Welcome to the Onshape forum! Ask questions and join in the discussions about everything Onshape.
First time visiting? Here are some places to start:- Looking for a certain topic? Check out the categories filter or use Search (upper right).
- Need support? Ask a question to our Community Support category.
- Please submit support tickets for bugs but you can request improvements in the Product Feedback category.
- Be respectful, on topic and if you see a problem, Flag it.
If you would like to contact our Community Manager personally, feel free to send a private message or an email.
Assembly mate problem
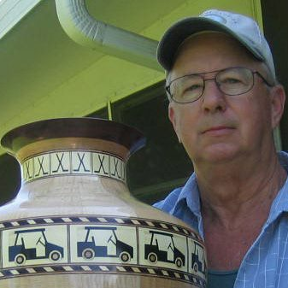
How do I mate these 2 subassemblies I have the one edge connected in the correct position. I can not seem to get it to connect face to face and in the proper orientation. In Inventor I would select the 2 faces to mate then mate the two approiate edges. Really stuck on this one.
https://cad.onshape.com/documents/8d9f5c0e2c4a57afce0fba09/w/997f4032f21955ab97fa26ee/e/778fe0068d005924d2415ed7
https://cad.onshape.com/documents/8d9f5c0e2c4a57afce0fba09/w/997f4032f21955ab97fa26ee/e/778fe0068d005924d2415ed7
0
Answers
Twitter: @onshapetricks & @babart1977
For the benefit of those new to Onshape the answer is you cannot. Assembly mates (orientation constraints) can only be made between instances of parts; not instances of other (sub) assemblies.
Here is some additional information which might be helpful to new Onshape users....
It has been my observation that experienced Onshape users use the term "Mate" when referring to the "Fastened Mate" constraint method which causes some confusion to new users. In Onshape speak "Mate" technically means "Assembly Constraint".
The "Fastened Mate" constraint method is by far the most common constaining method used and depends on exclusively on "Mate Connectors". Mate Connectors can either be explicitly created in the Assembly context and "attached" to geometry in the assembly, explicitly created in a Part Studio context and "associated" to a part, or can be implicitly sensed from instanced part geometry (surfaces/included sketches).
Note: There is a subtle difference between a Mate Connector "attached" to assembly geometry and one "associated" to a part. Assembly mate connectors always move with the instance of part geometry to which it was attached. A Mate Connector created in a Part Studio moves with the feature geometry it was attached to, but if a Transform feature is used to orient/duplicate the part any "associated" Mate Connector is NOT included by default in the transform; they have to be manually added to the entities to transform selection list. I have been told this behavior is a valuable feature in the product.
Sometimes the Group may be called Group Mate, I am probably guilty of this but technically it's not a mate.
Twitter: @onshapetricks & @babart1977
Fully Mated with just THREE top level mates!
I just finished watching Philip Thomas' recorded 7/10/18 Webinar: Onshape Assemblies for SolidWorks Users. At approximately 34:50 and 41:20 into the recording Philip uses the term "mate" for "Fastened mate". Given a person's tendency to drop words from their speech and that "Fastened Mate" is by far the most common mate used, when the term "mate" is used without a pre qualifier word it usually means "Fastened Mate". That was the point I was trying to convey to a new user reading the post.
Whatever function is used to control the orientation of part instances one to another is a Mate function, therefore, I consider "Group" to be a mate function. Technically it should be (re)named "Group Mate".
My original comment was not intended to be instructional but to clarify the misconception surrounding mating subassemblies.
The other information (subtleties of Mate Connectors created in a Part Studio vs an Assembly) was something that I recently struggled with which I thought a new user should be aware of.
@philip_thomas
I think you might have me confused with another "StephenG". I do not remember any post where I said, " 'you cannot' mate those parts".
P.S. I took a quick peek at the assembly mate scheme used in the Streptohedron. Hard to get excited when "Group Mates" are used.
On a positive note, just to prove that my comments are not always negative.... Onshape's assembly constraint tools are heads and shoulder above anything that I have ever used. Onshape's assembly mates are in easy to create, edit and more importantly, extremely robust.
With regards to my perception that you (as opposed to another StephenG), did not believe that that assembly could be mated, i may have inferred that from your earlier comment (highlighted below)
My apologies if i misinterpreted your statement.
The completed assembly uses three 'Fasten Mates' at the top level and specifically relies on the method demonstrated in the webinar whereby the secondary axis of a pair of Mate Connectors are redefined to align with part edges
I hope this helps.