Welcome to the Onshape forum! Ask questions and join in the discussions about everything Onshape.
First time visiting? Here are some places to start:- Looking for a certain topic? Check out the categories filter or use Search (upper right).
- Need support? Ask a question to our Community Support category.
- Please submit support tickets for bugs but you can request improvements in the Product Feedback category.
- Be respectful, on topic and if you see a problem, Flag it.
If you would like to contact our Community Manager personally, feel free to send a private message or an email.
Model broken, server in invalid state
I left my model earlier today in a fine state only to return to it now completely broken.
The main assembly is bleeding red, and the subassemblies are too.
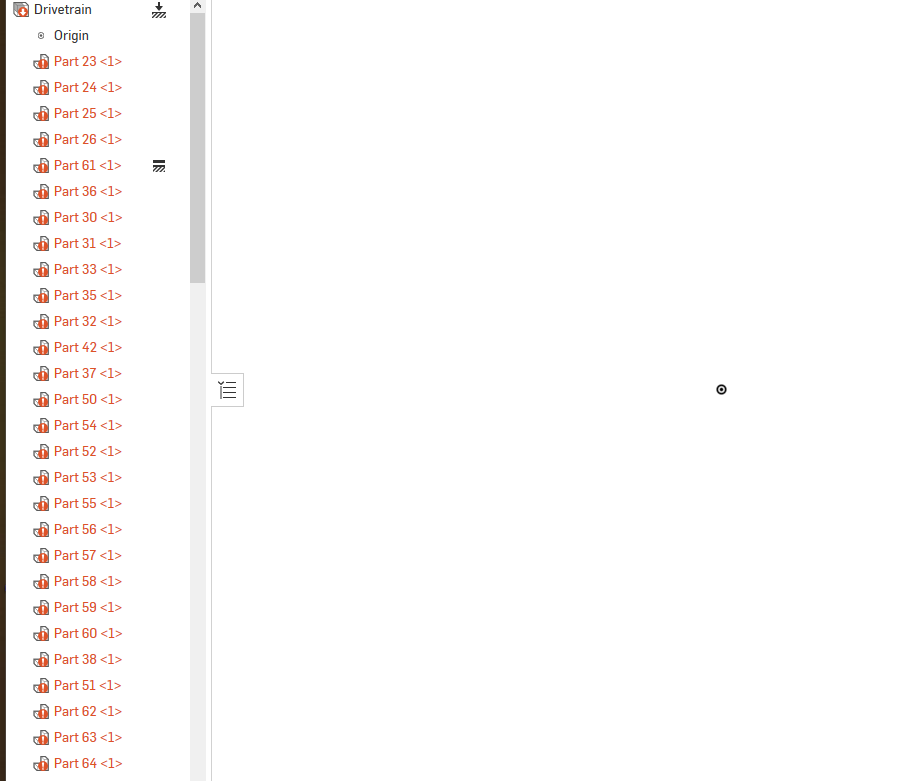
I see in the feature history that tech support did a number of rollbacks, no doubt to help, and I figured I'd just revert to what I know was my last known good version.
No luck. I tried reverting to a still earlier version, but same problem. Lots and lots of red.
There are red mates and there are red parts, and if I hover over the red parts I get the error message that the server is in an invalid state.
Twice before I've returned to models I knew I'd left in good state only to find them mysteriously broken---in one case many weeks after I'd last visited the model. One of those models, my hardest and longest to date, wound up in the trash bin.
Is Onshape aware of the issue? Is something being done to prevent models from breaking like this? You can't work on a broken model---it's gridlock, a complete road block---and you can't stop wondering if and when and how you'll get your model back, emphasis on if.
Tagged:
0
Comments
I have fixed this and verified that all assemblies open as expected.
I took a look at the document and logs and saw a couple of things:
1. A number of events over the last week that should have manifested as support codes. Did you see support codes over the last few days?
2. These events were caused by resource limitations caused, I believe, by a modeling anti-pattern common in your document: deriving from the same (giant) part studio using multiple derive features, rather than deriving multiple parts using one feature. Make that change throughout your part studios and I expect you'll see much better performance and fewer issues.
