Welcome to the Onshape forum! Ask questions and join in the discussions about everything Onshape.
First time visiting? Here are some places to start:- Looking for a certain topic? Check out the categories filter or use Search (upper right).
- Need support? Ask a question to our Community Support category.
- Please submit support tickets for bugs but you can request improvements in the Product Feedback category.
- Be respectful, on topic and if you see a problem, Flag it.
If you would like to contact our Community Manager personally, feel free to send a private message or an email.
Clearance for mating threads
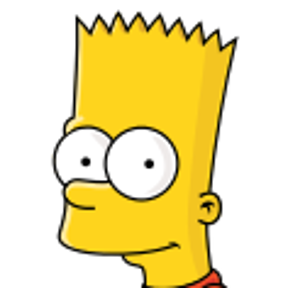
Hi everyone, I'm new to Onshape & this is my first post.
I feel a bit silly asking such a simple question but I've had several failed attempts so I thought I'd ask the pros.
I'm trying to model some mating threads (metric) for 3D printing and they all seem to look good in the drawing but the clearances are too tight and the nut never fits the male thread when I print them.
I've tried modeling the male thread and then creating the female part by doing a boolean subtract on the female mating part. Setting a bigger offset on the boolean subtract seems to destroy the thread form and I can't seem to set an offset bigger than 0.4mm with the thread I'm trying to offset.
I've also completely modeled the female part from scratch (allowing clearance on the root diameter of the male thread) and swept a thread with the same thread form and it still didn't fit after it was printed. I'm sure I could tinker with my clearances and get it to work without too much trouble this way but I didn't pursue that as it seemed like a lot of extra work.
Here's one I tried yesterday by doing a boolean subtract from the male part. I used a 0.25mm offset when I did the boolean subtract and the nut won't even go close to screwing on. My thread forms aren't on spec, I'm just using rudimentary thread forms until I can get my clearances/fit worked out.
I'm not up to assemblies in the learning path yet, no doubt I'll be more enlightened by the time I get through that but I need some threaded parts now.
I'm obviously doing something wrong, if anyone can point me in the right direction I'd really appreciate it.
Edit: I just found the thread creator. I'll run some tests with that, it looks like it's just what I needed.
Edit 2 : I just drew another model using the thread creator tool (that was much easier than modeling a thread) and after printing it wouldn't screw together either. I made both the parts a nominal 30mm diameter, applied the threads to both parts and then did a boolean subtract with 0.2mm offset between the parts. So I will need either a larger offset value or draw one part with the appropriate clearance added or subtracted from the nominal diameter before applying the thread.
I know this is all really simple stuff but maybe my mistakes will help someone else some time in the future if this comes up in a web search.
Tagged:
0
Best Answers
-
owen_sparks Member, Developers Posts: 2,660 PRO
Hi and welcome to the forum.Firstly nice model3D printing threads is not easy!A couple of thoughts in no particular order.(a) If you're using a regular filament printer then metric threads are going to be tough. They're designed to be really precise.(b) When we print them (on average at a 0.2mm layer height) then we're already making an approximation of the thread. ie for this 0.2mm space insert filament here yes or no? So a 0.2 mm offset is doomed(c) It'll then be a bit out due to printer calibration.(d) It'll then be a bit further out as the part warps due to cooling.(e) Usual practice is to print slightly oversize and then run a tap or die over them to clean up the threads, but who happens to have an M30 tap and die set lying about?So unless you need your parts to mate to existing real M30 threads I'd say ditch that thread profile and use something that has a wider pitched sloppier fitting profile. The very sharp tips of threads offer very little in the way of extra strength but require precision to make, so I'd suggest something more rounded. Take a look at a plastic coke bottle lid thread for inspiration, and bear in mind that that will be made with more precision than we can manage.Hope that helps,Owen S.Business Systems and Configuration Controller
HWM-Water Ltd1 -
mahir Member, Developers Posts: 1,316 ✭✭✭✭✭
Definitely start with known thread forms. They've been around forever, and there's no reason to reinvent the wheel. Here's a quick guide a la Google for the minor (innermost) dia of a metric female thread and the major (outermost) dia of the matching male thread.
Without getting too into details, the first thing I noticed when looking at your last link (under Edit2) was that on your female thread has very sharp crests on the minor dia. To avoid interference, make sure the peaks are cropped and the valleys have a minimal radius. This applies to both male and female thread. See my redline below.
Also, don't forget that your 3D printer has some tolerance. To insure clearance, add that tolerance to either your male or female part, or split the difference and add half to each. The .010in (.25mm) you were using seems about right if you have budget 3D printer.2
Answers
HWM-Water Ltd
Without getting too into details, the first thing I noticed when looking at your last link (under Edit2) was that on your female thread has very sharp crests on the minor dia. To avoid interference, make sure the peaks are cropped and the valleys have a minimal radius. This applies to both male and female thread. See my redline below.
Also, don't forget that your 3D printer has some tolerance. To insure clearance, add that tolerance to either your male or female part, or split the difference and add half to each. The .010in (.25mm) you were using seems about right if you have budget 3D printer.
I think a big problem is that Thread Creator does not cut a thread into a hole, but adds it to the hole. At first I wouldn't believe that...
So it's quite hard to find the matching size of a hole to "add" (instead cutting) a thread to, which will represent the right measures after printing. I made me some templates to test cylinder diameters for screws and boreholes to maintain compatibility to ISO metric system. The best dimessions varies even with every uses nozzle diamater with CURA / Ultimaker.
Sorry, didnt't find a (discussion!) thread concerning features for the Thread Creator tool to dicuss this further.