Welcome to the Onshape forum! Ask questions and join in the discussions about everything Onshape.
First time visiting? Here are some places to start:- Looking for a certain topic? Check out the categories filter or use Search (upper right).
- Need support? Ask a question to our Community Support category.
- Please submit support tickets for bugs but you can request improvements in the Product Feedback category.
- Be respectful, on topic and if you see a problem, Flag it.
If you would like to contact our Community Manager personally, feel free to send a private message or an email.
HELP! Gears (Globoids & Other types)
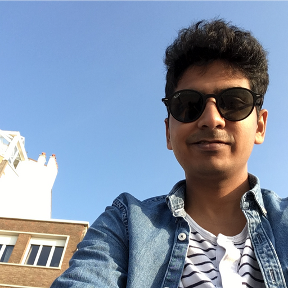
Hello folks,
I need help with creating various types of gears in Onshape. I am a Design Bureau, so work-around with circular arcs, or other methods will not work all the time, as I have clients sometimes ask involute profile on the gear. Please keep in mind about this, when giving me feedback/suggestions, and I appreciate your help.
Spur/Helical Gears
I use Onshape Custom Tools "SPUR GEAR ( https://cad.onshape.com/documents/6527d86ca7126bbe5b04ca08/v/83e5f3eba1ab6d76e8deeb45/e/3ea2b29bac4713685544dc37 )" & "PLANETARY GEARS ( https://cad.onshape.com/documents/b55a80bb510b8ff5cb20fd9a/v/48a8d665dd43d50680e9ca65/e/24256daec5d2bac4406f58d6 )" to generate these type of gears. I assumed they already follow involute profile, and helix profiles. I have two limitations with these tools:
Ring Gear: I have to manually generate Ring gear most of the time. As extracting Ring Gear from "PLANETARY GEARS" tools is tricky sometimes. I generally calculate module of gear set, and create a normal spur gear with tooth number near to my calculations, and then project sketch of single tooth on Ring gear pitch circle, and create gear from that. Is there any specific custom tool for creating Ring Gears?
Teeth more than 1000: Sometimes I have design inputs like, "shaft/ring thickness of 4mm, with 3mm gear tooth height", and I have instances where sometimes calculations show tooth number like 1300. I know this is rare, but this happens with some R&D projects, where ideas are being explored. In tools mentioned above, current limit on teeth number is 1000. So, again I create sketches with pitch circle and other gear parameters, and copy sketch of one tooth from smaller with same module, and paste it on required gear pitch circle. However Onshape has difficulties in multiplying features in these numbers (checked with support and confirmed this, and they also provided some suggestions on how to approach this), and so document goes into forever reload, when I do circular pattern on tooth. Instead, I create gear blank and tooth as separate parts, and create a assembly with these in exact same position, and do circular pattern in assembly. I do same colour to both, so it looks like gear. This is faster, and doesn't break files. I want to ask others is there any other methods people are using for these kind of situations?
Of other type of gears (except Worm Gears & Globoids), I didn't work on designing them yet, but I would like to ask, if there are any specific customs tools out there, for Bevel gears, Hypoid, etc.
Worm & Worm-Gear
Like explained above, I do calculations, and create a spur gear for worm-gear, and copy one of its teeth to create worm using loft. This kind of worked, as these models are not used to create production drawings, or something like that. Things like throat, or if helical gear is involved as worm-gear, I haven't tried creating those. Tricky thing is, addendum to dedendum ratio in worm-gear setup is different to spur gears, and also have variations to it, depending on lead angle. So, my method of creating worm-gear set up is not accurate. Any suggestions here?
