Welcome to the Onshape forum! Ask questions and join in the discussions about everything Onshape.
First time visiting? Here are some places to start:- Looking for a certain topic? Check out the categories filter or use Search (upper right).
- Need support? Ask a question to our Community Support category.
- Please submit support tickets for bugs but you can request improvements in the Product Feedback category.
- Be respectful, on topic and if you see a problem, Flag it.
If you would like to contact our Community Manager personally, feel free to send a private message or an email.
Hole tool, design intent, best practices
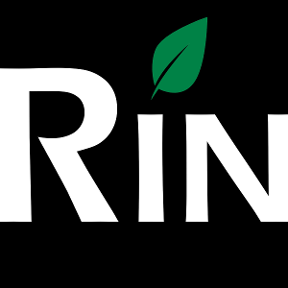
Consideration and thoughts about best practices on using hole tool.
Few angles to approach:
- Hole takes more time to regenerate than circle & extrude cutout
- Hole callout in drawings only finds the ones made by hole tool
- Single hole feature can include similar holes for multiple parts
- It is commonly thought as a good thing to have as few features as possible
- Good design intent is easy to edit and strong against breaking on edits
I haven't had problems with performance with my simple designs so I haven't really payed attention to regen times for holes. I've been trying to create all holes using hole tool and avoid circle extrude cuts for drilled holes because I like hole callouts more than adding depth dimensions to hidden lines. I wish there was a way to include x-y position into call-out in drawings.
I've found myself dividing holes to separate features since if I've already built the assembly and remove some redundant hole from feature, it will change also others id's and break the assy mates. So in the name of robustness I've been creating longer feature list and with decent naming it's pretty quick to edit similar holes even if it takes few more clicks and has possibility for error / forgetting one.
If those ID's would be static I would certainly combine all similar holes, it's amazing that you can even make configuration that adds/removes target points 

At this point I wen't back to check that this ID issue is still the case and took out an instance but it didn't affect to mates on other holes. Has this been improved? Have I been worried for something that happened only in past? Can someone please confirm @philip_thomas
What do you think? Do you use hole tool or circle extrude? Any other thoughts / tips making the best out of hole tool?
//rami
Tagged:
0
Comments
Hole reference stability has not been improved yet. You were just lucky last time. Please file a support issue, it will help us to prioritize fix.
One possible optimization - use of face pattern for hole faces. It will propagate hole data to pattern instances and will regenerate faster then the same number of instances in hole feature.
I think it's happened in the past, but I just re-routed mate connector to new hole and didn't think much about it. Now that you've pointed it out. Maybe I shouldn't have to do this.
I think another down turn to not using hole feature/ cosmetic threads/ hole meta data, is machining the part. No current NC software reads the meta data now, but hopefully, the newer NC codes can access this meta data and produce a drill cycle. I guess I'd want to support this.
The hole feature has certain 'opportunities for improvement' - and trust me, I am being kind.
We know this and are planning an overhaul. Your (collective) support tickets help us get this done.
Do I have any magic solutions? No.
But I might stir your imagination and possibly even improve your productivity with a couple of 'ideas'
1) If you change hole types and don't want to lose mates, this may help;
- Import the sketch containing the points used to generate the holes into the assembly along with the part
- Apply a group mate between the sketch and the part before moving either
- Mate to the sketch points and not to the holes - the ID's will be the same regardless of the hole type
2) There is an experimental 'parametric hole' feature. This is an (unsupported) hole feature that takes ALL the points in a sketch and makes a hole at each one. If you add a line, you get two more holes. You get the idea. This is cool because it saves a lot of clicking. AND, because configurations can control the sketch being used to generate the holes, you can easily point to other sketches containing (potentially) differing numbers of points (holes).https://cad.onshape.com/documents/4c1aba613a40947311bc6d05/w/3a2a6e89b11af1ac81749f98/e/16f4dcf95b4d67030e3eaa4f
(Thank you Jake Rosenfeld for that one)
3) The above has a twin - "Parametric Sketch Driven Pattern" (written by yours truly) that will import geometry into a Part Studio and patterns it to every point in the sketch. This was written for a company wanting a quick way of inserting PEM nuts onto a sheet metal part. It works very well!
https://cad.onshape.com/documents/e02f8da5c872d4d55e30e218/w/41d8b64176967ea1955c14fa/e/aff7ca3a7b06f2e095750678
Have fun!