TL;DR: No more than one derive feature per base part studio.
@john_mcclary
When did you have this happen? Could you please dm me with a zendesk number when you had a "document isn't what it used to be" issue?
The machine is large and complex, and that means the model will be large and complex. I wish it didn't have to be!
The part studios grow large because every part depends on every other, or close to. I would have hundreds of small part studios if I created one per part or even one per ten parts. As is, I have tens of part studios. I think Onshape has a blog highlighting the ability to model multiple parts in a single studio as a strength?
Well, I often have to update the versions of some but not all derived parts. This is very important to me. If I update the versions of certain derived parts, the model breaks: a simple change in a dimension or constraint can cause an Extrude or Split or Delete Part to go wrong, meaning hundreds of broken features downstream and a week lost over what at start was a simple change in a dimension or constraint.
Onshape is very picky on this matter. I could extend an Extrude by a fraction of an inch only to discover that part IDs following a split downstream have changed, causing a Delete feature downstream of the split to remove the wrong part, causing tens of sketches and extrudes and sweeps dependent on the now missing part to break, causing a week to go by just to get back to an unbroken part studio.
And yet, these are things I need to do.
So... I avoid the issue by using multiple Derived features and updating only those that I absolutely must---and only if I absolutely must, as every update comes with the risk that things below the Derived feature will break. And I insert my Derived parts as far downstream in the feature history as possible, so that I don't inadvertently use them as references early on, and so that if I update them, I don't have to wait for the entire feature stack to regenerate
TL;DR: I need multiple Derived features per part studio so that many things don't break when I update the Derived version.
It sort of sounds like establishing all the positioning in a top-level assembly and then using in-context modeling may be a better approach than deriving at different versions into your part studio. Then your top level assembly could contain the versions you are currently comfortable using, and you can update the context as appropriate when you want to edit specific parts.
Just my take on it though, maybe are things that block this approach for you.
When doing in-context, we only actually bring in the geometry that is referenced by a feature. The rest is just a ghost that does not actually affect the part studio. So, it matters when you ask about slowing things down if you are asking about interactive performance (rotating, panning, zooming the model) or regeneration (regen) performance (how long it takes to change/add features). In-context should be much better for regen performance because it just has to copy a little bit of the context into the Part Studio and then use it for the feature. It might slow down interactive performance depending on your machine though, because as you say we will be displaying the entire assembly.
The regen performance compared to deriving more than once from the same complicated part studio should be drastic though. When you derive from a part studio, we need to regenerate that Part Studio to get the result of the derive. If you import the same Part Studio twice, you are doing that regen twice and then extracting different data both times. With in-context, you just take a snapshot of the geometry as it is (one-time cost) and are making little extractions from that, no regen required.
Ideally, yes, and we try to do as much version caching as we can. Realistically, we cannot possibly store the full geometry for every version saved in the system. It would be a _lot_ of data. The "snapshot" in the version is a snapshot of the state of the Feature List, and we put tons of safeguards in to make sure that that Feature List regenerates the same every time.
We'll be going over designing in an assembly at our user group on March 11th. We'll be webcasting it, 6pm pst.
https://rustyshed.com/?quill=5e52a6dbf97817411d9b45dc
"anti-pattern" what the hell is that?
http://agilemodeling.com/essays/enterpriseModelingAntiPatterns.htm
The problem with everything talking to everything else, it's chaotic. I'm not sure what you're building, but choose your references wisely. If you want it to scale keep it organized.
In the past, we wouldn't allow reference across sub-assy's. All reference went down to lower dependencies only and stayed in a branch of the tree. You could say that's an extreme limitation, but we had 6 engineers designing and no engineers fixing what other did.
It's a big, post your project structure if you figure one out.
Here's the part studio that has my make parts:
The bearings and cylinder came from mcmaster and assembled in the assy but are used to make the parts (incontext).
Attach inserted components to sketches in the assembly.
Change the sketch in the part, goto the assembly and update.
Make sure to call the sketch "skeleton".