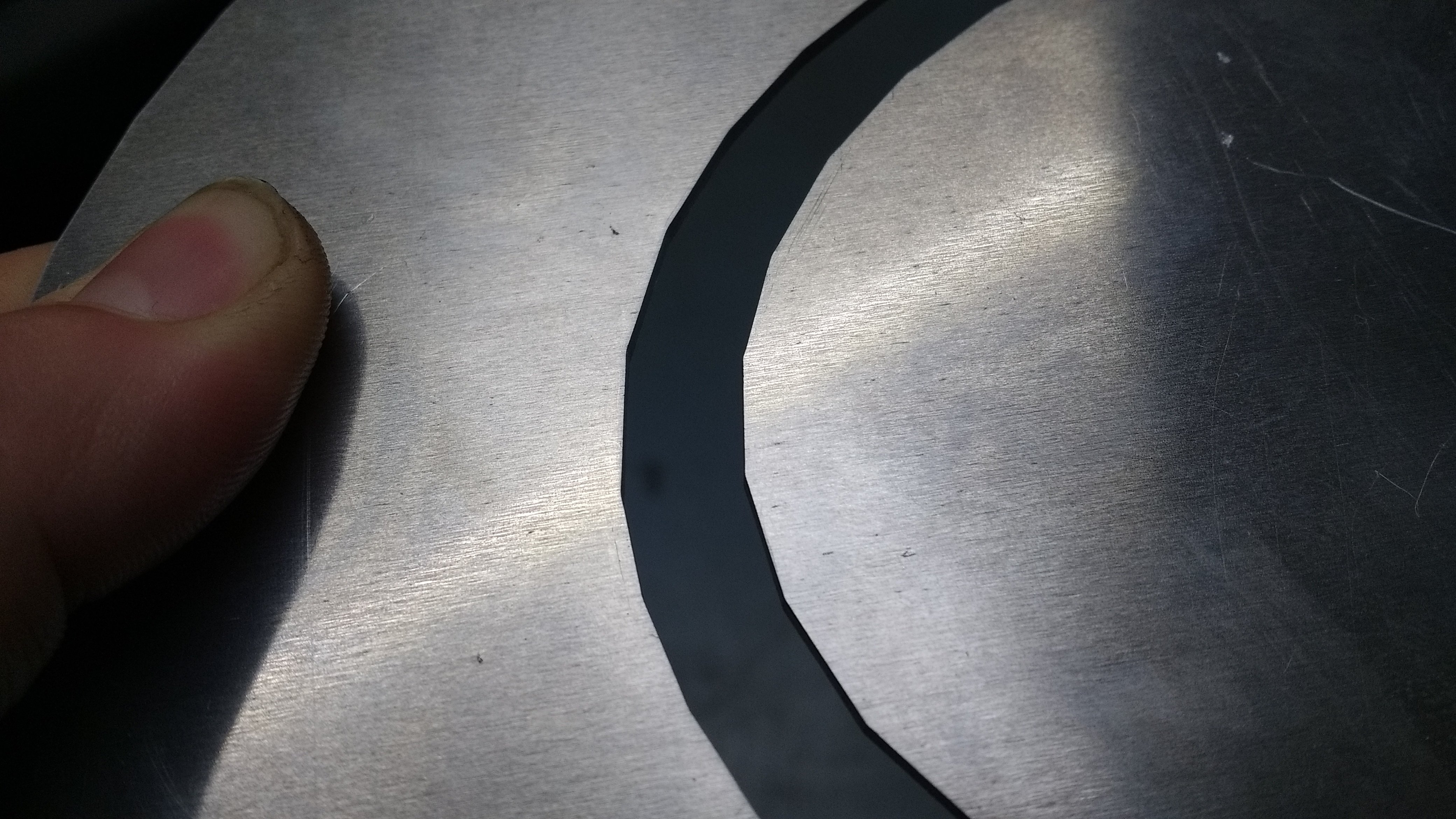
How can I create smooth lines like they should be?
0
Answers
In Onshape you need to export STEP with your model, then open this STEP with DesignSpark and then save it as dxf.
What is important, is that DesignSpark when do save as dxf it actually saves the current view from the view port. In your case you need to get view perpendicular to the face you need in dxf. For other users who looks for software to make illustrations for instruction (@3dcad), this is the way.
projektowanieproduktow.wordpress.com
We are very interested in learning why the manufactured sheet metal parts looks the way it does. To understand whether this is on us, we would very much like to see the document! Additionally, the dxf file supplied to your manufacturer would also be helpful. If you would upload the dxf you sent to the document and share it with us (support), we would love to look at it! I hope you take advantage of this offer
https://cad.onshape.com/documents/1d084eff273f2172e34828f2/w/7732e0373a516a4742828be5/e/5201ee15818ef6e20ca15d0e it is shared with support.
Even CamBam do see differences:
projektowanieproduktow.wordpress.com
projektowanieproduktow.wordpress.com
(a) All those extra layers are mildly annoying.