Globoid
On one of my current projects, I was asked to size and design globoid-gear in initial design. I felt embarrassed
to not know what it is, and how to create that. I still didn't succeed in creating this, but tried few things as explained below:
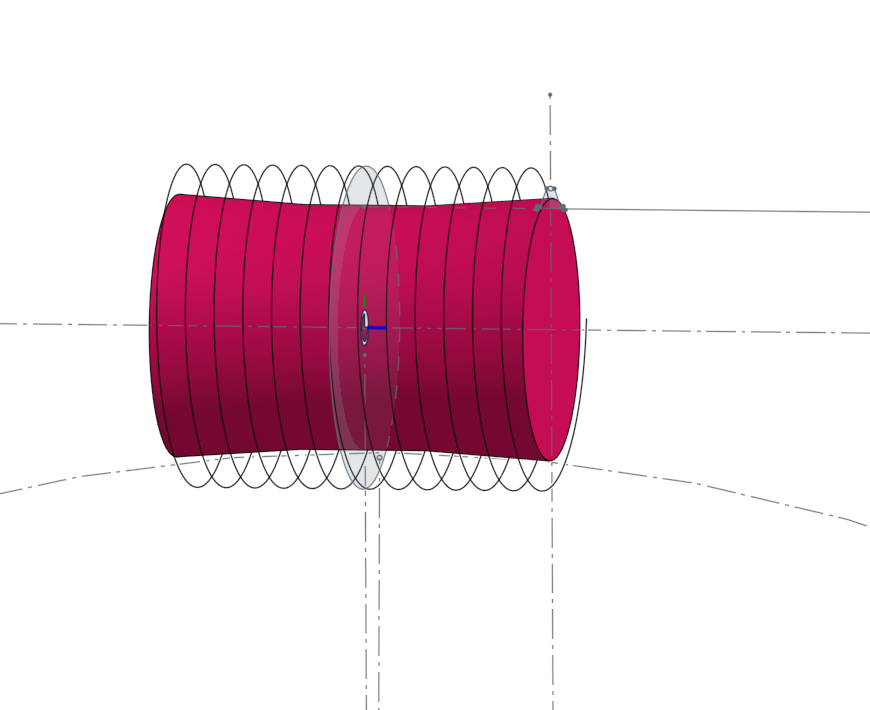
Another thing, generally I consult "Shigley's Mechanical Engineering Design" to verify my calculations. It has some good explanations, majorly for spur/helical gears, with some inputs in bevel and worm gears too. But if someone can suggest me a book that has some thorough reasoning on all kinds of gears & design, with their parameters, equations, etc. I would appreciate that.
Thanks,
Chandra
I need help with creating various types of gears in Onshape. I am a Design Bureau, so work-around with circular arcs, or other methods will not work all the time, as I have clients sometimes ask involute profile on the gear. Please keep in mind about this, when giving me feedback/suggestions, and I appreciate your help.
Spur/Helical Gears
I use Onshape Custom Tools "SPUR GEAR ( https://cad.onshape.com/documents/6527d86ca7126bbe5b04ca08/v/83e5f3eba1ab6d76e8deeb45/e/3ea2b29bac4713685544dc37 )" & "PLANETARY GEARS ( https://cad.onshape.com/documents/b55a80bb510b8ff5cb20fd9a/v/48a8d665dd43d50680e9ca65/e/24256daec5d2bac4406f58d6 )" to generate these type of gears. I assumed they already follow involute profile, and helix profiles. I have two limitations with these tools:
Ring Gear: I have to manually generate Ring gear most of the time. As extracting Ring Gear from "PLANETARY GEARS" tools is tricky sometimes. I generally calculate module of gear set, and create a normal spur gear with tooth number near to my calculations, and then project sketch of single tooth on Ring gear pitch circle, and create gear from that. Is there any specific custom tool for creating Ring Gears?
Teeth more than 1000: Sometimes I have design inputs like, "shaft/ring thickness of 4mm, with 3mm gear tooth height", and I have instances where sometimes calculations show tooth number like 1300. I know this is rare, but this happens with some R&D projects, where ideas are being explored. In tools mentioned above, current limit on teeth number is 1000. So, again I create sketches with pitch circle and other gear parameters, and copy sketch of one tooth from smaller with same module, and paste it on required gear pitch circle. However Onshape has difficulties in multiplying features in these numbers (checked with support and confirmed this, and they also provided some suggestions on how to approach this), and so document goes into forever reload, when I do circular pattern on tooth. Instead, I create gear blank and tooth as separate parts, and create a assembly with these in exact same position, and do circular pattern in assembly. I do same colour to both, so it looks like gear. This is faster, and doesn't break files. I want to ask others is there any other methods people are using for these kind of situations?
