Welcome to the Onshape forum! Ask questions and join in the discussions about everything Onshape.
First time visiting? Here are some places to start:- Looking for a certain topic? Check out the categories filter or use Search (upper right).
- Need support? Ask a question to our Community Support category.
- Please submit support tickets for bugs but you can request improvements in the Product Feedback category.
- Be respectful, on topic and if you see a problem, Flag it.
If you would like to contact our Community Manager personally, feel free to send a private message or an email.
Getting assembly studio information back into part studio?

I've used assembly studio to line up parts from two different part studios.
Now that I have their alignment I need to get that alignment info ... points or something ... back into part studio so I can design the mating hardware.
I don't immediately see how to do that.
Any suggestions?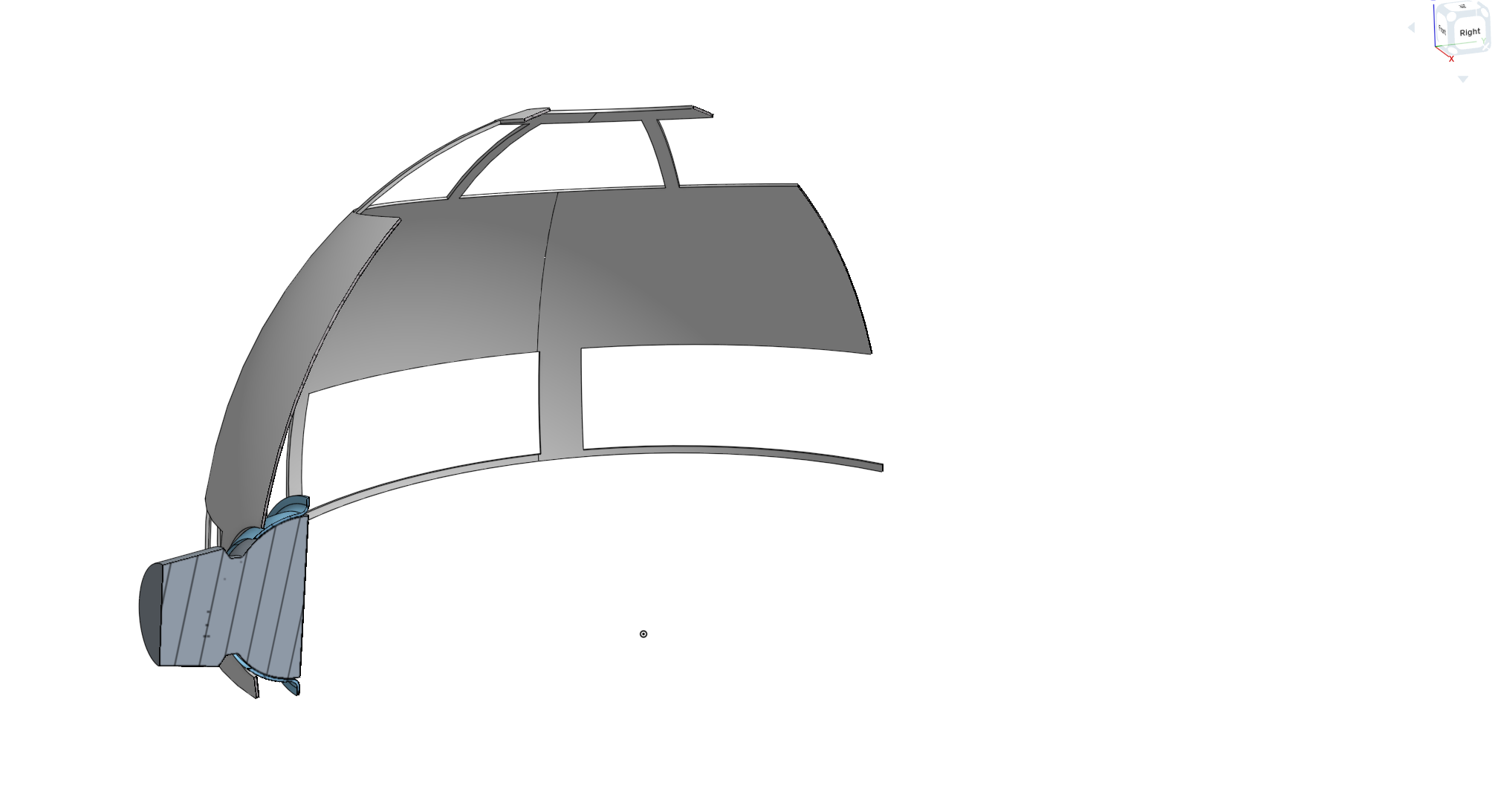
Now that I have their alignment I need to get that alignment info ... points or something ... back into part studio so I can design the mating hardware.
