Welcome to the Onshape forum! Ask questions and join in the discussions about everything Onshape.
First time visiting? Here are some places to start:- Looking for a certain topic? Check out the categories filter or use Search (upper right).
- Need support? Ask a question to our Community Support category.
- Please submit support tickets for bugs but you can request improvements in the Product Feedback category.
- Be respectful, on topic and if you see a problem, Flag it.
If you would like to contact our Community Manager personally, feel free to send a private message or an email.
Mate connector for slider mate for tube roller on configurable diameter tube
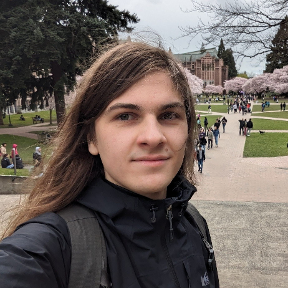
I've been scratching my head over this for a bit now, so I thought I'd ask about a particularly weird case for defining a mate connector. Here is the part I'm importing: https://www.servocity.com/0-250-acetyl-press-fit-tube-roller.
Here is an image of a similar part (with built-in ball bearings) as an example of how the part sits on tubing:

What I'd like to have would be a mate connector for a slider mate with the tube which the roller sits on where the mate connector's position is defined by a configuration variable for the tube's outer diameter. Here is a document in which I mock up part of the target behavior: https://cad.onshape.com/documents/6569ec2e7e44e8d68bc3e677.
A simple slider mate is probably good enough in this situation because the roller may slip, so modeling a relation between its rotation and translation along the tube wouldn't be mechanically meaningful (and would add complexity/difficulty). The current document's demo assembly is configured with a table with different mates for each of the diameters of tubing. However, the goal is to have just the roller and mate connector with a configuration variable for the tube diameter so that it can be "dropped in" and used with any diameter pipe (within the 1/4" to 2" limits of the part).
Sorry if this question is a bit wordy/unclear, and thank you in advance for any help!
Here is an image of a similar part (with built-in ball bearings) as an example of how the part sits on tubing:

What I'd like to have would be a mate connector for a slider mate with the tube which the roller sits on where the mate connector's position is defined by a configuration variable for the tube's outer diameter. Here is a document in which I mock up part of the target behavior: https://cad.onshape.com/documents/6569ec2e7e44e8d68bc3e677.
A simple slider mate is probably good enough in this situation because the roller may slip, so modeling a relation between its rotation and translation along the tube wouldn't be mechanically meaningful (and would add complexity/difficulty). The current document's demo assembly is configured with a table with different mates for each of the diameters of tubing. However, the goal is to have just the roller and mate connector with a configuration variable for the tube diameter so that it can be "dropped in" and used with any diameter pipe (within the 1/4" to 2" limits of the part).
Sorry if this question is a bit wordy/unclear, and thank you in advance for any help!
Get in touch: contact@alnis.dev | My personal site: https://alnis.dev
@alnis is my personal account. @alnis_ptc is my official PTC account.
@alnis is my personal account. @alnis_ptc is my official PTC account.
Tagged:
0
Best Answers
-
NeilCooke Moderator, Onshape Employees Posts: 5,891
Composite Curve will still consist of 3 segments, so a spline is the best approximation (I think it is accurate enough).Senior Director, Technical Services, EMEA5 -
kevin_o_toole_1 Onshape Employees, Developers, HDM Posts: 565
FeatureScript Unified Spline will take multiple lines and arcs, and create a single spline through all curves which you can use for e.g. sketch tangent constraints. This has all the benefits of @NeilCooke 's solution, without the need for approximation.
3
Answers
Then a simple slider is good.
You can configure your sketch to have different diameters and that's it.
This is a bit of a trickier situation because the profile of the roller is an arc, a line, and another arc, so a single circle cannot cover all diameter cases with a single tangent constraint as far as I know. As the diameter grows, it comes into contact with different geometry.
Sorry if I'm not articulating this well!
@alnis is my personal account. @alnis_ptc is my official PTC account.
https://cad.onshape.com/documents/585135a07a22a6cf2a538a57/w/84f2e412f5bce7f65d55a23d/e/1db576bed76718b866aa9189
I think that in the end, I'll try to create a one-off FeatureScript because it will provide an exact solution and it will be good practice. Alternatively, if that doesn't work out, I might just go with a clunkier configuration table (with ranges for the diameter to select the circle/mate connector) and configuration variable (with the exact diameter of the tube).
Thanks again!
@alnis is my personal account. @alnis_ptc is my official PTC account.
@alnis is my personal account. @alnis_ptc is my official PTC account.
The Onsherpa | Reach peak Onshape productivity
www.theonsherpa.com