Welcome to the Onshape forum! Ask questions and join in the discussions about everything Onshape.
First time visiting? Here are some places to start:- Looking for a certain topic? Check out the categories filter or use Search (upper right).
- Need support? Ask a question to our Community Support category.
- Please submit support tickets for bugs but you can request improvements in the Product Feedback category.
- Be respectful, on topic and if you see a problem, Flag it.
If you would like to contact our Community Manager personally, feel free to send a private message or an email.
Best Of
Define the surface distance between two bending pockets
Of course I could build the sheet metal model differently from the beginning, but I already have some features planned in this part and no time to do it again. It would be ideal to be able to say afterwards what the distance between the two faces should be, so that the flange length calculates itself for angles above and below 90°.
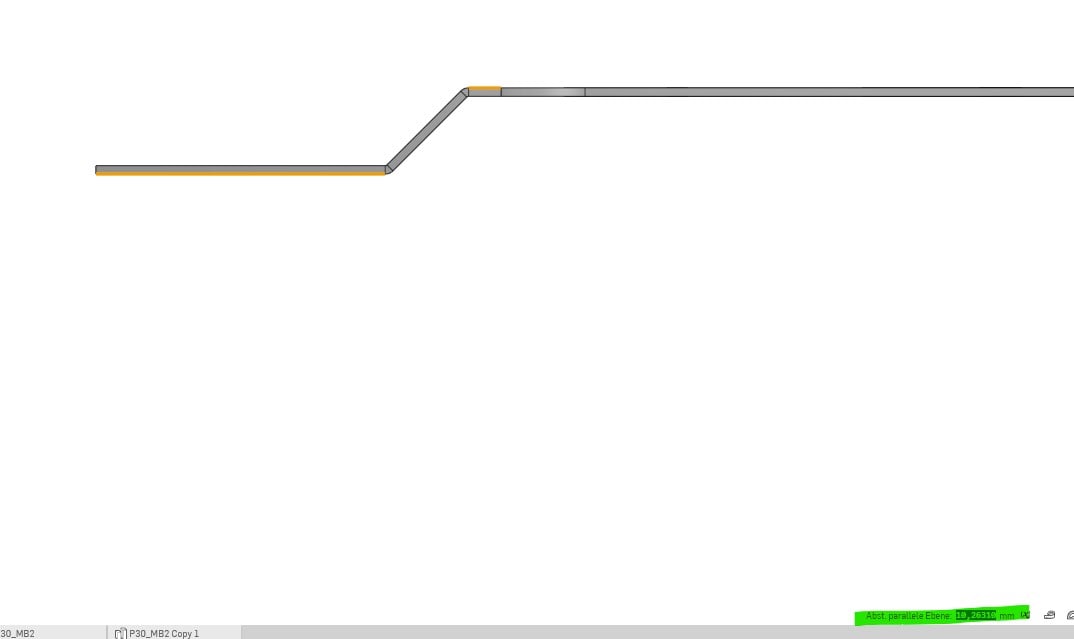
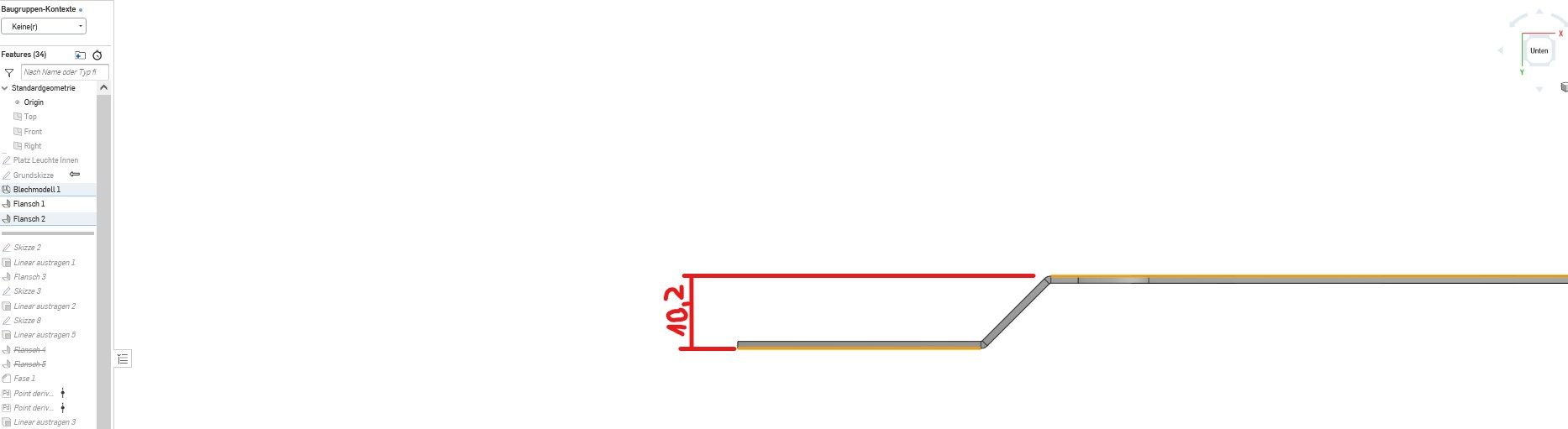
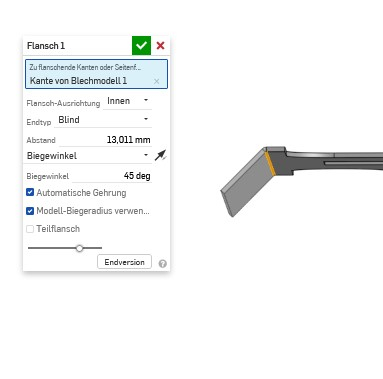
Re: Define the surface distance between two bending pockets
glen_dewsbury said:use a material offset for you sketch with extrude sheet meta.
https://cad.onshape.com/documents/fd8d60e9de614fef424c4257/w/f74808f6a3a75c2ab5c832d6/e/ca3ea29c67e222cf9d89f47a
Re: Error: "Should be unreachable!"
@MBartlett21 Yes it worked with the newer Version V0.4.1 Thank you!
Re: Error: "Should be unreachable!"
We are currently using V0.4.1 . I will check the new version. Thank you!
Re: Error: "Should be unreachable!"
It looks like you are using an older version, possible not from the original document. That error message is now a warning that you haven't selected a sheet metal part.
This could be to do with 'recent' changes to how Onshape's sheet metal works internally (i.e. the new corner break stuff, holes, etc.).
Re: Error: "Should be unreachable!"
Link for reference:
Re: ThreadLab - Internal/External Modeled/Cosmetic Threads with External Thread Callouts
I'd think if you were going to model the threads you could go with the drilled option instead of the tap drill.
This is just one more reason they need to fold it in. One checkbox for "modeled" in the tapped hold dialogue would let you dispense with all the complexity.
Re: Why can't I rotate the dogbone link component (see image)?
If the whole assembly moves with it means the rest of the assembly isn't constrained…
Try fixing the part it's mated to, that should take care of it…