Welcome to the Onshape forum! Ask questions and join in the discussions about everything Onshape.
First time visiting? Here are some places to start:- Looking for a certain topic? Check out the categories filter or use Search (upper right).
- Need support? Ask a question to our Community Support category.
- Please submit support tickets for bugs but you can request improvements in the Product Feedback category.
- Be respectful, on topic and if you see a problem, Flag it.
If you would like to contact our Community Manager personally, feel free to send a private message or an email.
Laserkiste – a parametric finger joint box for laser cutting (stackable!)
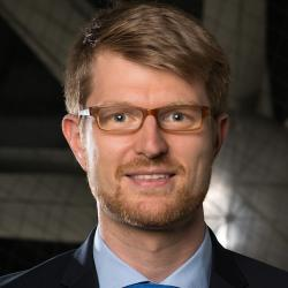
Hi Everyone,
The Onshape Document is called Laserkiste (German for Laserbox). Feature list:
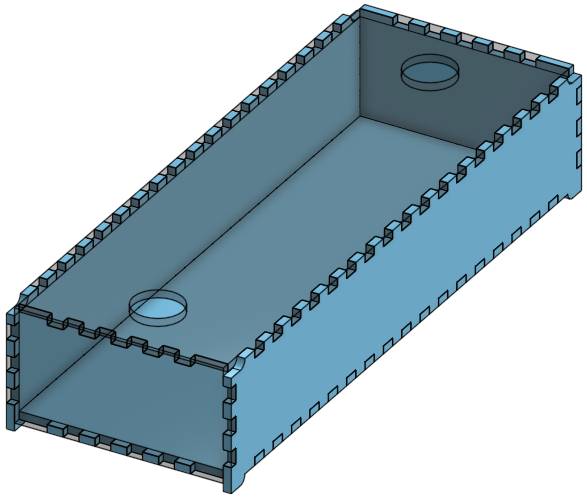
PS: My favourite existing webtool: Makercase
based on those countless designs of simple boxes with finger joints I made my own. Why? Because I wanted a stackable version that scales as I need it. And sometimes you want to make adjustments that are quicker in Onshape than in a vector graphics tool.
The Onshape Document is called Laserkiste (German for Laserbox). Feature list:
- Variables for inside length, width, height, material thickness
- Variable for finger width
- Finger count needs to be updated manually (They are calculated as #n_l, #n_h, #n_w , but linear patterns don't like variables yet)
- Corners/Feet that are stackable
- Take laser kerf into account => Booleans with "offset all" + extra Extrusion to make it 2D again
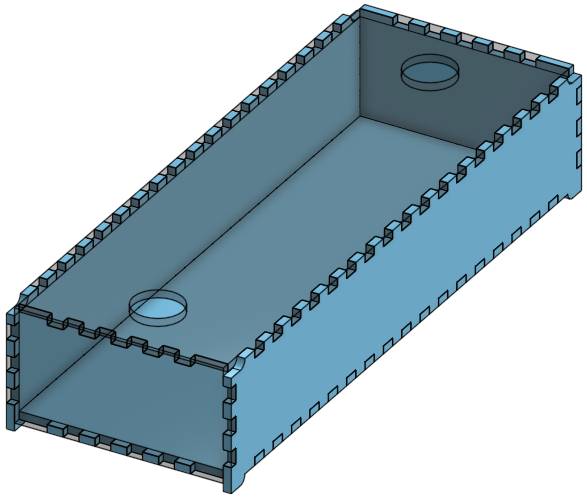
PS: My favourite existing webtool: Makercase
Tagged:
5
Comments
florian said: Take laser kerf into account => Booleans with "offset all" + extra Extrusion to make it 2D againI love the boolean offset tool, works an absolute treat for projects like this.
What do you mean by "+ extra Extrusion to make it 2D again"
Twitter: @onshapetricks & @babart1977
You can also use Select other as shown in the pic below.
Twitter: @onshapetricks & @babart1977
The only way I can workout how to get it to work as fully parametric model would be to use the Boolean offset all, then to clean up the unwanted offsets with an extrude of the top face (by selecting the top face you will always get all the fingers), then another extrude of a sketched rectangle on the top face referencing the inside edges. Both to the thickness and merging to the top part.