Of other type of gears (except Worm Gears & Globoids), I didn't work on designing them yet, but I would like to ask, if there are any specific customs tools out there, for Bevel gears, Hypoid, etc.
Worm & Worm-Gear
Like explained above, I do calculations, and create a spur gear for worm-gear, and copy one of its teeth to create worm using loft. This kind of worked, as these models are not used to create production drawings, or something like that. Things like throat, or if helical gear is involved as worm-gear, I haven't tried creating those. Tricky thing is, addendum to dedendum ratio in worm-gear setup is different to spur gears, and also have variations to it, depending on lead angle. So, my method of creating worm-gear set up is not accurate. Any suggestions here?
Globoid
On one of my current projects, I was asked to size and design globoid-gear in initial design. I felt embarrassed

- Like in worm-gear, I created globoid blank with root circle (calculated), and created a helix at pitch diameter. Now what I wanted to do is, project this helix onto globoid blank (image below), and loft like normal worm gear. This is not a perfect globoid, but would work for now. But I couldn't proceed further because I am unable to project helix onto globoid blank. I didn't explore much here, as I found other methods like explained below, which I didn't succeed as well
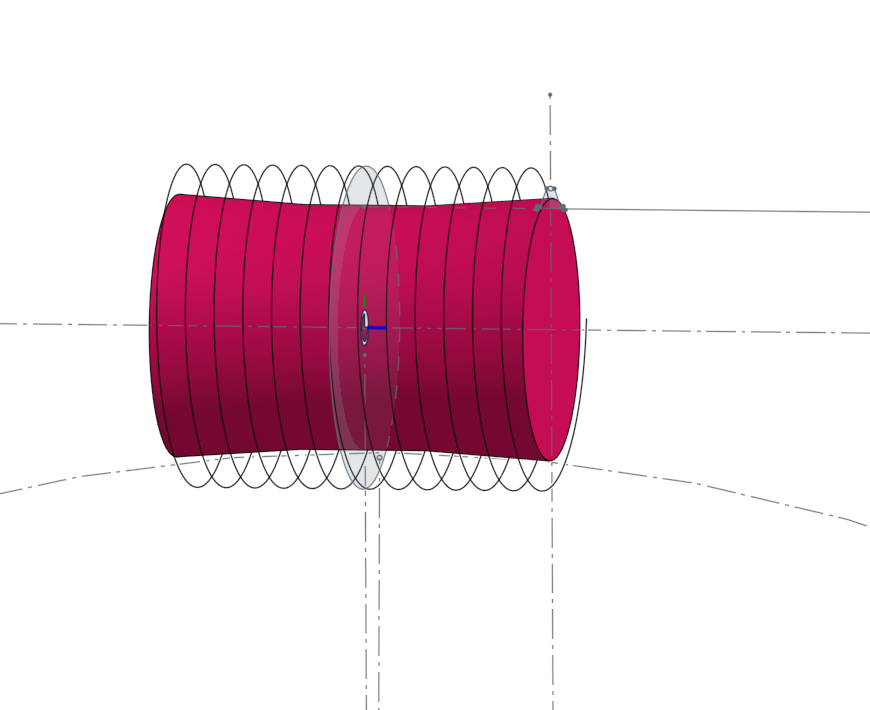
- I also thought, creating a variable radii helix using "Parametric Equation curve ( https://cad.onshape.com/documents/578ff8b3e4b0e65410fcfda3/w/d33395f174e5b38f4abd6097/e/cc0c3d5644a78b1b64d6c3b4 )", and using equations mentioned in link https://www.zwsoft.com/support/zw3d-base-skills/1378 . This will be my last ditch option. I have to dust off my math, but I am wondering surface on which this helix sits is a cone, but globoid surface (root dia) is not cone, and has curvature. Thats why I didn't explore this option completely
- I checked Onshape forums, and came across a discussion, where @konstantin_shiriazdanov posted few suggestions. https://forum.onshape.com/discussion/13641/globoid-thread He shared a file that contains his work on globoid creation but I couldn't make "Curve Generator https://cad.onshape.com/documents/d8aab1e0e7ae10038a6830e0/v/5c9f65e4909a623a7644a665/e/421758eb171fa79c9a45f9a6 " tool work. I couldn't get my head around it, and figure out how it works
- I also came across this link https://spiralbevel.com/ , and thought of following their method, but their excel sheet that generates tooth curve is not available
Another thing, generally I consult "Shigley's Mechanical Engineering Design" to verify my calculations. It has some good explanations, majorly for spur/helical gears, with some inputs in bevel and worm gears too. But if someone can suggest me a book that has some thorough reasoning on all kinds of gears & design, with their parameters, equations, etc. I would appreciate that.
