Welcome to the Onshape forum! Ask questions and join in the discussions about everything Onshape.
First time visiting? Here are some places to start:- Looking for a certain topic? Check out the categories filter or use Search (upper right).
- Need support? Ask a question to our Community Support category.
- Please submit support tickets for bugs but you can request improvements in the Product Feedback category.
- Be respectful, on topic and if you see a problem, Flag it.
If you would like to contact our Community Manager personally, feel free to send a private message or an email.
Importing models (Step, IGS) best practices.
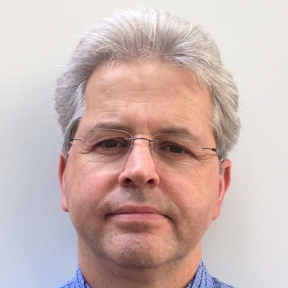
I imported a Step file into a part studio and plan to use the geometry to create tooling. The tool will consist of multiple parts.
As in most cases with imported models the Step file is imported it is not located in the desired location i.e. origin,top,right, front etc. This in return will cause issues if I want to create a drawing. I do not want to use the "named views" as a workaround a someone else suggested in the forum.
What is a recommended best practice?
Best Regards,
As in most cases with imported models the Step file is imported it is not located in the desired location i.e. origin,top,right, front etc. This in return will cause issues if I want to create a drawing. I do not want to use the "named views" as a workaround a someone else suggested in the forum.
What is a recommended best practice?
- In the parts studio: Add "mate connectors" and transform the imported (Step) model to the desired location and design the tooling?
- In Assembly: Import the (Step) file and locate the model in the desired location and design the tooling in context?
- In part studio: Use a derived part method, it uses more resources?
Best Regards,
0
Best Answer
-
owen_sparks Member, Developers Posts: 2,660 PRO
Hi @joep
I tend to use your Option 1.
Assemblies are good but depending on the complexity of your design, you may not even need one. (I'll only go there if I need to see motion, or have many instances of the same part that don't want many copies of in a part studio.) In most cases modelling all the discrete parts together in one partstudio is a good way to go.
The contexts are great to model around things that move (say both end stops on something that slides) but may be overkill here.
Long chains of derives are bad, one or two are fine, especially from "common parts" library documents.
Shout if that doesn't make any sense!
Cheers, Owen SBusiness Systems and Configuration Controller
HWM-Water Ltd6
Answers
I tend to use your Option 1.
Assemblies are good but depending on the complexity of your design, you may not even need one. (I'll only go there if I need to see motion, or have many instances of the same part that don't want many copies of in a part studio.) In most cases modelling all the discrete parts together in one partstudio is a good way to go.
The contexts are great to model around things that move (say both end stops on something that slides) but may be overkill here.
Long chains of derives are bad, one or two are fine, especially from "common parts" library documents.
Shout if that doesn't make any sense!
Cheers, Owen S
HWM-Water Ltd
However, much of the time we continue to need what was discussed in this thread (something like 'update standard views' in SW - https://forum.onshape.com/discussion/comment/23819#Comment_23819
O.S.
HWM-Water Ltd