I don't immediately see how to do that.
Any suggestions?
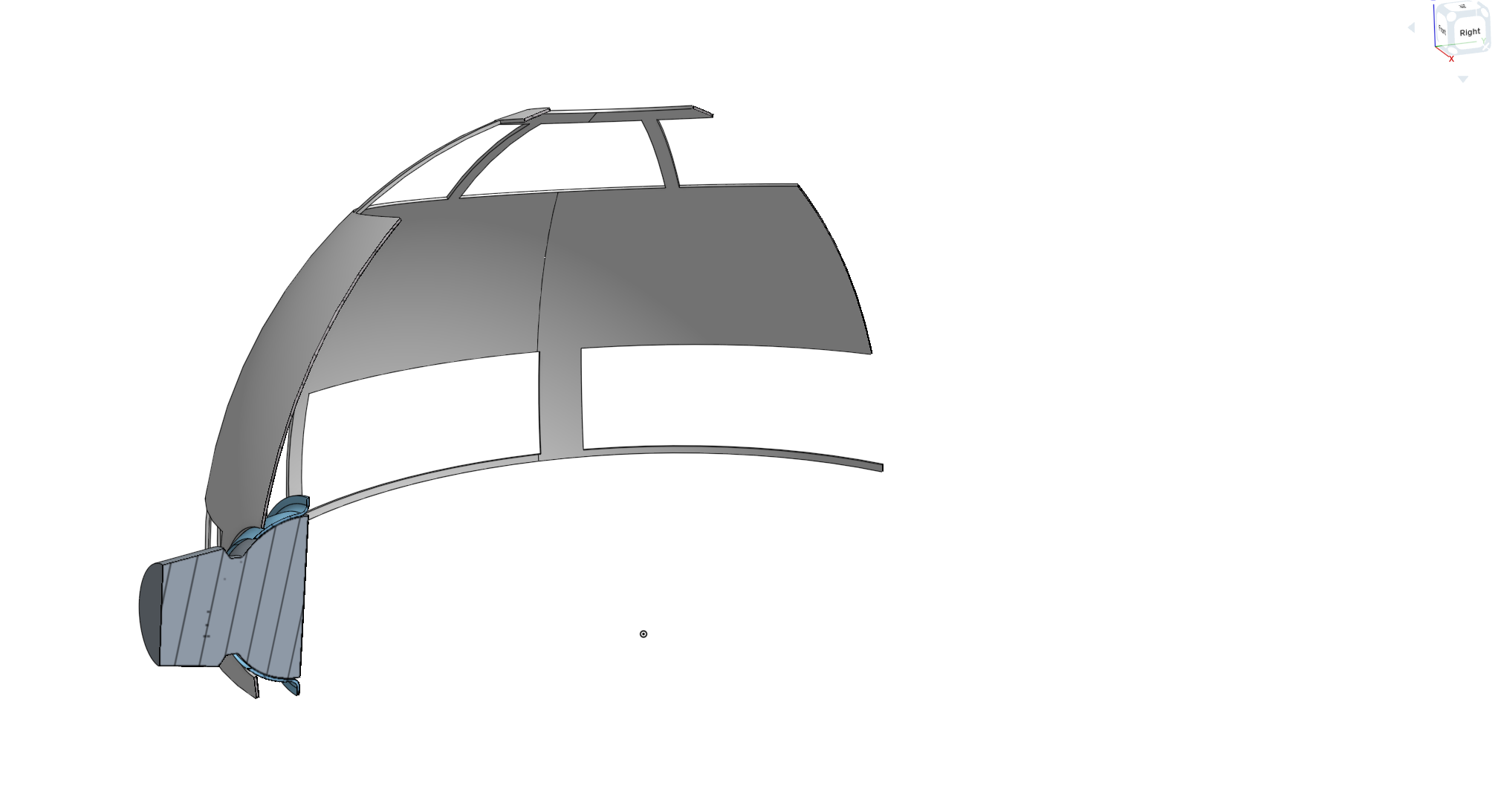
0
Answers
Onshape, Inc.
I know I've kept you busy with all the STL questions but now that I have the STLs imported and positioned, I am now back to working on the actual design.
Any suggestions for capturing points of interest while moving the kinematics through its range of motion? Then using those to optimize the original mechanism geometry?
Robert
I also think using Mate Connectors (which are just coordinate systems, really) and transform features would work well, but it depends on complex the motion is. Is it possible for you to share the geometry with us?
Linked[in]
Onshape, Inc.