Welcome to the Onshape forum! Ask questions and join in the discussions about everything Onshape.
First time visiting? Here are some places to start:- Looking for a certain topic? Check out the categories filter or use Search (upper right).
- Need support? Ask a question to our Community Support category.
- Please submit support tickets for bugs but you can request improvements in the Product Feedback category.
- Be respectful, on topic and if you see a problem, Flag it.
If you would like to contact our Community Manager personally, feel free to send a private message or an email.
Beams not quite as it should be?

Earlier this year I tried out the beams feature and it worked fine, tonight I tried it again on a real project but the "butt joints" feature does not seem to be working. I reduced the complexity to just two beams and nothing I did would make it work correctly. It seems to do a wierd coped joint, and it is not just a rendering problem because it carries through to the drawing of the cropped beam part. I have included a screen grab so maybe someone else has an idea of what is happening. BTW I am using Firefox, but it does the same in Chrome
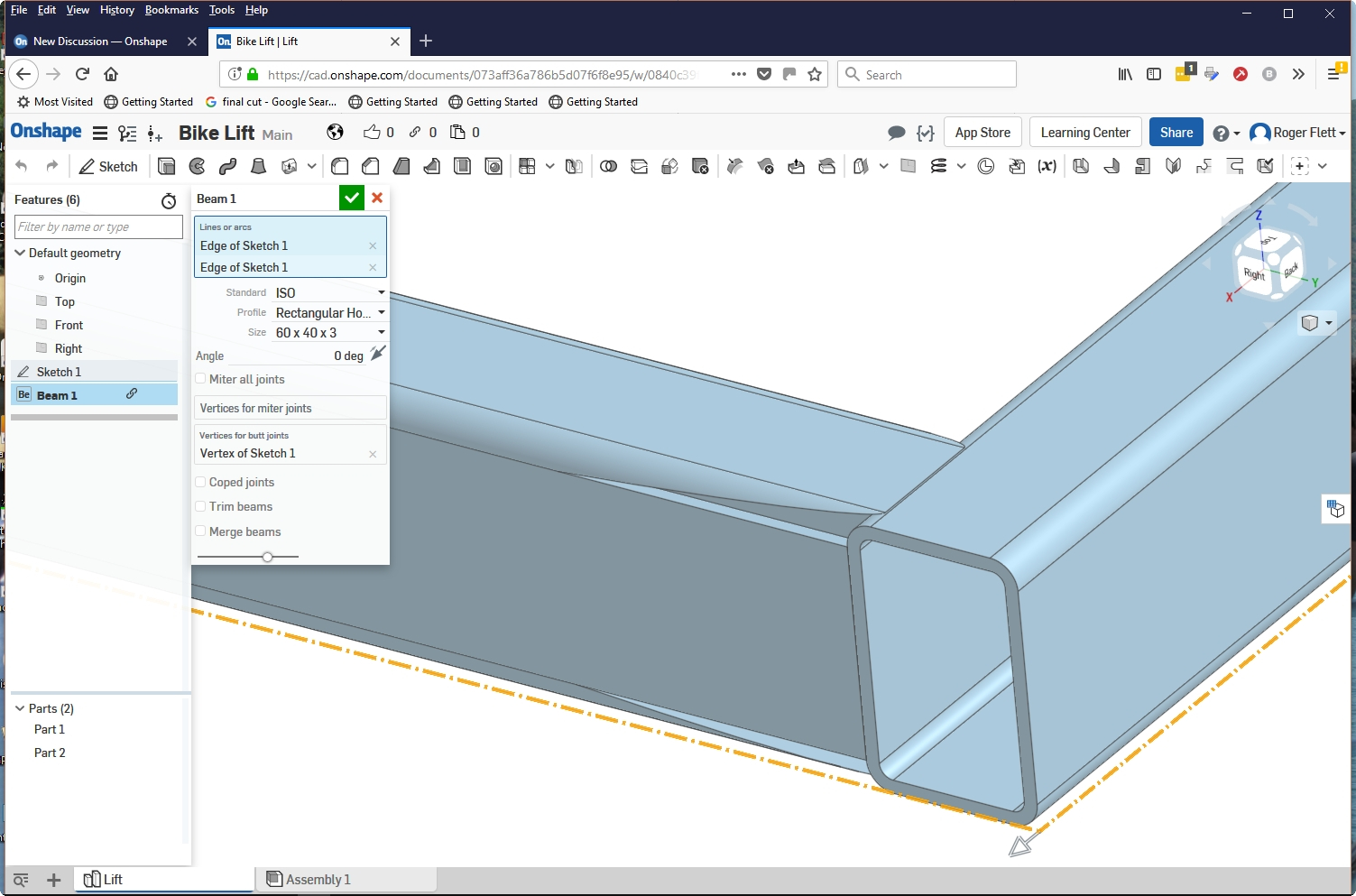
0
Comments
In the meantime you can either a) use the "coped joint" option and manually do a "replace face" to remove the coping afterwards (which is what the beams feature is doing internally anyway, or at least trying to) or b) create the beams in two separate beam features then use the "trim beams" option and "planar faces to trim to"
Sorry for the inconvenience.
Sorry error should read .02mm too short
I believe the 0.02mm offset is done to ensure the trimming works without geometric issues from trimming one beam with the other in complex cases. If you want a beam whose butt joints trim flat, rather than trimming flush to the contour, you can use a custom profile with "Enable coping" unchecked. This will skip the offset and perform a simpler trimming operation.
I will defer to Neil to say if there is a better solution for coped or non-custom profiles.