Welcome to the Onshape forum! Ask questions and join in the discussions about everything Onshape.
First time visiting? Here are some places to start:- Looking for a certain topic? Check out the categories filter or use Search (upper right).
- Need support? Ask a question to our Community Support category.
- Please submit support tickets for bugs but you can request improvements in the Product Feedback category.
- Be respectful, on topic and if you see a problem, Flag it.
If you would like to contact our Community Manager personally, feel free to send a private message or an email.
Missing bits I need to do work...
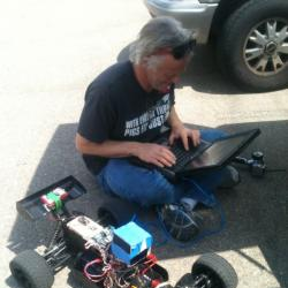
I need some way to import mating surfaces and/or computationally defined profiles.
The ability to place a
2D DXF file,
a CSV list of x,y
or manually entered points into a sketch plane would be awesome and get me 99% of the way there!
I need mass properties, IE
How much does it(part, assembly) weigh,
What are the parts moments of inertia.
What are the assemblies moment of inertia.
So the ability to give individual part components characteristics, like material, density would be nice.
Of course Drawings would be nice ;-)
The ability to place a
2D DXF file,
a CSV list of x,y
or manually entered points into a sketch plane would be awesome and get me 99% of the way there!
I need mass properties, IE
How much does it(part, assembly) weigh,
What are the parts moments of inertia.
What are the assemblies moment of inertia.
So the ability to give individual part components characteristics, like material, density would be nice.
Of course Drawings would be nice ;-)
Tagged:
3
Comments
If you select the part from the parts list or the part from the assembly tree, there is a mass properties icon located in the bottom right. This brings up the mass properties dialog. Is there any other information (besides material properties) that you need listed there?
Note that people will be trying to automate collection of this data for various purposes (mechanism simulation, required build material, buoyancy estimates, etc) and I think that people rarely are using this information while designing.
Onshape's time would be better spent, in my opinion, if you put a mass properties report generator in the hamburger menu that generates a report for all parts and assemblies in a human+machine readable format; YAML, JSON, CSV, pick your poison.
In other words in don't like information expressed with too much accuracy: Volume = 2,322518380E7 mm³ Mass = 2,383716771E1 kg
Even though I use mm in design, I would like to see volume in 0,023m³ and weight 23,8kg.
I would also like to see dimensions and volume of the box where model (assembly or part studio) fits for transportation purposes.
Drawings should have a preset 'parameter' fields for automatically displaying material volume, transportation volume and weight.
Another thing is when I need to create real world component which has multiple materials, it's not always convenient to model with too much accuracy. In these cases I would like to overwrite material properties with simply writing the known weight (to be used when calculating weight for assembly where component is used) instead of trying to find the right densities to achieve correct information.
I'm sure it is possible to have custom display with different unit and accuracy for the actual accurate value.
I think I understand your point about multiple material assemblies: are you saying "In cases where it is not important (or not possible) to me to define the individual densities (and hence masses) of all the parts of an assembly, please let me specify (for the purposes of drawings and Bills of Material) the mass of the assembly, as an override"
To me this implies that the piece parts would need to be able to have a density (and hence a mass) of "Undefined", in order to keep the internal database sweet. It seems like a good idea to consider this future enhancement from an early stage, because it's the sort of capability which it could be disruptive to retrofit if the pathways had not been prepared.
Others seem to be asking for a bidirectional input interface, allowing the user to input EITHER density or mass in respect of piece parts. I can see it would appear to offer a worthwhile saving of labour, when modelling an existing part whose mass was known but some of whose dimensions were not, AND whose density was not known. The ability to specify mass in this case would save a bit of juggling of figures, as the user tried to choose the best approximation to the truth.
If one or other of density or dimensions is known, then the user can very easily calculate a target volume in the first instance, or have the software calculate the actual volume in the second. The latter is not at all easy for a human to do, and the fact that the software does it in real time is priceless, and (to me) the sort of labour saving which should always receive maximum priority. Provided the mass properties data can easily be copied to the clipboard, it's a trivial calculation to arrive at mass, volume or density when two of the three are known, and the complication to the code of saving this negligible human labour seems questionable, to me.
It inevitably implies a complication to the user interface, also, because it means providing two different modes of operation, one in which density is fixed and mass varies when dimensions change, and the other in which mass is fixed and the density varies when dimensions change.
I'm entirely in favour of the software calculating the mass given the density, but the reverse calculation seems to me likely to be relatively rare. In your practice, how often would you need to do the reverse more than once for a given model?
Each off the shelf component needs the mass entered, often more than once. For me it's pretty common to start with a basic volume (a box or simplified shape) for a component and then refine it to be more accurate later in the design once I'm sure I'm going to use it and then sometime refine it further if someone wants more visual accuracy.
For things like screws, washers, pins; the material is homogeneous and the model accurate enough that density works (if you know the density of the material). Bearings (I rarely model balls, seals) are questionable, one can argue that the error introduced is negligible. Electronics, OTS gearboxes, motors, wires and other goodies all need the mass entered, often more than once as noted above.
Unfortunately different projects rarely share the same components because they are for different customers with different needs.
It's enough that it's a pain point for me, keeping in mind that there are 101 features Onshape needs that have higher priority for me than this.
So, for that situation, would a "mass override" capability suit your needs, in other words
<<forget the density, the mass remains what I say it is, regardless of volume, until I cancel the override or edit the mass>>
The thing I like about this is that the same approach would work for multibody parts (where the density may vary in different bodies) and also in assemblies (as noted above) without introducing ripples of complication.
Hmmm - the trouble there is that the inertia matrix would require the individual densities to be supplied, for multibody parts or assemblies....
Anyway, hopefully they fix a lot of other things before they work on this....
I would like to use Onshape also to design the boxes and how disassembled product will be packed in. At some point I hope I can create animation where parts come out of the box and show how things are assembled.
Transportation cost is not marginal these days, I think this is something that should be kept in mind when designing any product.
I think forum is a good place to throw ideas for the future, all the important / urgent stuff should go in using feedback..