Welcome to the Onshape forum! Ask questions and join in the discussions about everything Onshape.
First time visiting? Here are some places to start:- Looking for a certain topic? Check out the categories filter or use Search (upper right).
- Need support? Ask a question to our Community Support category.
- Please submit support tickets for bugs but you can request improvements in the Product Feedback category.
- Be respectful, on topic and if you see a problem, Flag it.
If you would like to contact our Community Manager personally, feel free to send a private message or an email.
Mirror in assembly
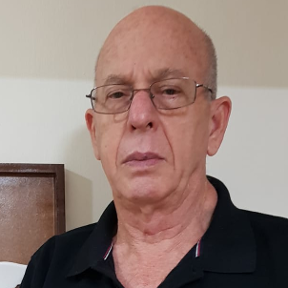
in General
Why Onshape don't have mirror/pattern in assembly????
1
Comments
Simon Gatrall | Staff Mechanical Engineer | Carbon, Inc.
I'm thinking in OS geometry is best created in a part studio and assemblies are for managing parts. Why not create the mirrored parts inside a part studio and then bring them into an assembly?
If you're thinking that's not a traditional part/assembly relationship, I have no argument.
I think it's safe to say that we've shoe horned parts & assemblies into CAD and the old definitions of these are changing.
I'm finding that creating geometry in part studios, creating parts and then moving parts into an assembly is working best for me. At least that's what I'm believing today.
If you have better ideas, please share them.
Any mate connector in an assembly can serve as a center of symmetry for placing instances in a mirror relationship, or as the origin of a part studio in which a part can be duplicated and mirrored.
This combination of techniques has been able to cope with nearly every "mirror" situation I've encountered since leaving Solidworks behind. I'm eager to see whether the much-anticipated improvement request will add any further value.
@edward_petrillo I'm glad you brought up SW because I knew this thread would end up there.
Demoing the assembly mirror feature in SW was "yes Mr. customer one feature will handle all your mirroring needs". But in reality 50% of the people don't get it and it's difficult to maintain especially if you didn't create it. Parametric modeling should be about predictable change and I'm not sure mirroring in the assembly is predictable across an entire engineering department. We called this type of stuff "demo candy" because it gets everyone excited, but can it be implemented?
If I had an engineering department, I'd probably stick to just mirroring the parts in a part studio and have the people mate the mirrored parts manually. If I opened up one of my engineers project I could easily see which parts are declared as left & right. I'm not sure symmetry in an assembly is always the case. My left brake is not symmetrical to my right brake on my bike. I try to make them symmetrical, but they're not.
I'm always thinking about the next guy and how much work he has to do to figure out what I've done. Keep it simple, keep it transparent, keep it understandable and keep it accurate. I'm thinking that's what CAD should be.
You've definitely mechanized the mirror process in the part studio. I'm wondering why you don't keep the original body? After all it's about a left & right.
Also, in production, you need to name the mate connector and tell me what they're doing. The only way to know what's going on is to make a copy of your feature script and then go through and toggle all the options watching everything rebuild.
This is what I'm thinking:
In the part studio I can click on the mirror feature and see that it created a "hand right"
And then in the assembly
I just add the right hand.
The nice thing about this approach is that mirroring the hand didn't affect the assembly. This means that if this assembly was in production I can easily adapt LH & RH to the part studio. If hand was used all over the place, I could perform this operation, creating a LH & RH version of a part wouldn't interfere with any production lines.
Adding the RH to the assembly would impact production for that particular product line, and it should.
Really for any business, we really need to focus on how we're impacting manufacturing and is our data set manufacturing friendly.
Before:
After:
My mirroring a part in an assembly requires one feature in a part studio and one mate connector in an assembly. This technique uses core OS functionality and is manufacturing friendly. I think I could explain this to someone who just graduated from engineering school and make him a valuable asset to my company. I think if I shared this data set with a machinist who hates computers, he'd get it.
I'm slowing convincing myself this is a good technique. What am I missing?
Back in the old days many designs had -01 shown & -02 opposite. I think if you were to use that nomenclature today you'd be rejecting all the -02 parts because machinist just wouldn't catch it. Since machinist work off of CAD files, you have to ensure that the -02 is captured in the file name otherwise you'll have problems. And, don't forget the revision number in the file name. Can your machinist work from a shared OS document? My machinist can but won't.
I'm not a fan of configurations and prefer a new part number. I read an article along time ago that a part number is just a sequence of differentiation and should have no meaning. I still believe that. I'm really hesitant about adding dash numbers to a part number.
In my bom, my new mirrored part would need updating. I like the fact that OS's boms are really easy to edit. My new part would have blank fields which is pretty easy to spot and fix.
What's good for my company may not be good for your company. What's most important is that everyone in your company agrees to how things should be done.
Is everyone including your machinist on board with this process you've developed?
I'm probing and probably shouldn't be. In the US, a lot of engineering departments are every man for themselves which I'm opposed to.
You're working for a design firm and can get away with more flexibility than a production house.
It's cool that you had a small problem, banged out a script, and got'r done. That's impressive.
I outsource my work too and manage step/pdf files also.
I too was bother in the beginning without a mirror feature in onshape assembly. I have found it actually kind of refreshing to not having it. In solid works, I found I was continually having to delicately modify things for fear I would some how disturbed the delicate relationship the mirror feature had created in the mirrored part. I would like a mirror feature in onshape assembly but only for holding a part in the same position as another across a mirror plane. If you want a very quick way of creating a mirrored part without having to premeditate its existence too much, here is how you can do it with a move forward type of workflow instead of trying to trace backwards into possibly released parts territory.
- Mate parts in your assembly and realize that a part created by someone else needs to have a mirrored version in your use case.
- Create a part studio in-context and use the assembly origin as the mate connector.
- Create a translate feature and use the option, "copy part in place" and select the in-context part you wish to created a mirror of. Now you have the original part sitting in the proper position with respect to the assembly origin.
- Mirror the part as desired.
- drop the mirrored part into the assembly and it falls right into position.
Now if we could just create a symmetric mate or mate connector the uses entities from different instances we would be golden. What I like about this is there is no going backwards. You maintain you forward momentum. Also, the mirrored part is a perfect mirror but does not necessarily always follow the parents geometry changes unless you very deliberately tell it to by updating the part studios assembly context. Also, this method require no modifying of the parent parts document. If you decided you wanted the part studio to hang with the parent, you can just move it to the parents document which seems easier to follow if you are the creator of the parent part and come back to it a year later. seeing the version history shows clearly that something was moved in rather than attempting to decide if any other changes to the parent part were done during the creation of the mirrored part.