Welcome to the Onshape forum! Ask questions and join in the discussions about everything Onshape.
First time visiting? Here are some places to start:- Looking for a certain topic? Check out the categories filter or use Search (upper right).
- Need support? Ask a question to our Community Support category.
- Please submit support tickets for bugs but you can request improvements in the Product Feedback category.
- Be respectful, on topic and if you see a problem, Flag it.
If you would like to contact our Community Manager personally, feel free to send a private message or an email.
Workflow for importing parts
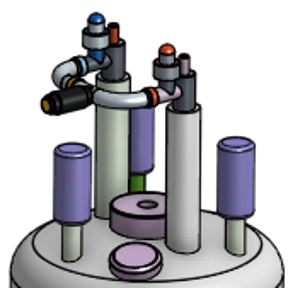
I recently did a design which required a couple of imports (motors, bearings, profiles...). While everything was possible I think that the workflow could be improved significantly with some small changes. Here my observations and suggestions for improvements.
1) Importing parts
a) Importing a part (step file) opens two tabs, one with just the name and some file informations and one with the actual part. I have no idea what the first tab is meant for and usually delete it without consequences.
Suggestion: Don't generate the first tab
b) Parts are imported into their own part studio. Besides cluttering the tab bar with a lot of part studios only containing single screws, bearings etc. this requires an additional "derive" into the part studion where the part is actually needed.
Suggestion: Allow direct import into an existing part studio
2) Transform of derived parts
After deriving the imported part into the part studio it needs to be transformed to the correct place. The 'transform by mate connectors' works nicely for this but it requires 3 features in the feature tree for each part (derive, generate mate connectors, transform)
Suggestion: It would be much cleaner if the mate connectors could be defined directly in the transform dialog (like it is done in defining a mate in an assembly). If 1b) is implemented it would be even more clean if the import feature would contain the transform and the definition of the mate connectors. I.e.importing a part and placing it would be all contained in one feature.
Regards
Lutz
1) Importing parts
a) Importing a part (step file) opens two tabs, one with just the name and some file informations and one with the actual part. I have no idea what the first tab is meant for and usually delete it without consequences.
Suggestion: Don't generate the first tab
b) Parts are imported into their own part studio. Besides cluttering the tab bar with a lot of part studios only containing single screws, bearings etc. this requires an additional "derive" into the part studion where the part is actually needed.
Suggestion: Allow direct import into an existing part studio
2) Transform of derived parts
After deriving the imported part into the part studio it needs to be transformed to the correct place. The 'transform by mate connectors' works nicely for this but it requires 3 features in the feature tree for each part (derive, generate mate connectors, transform)
Suggestion: It would be much cleaner if the mate connectors could be defined directly in the transform dialog (like it is done in defining a mate in an assembly). If 1b) is implemented it would be even more clean if the import feature would contain the transform and the definition of the mate connectors. I.e.importing a part and placing it would be all contained in one feature.
Regards
Lutz
0
Comments
At the time of importing any step file kindly select second option (Import files to part studio only ) only then all part will come after import at the right position. Therefore no need of doing transform operation and derived operation. All the associated parts and sub-assembly will come in one part studio only if you import by this method.
For more clarification refer below video.
Lutz
Currently there might be chances you may be selected both option before import therefore all parts are appeared in separate-separate part studio tab. Can you share document link with us therefore we can get detail description about that step file.
An option to reduce tabs is to add all your imported parts into 1 assembly, position with mates if desired once they are all in (you get 1 go at this) export as a parasolid and import that file back in with the flatten to part studio checked. Now you can clean up all the unwanted tab's and derive and assemble as required.
Twitter: @onshapetricks & @babart1977
lutz_niggl, I have one more suggestion.Try to import your step file to Onshape as
after importing if your parts are in single part studio but they are in required position. then you can Export that part studio to parasolid by using "Export part as individual files"
It may reduce one step(putting parts into assembly studio) if your part are in already in required position.
Here i am also having one question that why this option("Export part as individual files") not find for exporting files to STEP or IGES etc?
Here's my ticket:
I found cleaning up assemblies before export goes along ways when importing into OS. Garbage out is garbage in.
Trying to build clean/understandable structures. Wait till you try and add a derived part studio with 50 components in it to another part studio. Let me know your thoughts when you do this.