Thanks,
Chandra
Tagged:
0
Comments
- Is this just visual for reference and you're buying off-the-shelf parts?
- Is this something which will just be 3D printed for fun?
- Is this for a one-off machine, or a high volume consumer or medical product?
- Will these gears be machined or injection molded?
- Will the gears be metal or plastic?
- How small are the teeth?
- Are you trying to do FEA on the models?
In my experience, hiring a professional gear designer who uses specialized CAD tools is essential for good performance, especially with molded gears (gating, shrink and draft on plastic gear teeth has complex effects on noise, wear, and torque). Similarly, tool design and molding for plastic gears is not something you want to hand off to any random injection molder.If it's a metal gear, chances are good that the manufacturer will use specialized gear cutting tools which will help to create the profiles you need.
Drawings and inspection of gears also requires specialized tools and techniques. If you don't know what to ask for you may get something that kinda works like a gear, but doesn't perform very well.
Simon Gatrall | Staff Mechanical Engineer | Carbon, Inc.
@S1mon & @nick_papageorge073 Thanks for your inputs. Like you said, when it comes to exact gear design, I leave it to respective manufacturer for actual design. In the past, when there is a gear, I generally make cylinders with pitch circle, to mimic gears (with other features that are important for its fixation, etc). But recently, some of the clients started asking gear in the design to be more representative of actual piece. Spur Gear tool works for most of my cases, but I had instances like once, a client asked me he wants a hypoid gear, and teeth to be with involute profile.
About those Globoid gears, I can't go into exact specifics, but we are in preliminary stage in R&D on a certain project, and we need teeth and approximate representation, because we are trying to estimate weight (very critical to application) of assembly. So, similar method to worm-gear (my method) should help, even though teeth is not same as spur teeth, but I couldn't get the helix (spiral) required for loft in globoid case. So, yeah I am looking for approximate designs in this case.
I created this thread, to gain some knowledge on how different designers are approaching gear designs. Also designing gears felt a bit challenging , and made me curious.
The Onsherpa | Reach peak Onshape productivity
www.theonsherpa.com
@konstantin_shiriazdanov I didn't get time to work on your method, but I noticed I didn't use fix constraints in sketches. I will explore this further, and if I have more questions, I will post in this thread. Thanks again.
Can you please tell me what does parameters "Screw Padding" , "Fall off" , "Vertices per Screw Loop" do? Or how we can use them to tailor your needs?
About limit, not just on your tool (I checked your FS), but also actual "Gear" & "Planetary Gear" tools in Onshape, why teeth is limited to only 1000. I know you rarely go beyond that, but I am working on a project where we are assessing a design of an assembly with some titanium gears with CF base, in which I have more than 1000 teeth. Is there any particular reason why 1000 is the limit for gear tooth generation in Onshape?
I am new to FS, so didn't know about this "bounds spec". I will update to your current version.
To give you an idea, my parameters wrt tool inputs are as follows:
px = 0.10923in, so module m = 0.03477in
teeth in gear = 1275
gear width = 1-1.5in (currently I kept my models with 1in width)
attack angle = 20deg
teeth in screw = 10in/px = 91.54, so 91 teeth, as I need globoid screw to be around 10in long
screw diameter = 2.7405in (pitch diameter of screw)
I will try to recreate my models and get back to you.