Welcome to the Onshape forum! Ask questions and join in the discussions about everything Onshape.
First time visiting? Here are some places to start:- Looking for a certain topic? Check out the categories filter or use Search (upper right).
- Need support? Ask a question to our Community Support category.
- Please submit support tickets for bugs but you can request improvements in the Product Feedback category.
- Be respectful, on topic and if you see a problem, Flag it.
If you would like to contact our Community Manager personally, feel free to send a private message or an email.
What are your most used mass property items?
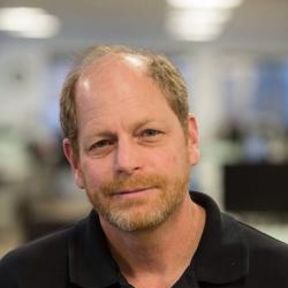
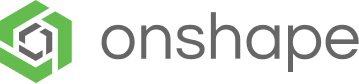
In the context great forum discussions, several people have mentioned using mass properties. Since mass properties is a category of calculations I am interested in the results that you use the most and what workflow suits you best with respect to volumes, mass points, axis of inertia, moments of inertia, etc.
Thanks,
/Scott
Thanks,
/Scott
Scott Harris / Onshape, Inc.
0
Comments
I mean like in this example:
*Take a pump housing (consisting of multiple parts/bodies, including a rotor).
*Shut off (planar cap) all intake/exhaust openings.
*Calculate volume of internal 'flow body' (internal volume, minus rotor, in this example).
I would really like a workflow that automates:
*Capping of intakes and exhausts.
*Boolean operations to generate flow body.
*Volume and mass calculation of flow body.
*Parametric relation: if model updates, then flow body and calculations update as well.
Dries
expanding on what I send you by email:
For me, the big 4 that I use most often for Mass Properties are:
Volume
weight
Surface area
CG
- In the normal coarse of my work I'm finding that I use surface area frequently for calculating size of PCBA's that EE's give me in sq. inch area.
- For Volume and Weight, I've been designing a 2-person submersible and you can imagine how I'm using MP to calculate negative Ballast and neutral buoyancy.
- I've also been designing charging docks for consumer products where we incorporate zinc die cast parts to weight the dock as well as calculate the amount of weight to overcome the pogo pin contact force.
- Recently designed a table top scanner for the TSA that has a 120.lbs magnet in it and I needed to insure that it did not tip over with a 15 degree angle of movement (CG.)
these are just a few examples that make having MP essential.
Mark
1. Weight of assemblies and parts ( for shipping, foundation sizes, shot weighttc)
2. volume and weight of fluid( in bathroom product design, packaging, medical etc)
3. Surface area of selected faces ( not mass but essential)
2. The Center of Mass locations for the entities being calculated. Along with this the moments of inertia
3. Surface area of surfaces selected
4. Section modulus of an area (useful for quick structural deflection calculations).
This is a separate thought, but it would be helpful if we could have a tool to create material definitions that can then be applied to parts. A material library. This would play into the calculation arena, but also would be very important for FEA downstream. It seems if the material library were thought out, it could be done in a way that is not a bolt on library, but one that is integral to Onshape and could have implications for helping users with BOMs - identifying what raw material a part is made from, possibly what part number that raw material is. This would be important on the PLM/ERP facing side of things. If Onshape is going to support BOMs and if it is a database system, then why not extend it to the most granular state that users would ultimately want in order to capture product structure. The material database/definitions would also be important for regulatory compliance with users, as well.
*Weight. This is a must have but needs to be couple with material properties, you need to know the exact materials the weight is calculated on. It could be good in an assembly to itemise material weights, then you know if you have not got the properties mixed up. e.g. you should know if your assy is meant to be all steel, or a split between aluminium, plastic and steel.
*C of G. This is a must have. Ideally coupled with the weight command but also the ability to save to part for reference to calculations. It would be nice if when the C of G is saved to the part you could hover and also see the weight as normally I would be using the C of G and weight to calculate a lifting ram or spring capacity.
*Surface area. Has to be also on the section tool as I regular compare section surface area during design. I would also use Surface area this to give an estimate of paint volume, it would be nice to have an external faces only switch.
The external dimensions e.g. box size would be a nice feature.
Twitter: @onshapetricks & @babart1977
Mark
Twitter: @onshapetricks & @babart1977