Welcome to the Onshape forum! Ask questions and join in the discussions about everything Onshape.
First time visiting? Here are some places to start:- Looking for a certain topic? Check out the categories filter or use Search (upper right).
- Need support? Ask a question to our Community Support category.
- Please submit support tickets for bugs but you can request improvements in the Product Feedback category.
- Be respectful, on topic and if you see a problem, Flag it.
If you would like to contact our Community Manager personally, feel free to send a private message or an email.
Variable Helix
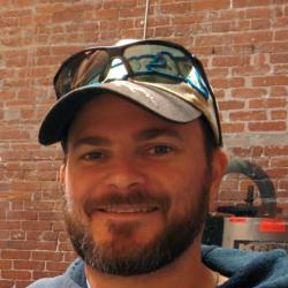
Any plans for the ability to have a variable helix where pitch and diameter can be controlled independently? (Like the SW tool)
Barring that, any ideas on how to accurately model the thread form for self tapping screws tapering off into the gimlet point?
Barring that, any ideas on how to accurately model the thread form for self tapping screws tapering off into the gimlet point?
Tagged:
0
Best Answers
-
pete_yodis OS Professional, Mentor Posts: 666 ✭✭✭
@shaun_3 There is no compound curve function in Onshape at the moment. To get around that, you have to create edges of either surfaces or solids and reference them in your sweep to get what you want...
5 -
andrew_troup Member, Mentor Posts: 1,585 ✭✭✭✭✭
shaun_3 said:Possible to use intersection between a revolved surface - representing the body of the screw - and a swept helical surface as the path for a new swept solid?
(variable helix, AFAIK, is still confined to varying the pitch at constant diameter; it was not possible last time I checked to combine a tapered helix with a variable pitch. Plus a tapered helix did not support a transition from parallel to tapered, so it would not be a realistic representation of most self tapping screws. However I'm a couple of years behind the play in SW, so please correct me if wrong)5
Answers
(variable helix, AFAIK, is still confined to varying the pitch at constant diameter; it was not possible last time I checked to combine a tapered helix with a variable pitch. Plus a tapered helix did not support a transition from parallel to tapered, so it would not be a realistic representation of most self tapping screws. However I'm a couple of years behind the play in SW, so please correct me if wrong)
This kind of control allows you to sweep a thread form such that it disappears into the point.
EDIT : using turns instead of pitch in the helix command performs a smooth transition
EDIT 2 : There is no actual smooth transition when using the number of turns instead of pitch either, it was just an optical effect and I got lucky with the number of turns i selected randomly, when using a different # of turns I get the same result as in the second image above. Is very likely we need tools like andrew_troup said:
Indaer -- Aircraft Lifecycle Solutions
Is it possible to specify transition radii when the diameter changes (ie, the radius of the tangent arcs, if using a revolved surface intersecting a helical surface, per your alternative method?)
@nav: I don't right now have an idea for a workaround for the problem of how to transition smoothly between different pitches. It's a bit difficult, in the absence of 3D sketches with fillet or tangent spline or 'fitted spline' ability
For variable diameter, though, it seems relatively straightforward. I would tend to use a revolve to create the surface, rather than a loft, because it's dead easy to use fillet to create the necessary tangent arcs in the profile, but I think there are other ways which would also work.