(b) It also winges about all the lines being open vectors in for example rectangles.
Both are easy enough to fix so I've not raised them as a problems in the past but if dxf export is being focused on then thought it worth mentioning.
Cheers, Owen S.
HWM-Water Ltd
projektowanieproduktow.wordpress.com
In the image below is a view of the slot next to a true circle on the right and a filleted edge on the left, all appear jagged.
The slot sketch is selected, highlighting its actual curve.
This same part, exported via Onshape into a DXF format and opened in QCAD shows the fillet and circle are correct but the slot is still jagged.
Here's the slot from above: https://cad.onshape.com/documents/7fc6dfa67e4677f6d8d50f09/w/adfce6db37bb69c3ef626463/e/208f9f45f4ef09c25ddd7cde
projektowanieproduktow.wordpress.com
I'm currently downloading Designspark Mechanical, so I will test that out.
Please dont forget about us, we want to fix it - please share the doc (and the DXF and the name of your manufacturer!)
again it's shared with support.
This time I've decided to create enough specific cv points layout so I could find it in dxf without knowing the exact meaning of each line of dxf (yes we can open dxf with a text editor).
It's a simple spline with cvs at:
x:0 y:0
x:0.3 y:0.3456789
x:0.6 y:0.56789
x:0.9 y:0
For any program to be able to recreate spline it must know cvs position and curve degree. Now if you search for just a row 3456789 you will find nothing in Onshapes dxf. You can also search for word spline and you will find only two lines with only object class denotation.
For comparison, I've created exactly same spline in DesignSpark and export it in dxf. This time you can find both values 3456789 and 56789. Also you have same class denotation lines about spline but also data about spline itself.
Original file from DesigSpark and dxf are attached to my document from the link above.
It can't be that manufacturer might have a problem to read Onshapes dxf properly, Onshape didn't write data about spline to dxf.
projektowanieproduktow.wordpress.com
Michal and @owen_sparks, what are your output settings on your DXF/DWGs? Not all file types are the same or will yield identical results. There is a decent sized matrix of options here.
Cheers, Owen S
HWM-Water Ltd
projektowanieproduktow.wordpress.com
Because of my experience with multiple CAD applications, I tend not to use drawing exports, I use them only for documentation, not for CNC.
That was my mistake, I was wrong. I also must review my initial advice here: https://forum.onshape.com/discussion/7156/onshape-vs-rhino#latest maybe best is to export from drawings, I will look at that.
To get spline in dxf you must use drawings (for example adjust drawing format and use 1:1 scale) all should work except DXF Release 11-12.
We won't get spline if exported from Sketch of by picking a face and then exporting it as DXF, these will not work, they don't contain any data about spline.
I wish exports from Sketches and faces will be fixed, but since now I don't consider it urgent.
projektowanieproduktow.wordpress.com
projektowanieproduktow.wordpress.com
Cheers, Owen S.
HWM-Water Ltd
projektowanieproduktow.wordpress.com
The solid image will show tessellation which is visual and not the geometry's true curvature. This was pointed out in a previous post.
Splines are mathematically continuous and accurate. G-code can't handle them so CAM packages have issues when engineers use them. I wish after all these years we had a better method for handling splines in CAM.
CAM systems can either linear interpret or circular interpret splines. Most will linear interpret the spline causing huge CNC files. I don't care how far done the "tolerance" goes, you'll always see facets. More advanced interpolation will map arcs onto splines reducing the CNC file size. Arcs are planar so for 3D splines you'll need 5 axis. All interpolated tool paths don't look that good. I hate when they circle interpolate my splines, but there's no other way. It effects the way light reflects off of your part and makes it appear dull & bland. This really needs to be addressed.
The solution will be to send the spline's coefficients to the motor controller and have it resolve down to the motor step. I haven't heard of any one trying to do this, but it's time.
Ask the CAM BAM people to figure out splines without interpolation. This would be new and exciting. Stay away from dxf and all the bad it's brought into the world.
This is my opinion,
Next thing I would like to address your concerns with G-code not supporting splines.
Do you know G06.2 command?
CAM developers were working on that like two decades ago. Here's a Fanuc manual form 1999:
http://www.kfilipowicz.zut.edu.pl/Programowanie/FANUC/0010__GE_FANUC_User_Manual.pdf
go to page 105 on that pdf doc, or on page 79 if you read from the paper, it's chapter 4.13 NURBS INTERPOLATION (G06.2)
This command (G06.2) is doing what you're asking it sends NURBS data directly to the motor controller.
Of course, even then it's just an approximation with a tolerance equal to machine resolution. I wish you know what I mean by machine resolution. Stepper motors are working by moving a fraction of full rotation (step) and that translates into an incremental linear move, usually, something like 0.001mm and this is your machine resolution.
We can speculate about (dream about), not using stepper motors and build an analog device. I can imagine linear and circular motions being implied, maybe NURBS also? Eventually, you are the engineer here.
projektowanieproduktow.wordpress.com