Welcome to the Onshape forum! Ask questions and join in the discussions about everything Onshape.
First time visiting? Here are some places to start:- Looking for a certain topic? Check out the categories filter or use Search (upper right).
- Need support? Ask a question to our Community Support category.
- Please submit support tickets for bugs but you can request improvements in the Product Feedback category.
- Be respectful, on topic and if you see a problem, Flag it.
If you would like to contact our Community Manager personally, feel free to send a private message or an email.
Modeling Finish Stock (Cutting prior to machining)
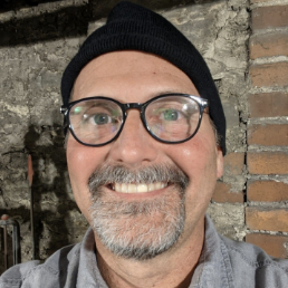
We cut a lot of parts from plate that get turned in a lathe or otherwise machined. Is there an easy way create in a model, and on the subsequent drawing, the finish stock required? We pull parts studio parts directly from OnShape directly in to our nesting software so I need a modeled part I can nest. Take a look at the shared file, it's a couple simple flanges. I've modeled the (2) flanges. Then I modeled a third part to represent my burn-outs as shown on sheet2 of the drawing. My visual preference on the drawing is a phantom line representing the burn-out or material to be removed but of course still need something I can pull into Sigmanest. What I'm doing works but seems cumbersome. I wondering if there's an easier way.
https://cad.onshape.com/documents/8f3480dc07fd47ed307aef0c/w/2cb077e97aa3d803a522b57d/e/7a969ca11d8162f85138e469
Thanks in advance for any thoughts/advise,
Kent
https://cad.onshape.com/documents/8f3480dc07fd47ed307aef0c/w/2cb077e97aa3d803a522b57d/e/7a969ca11d8162f85138e469
Thanks in advance for any thoughts/advise,
Kent
0
Best Answer
-
John_P_Desilets Onshape Employees, csevp Posts: 258
^^ I agree with @mahir Using a configuration for the stock size would be helpful. I made a quick example to show you. Below is the link .
https://cad.onshape.com/documents/9f730b0cdb8b51ca71fd5b75/w/ae7789b3d0dbcd0e86990370/e/459ae6562bf470a4ef8b7d3c
5
Answers
https://cad.onshape.com/documents/9f730b0cdb8b51ca71fd5b75/w/ae7789b3d0dbcd0e86990370/e/459ae6562bf470a4ef8b7d3c
https://cad.onshape.com/documents/72e167d4f62ee42caae9fafd/w/4bac3a02de6537f931d939c6/e/91d5d8f7e3c795c06f3914ba
1. Derive finished machined part into another Part Studio
2. Add material to the part in reverse machining order (i.e. last machined face should be first material add operation)
3. Repeat until full blank achieved
4. Use configurations to suppress each of those features in order
5. Create a drawing showing each machining operation if you so desire!
@ilya_baran's method sound a little less hokey.
It isn't a big deal though. I think it only comes up when using different profiles to generate the base feature of a part. I don't think that's a common occurrence. You can easily overbuild the part and then cut away what you don't want instead.