Welcome to the Onshape forum! Ask questions and join in the discussions about everything Onshape.
First time visiting? Here are some places to start:- Looking for a certain topic? Check out the categories filter or use Search (upper right).
- Need support? Ask a question to our Community Support category.
- Please submit support tickets for bugs but you can request improvements in the Product Feedback category.
- Be respectful, on topic and if you see a problem, Flag it.
If you would like to contact our Community Manager personally, feel free to send a private message or an email.
Best practice, ball bearing model from import
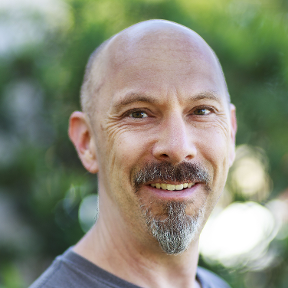
I have a project that will require the use of shielded ball bearings. I downloaded a model from the vendor website (I used solidworks format). The model is imported into a part studio as individual components that make up the bearing.
I would like to have only a single instance of the bearing, and assign the part number from the vendor so I can insert it into an assembly and have only one reference to the part as a whole in the BOM.
I thought I could just boolean all the parts together, and then assign the part number to the result. Well, the parts don't intersect so the boolean operation does not work. I know I could group them in an assembly, but then there is no way to assign a part number to the group?
https://cad.onshape.com/documents/6a747034d48ef1346ad1bc1f/w/f3e1f23f6352b61fc6862fb3/e/eb98a4cc6162a6a9b1291cf2
I would like to have only a single instance of the bearing, and assign the part number from the vendor so I can insert it into an assembly and have only one reference to the part as a whole in the BOM.
I thought I could just boolean all the parts together, and then assign the part number to the result. Well, the parts don't intersect so the boolean operation does not work. I know I could group them in an assembly, but then there is no way to assign a part number to the group?
https://cad.onshape.com/documents/6a747034d48ef1346ad1bc1f/w/f3e1f23f6352b61fc6862fb3/e/eb98a4cc6162a6a9b1291cf2
Tagged:
0
Best Answer
-
michael_mcclain Member Posts: 198 PRO
I usually delete the internals of bearings and move some faces until they intersect and I can Boolean-Union the piece together. If the weight is on the manufacturer's page then I add that into the properties of the Final part to document it.
If you just directly add all the parts to an assembly and group them together then that works great too. With the group method you can assign proper material and get a pretty accurate weight in the assembly, but I will add manufacturer listed weight as metadata anyways. Either way, I get rotation movement in other assemblies, not the bearing itself.
Just make sure to double check imported parts and direct-edit them straight away BEFORE they get used. I've made that mistake enough to learn that extra edit time is always worth it.7
Answers
I created an assembly of the bearing, and made a suitable group. I then assigned a part number to the assembly using the tab. Then using a structured BOM the part number shows up correctly and does not break down the assembly into all its parts.
Still wondering is there a better way to do this?
Owen S
HWM-Water Ltd
If you just directly add all the parts to an assembly and group them together then that works great too. With the group method you can assign proper material and get a pretty accurate weight in the assembly, but I will add manufacturer listed weight as metadata anyways. Either way, I get rotation movement in other assemblies, not the bearing itself.
Just make sure to double check imported parts and direct-edit them straight away BEFORE they get used. I've made that mistake enough to learn that extra edit time is always worth it.
@michael_mcclain that is a good idea about using the mfg. weight information.