Twitter: @onshapetricks & @babart1977
I encountered the same problem trying to adjust for laser kerf. "Offset All" isn't really applicable (because it offsets too many faces), and selecting individual faces is a *lot* of effort in a larger design.
I am hoping OnShape will address this use case — anybody who laser-cuts designs will have the same problem.
Here's a selection idea for Onshape: Select a face, then choose "Propagate Selection", either directly from RMB, or perhaps as a subchoice within "Select Other". Then select an edge on that face to specify what direction to propagate selection, then roll the mouse wheel until the desired number of faces have been selected. During this process it would be possible, at any point, to "steer" the propagation in a new direction by picking a new edge on the last face selected. (The default edge adjoining the next face to be picked having been highlighted as each face was added to the selection set). If at any stage, the "wrong" next face is added, simply roll the mouse wheel in reverse to deselect it, then steer the selection by picking a different edge.
The same functionality would be useful picking surfaces on Surface Bodies.
In the meantime, it might be worth experimenting with the capability explained in this post by @lougallo, which is less controllable, but more powerful:
https://forum.onshape.com/discussion/125/creating-selection-sets
Twitter: @onshapetricks & @babart1977
I agree, being able to tag faces in some way for DXF export would be useful.
We are using a parametric modelling tool, so one typically models just a fraction of the entire assembly. You use a driving sketch, lots of mirroring, and then boolean operations to build the interlocking parts. It doesn't make sense to add offsets in the sketches, because they will get applied to both sides of your subtract operations. It doesn't make much sense to add them later (after the boolean ops), either, as it requires painstakingly selecting all the faces that need the compensation applied. And you still end up with an incorrect 3D model, where your parts intersect each other.
Theoretically CAM tools are supposed to compensate for kerf, but it seems that in the laser-cutting world none of them do.
What I would love to see in OnShape is slightly higher awareness of the laser cutting process. Tagging faces for DXF export is one thing, but let's take this further — at this stage we still have the full 3D model available, so OnShape knows what's "inside" and what's "outside" in the outline being exported. At this stage it is very easy to adjust for kerf — offset all the "outside" profiles with a positive value (make them effectively larger), and offset all the "inside" profiles (holes, basically) with a negative value (make them effectively smaller).
Once OnShape exports to DXF, the inside/outside information is lost and can sometimes be hard to retrieve unambiguously.
I would be very interested in taking a look at the API, but it doesn't seem publicly available? Perhaps with a little tagging support inside OnShape all the rest can be done externally?
One thing I'd like to note is that if OnShape can nail this process, people who laser-cut 3D designs would love it immediately. There is no solution for this problem out there, just google for laser kerf compensation and see how much effort people expend on it in programs like CorelDraw, Inkscape, and others.
summing up: kerf isn't a CAD but a CAM problem.
Now I'm waiting for parametric linear sketch patterns and I'll be able to finish this document.
Twitter: @onshapetricks & @babart1977
Instead of waving the problem away, I was suggesting we think about how to improve things. After all, OnShape is supposed to be about rethinking CAD. So far my thinking led me to the conclusion that once you export the 2D DXF face outlines, you already lost information, and the CAM software has a much harder job, because you can't differentiate between product and waste. Which is why I was suggesting that instead of drawing a thick line between CAD and CAM, OnShape could accomodate some features which would make the process easier.
I'm not sure that hobbyists are Onshape's target market.
They're an important group for Onshape, certainly, because they may end up in a professional capacity as paying users (or that may be their day job), but essentially it seems to me that Onshape is primarily setting out to provide industrial-strength CAD for industrial users. You may have noticed they've strenuously avoided setting a hobbyist-level paid subscription offering.
So it's not so much, perhaps, a question of waving the problem away, but of seeing that problem in the context of the core users of Onshape. It makes sense to me that they would focus the development resource on what's important to those users, and minimise adding capabilities (and the associated interface clutter) which would be extraneous for those users.
Twitter: @onshapetricks & @babart1977
Kerf Compensation, T-Slot Joint, and Laser Joint.
PhD, Mechanical Engineering, Stanford University
The link should have a colon (':') after the https at the start
IR for AS/NZS 1100