Welcome to the Onshape forum! Ask questions and join in the discussions about everything Onshape.
First time visiting? Here are some places to start:- Looking for a certain topic? Check out the categories filter or use Search (upper right).
- Need support? Ask a question to our Community Support category.
- Please submit support tickets for bugs but you can request improvements in the Product Feedback category.
- Be respectful, on topic and if you see a problem, Flag it.
If you would like to contact our Community Manager personally, feel free to send a private message or an email.
My list of what's missing.
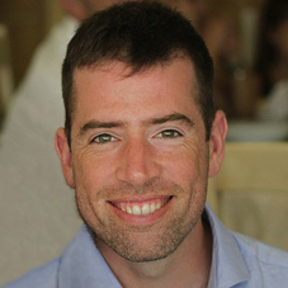
I just finished a job for a client that would have been a good test for Onshape. No existing CAD already in use. A minimal set of output information to communicate. But the capability to communicate the info I needed to just wasn't there. Bummer.
I have a list on my whiteboard of the features I'm waiting for before I am willing to use Onshape in a real project. Here's my list:
- drawings (with export to PDF and DXF)
- common parts (parts shared between workspaces)
- configurations (tables, equations)
- annotations in sketches (mostly to leave design intent notes to myself or other designers)
- traversal of mate relationships (which mate belongs to which part and vice versa)
- better traversal of feature relationships (Which features depend on this one, which features drive this one.)
- better sketch constraint discovery and management (trying to fix broken constraints in a recent sketch is difficult, trying to fix broken constraints in a sketch I'm seeing for the first time would be a nightmare)
- grouping: (sketch elements, features, workspaces, users)
The final issue, grouping, is another thing needed for working with complex designs. I've seen some interesting conversations here on the forum about grouping. When I say group I mean sets of both elements and (sub)sets.
Grouping workspaces allows one to reduce the total set of all workspaces into manageable chunks, and when combined with good naming can help with new team members understanding what subsets of the total set are relevant. Tags can do this a little bit and should be included for those who like them but the mechanics of tags (tags are not normally tagged themselves in the way that groups are often added to groups. tags are typically accessed via recall in contrast to recognition for groups) make them less capable than groups. In addition to aiding in the discoverability, the ability to manipulate groups and subgroups of workspaces could make some tasks such as sharing and deleting easier.
As a side note, I think that sometimes people have the misconception that grouping implies being limited to a hierarchy (a DAG for you CS buffs). It does not.
User grouping makes granting and revoking permissions on workspace groups (and one day individual branches I hope) tractable.
Grouping features can be handy for speeding the work-flow (o-ring grooves, mechanical interfaces, hole patterns, etc) when parametrized, but mostly I just want to compress the feature tree to meaningful chunks that can be comprehended and navigated quicker than the full list.
Grouping sketch elements (blocks in SW, groups in every other graphics program) is useful for patterns and re-use... but like feature groups, often it is also a good way to reduce the complexity of the sketch, partitioning constraints so that they are easier to understand.
That's the stuff I'm waiting for before I invest in building any infrastructure around Onshape... Though if a minimally capable version of drawings + dxf export was available I probably would have tried to use Onshape in this last job.
I should point out that the list on my whiteboard used to be a bit longer and every new release I'm eagerly looking for what I can cross off.
I know a couple have used Onshape in "production". I'm curious what are the rest of you are waiting for? What are the roadblocks for you?
2
Comments
I am in the same boat.These 2 are a must have.
Twitter: @onshapetricks & @babart1977
Would a "group" be similar to an assembly? A way to gather a bunch of components that act as a whole?
I always wondered why we limit our data structures to parts, assemblies & drawings, a concept brought over from draft boards.
Spaceclaim had an interesting grouping algorithm. Basically a saved selection list. Then when applying a function to that list, it would up-select/down-select and choose what made sense for that function. ie.. let's say I pick a vertex and add it a group (select set), then I pick a move body function, SC would up-select the vertex and grab the body and move it. This made selection sets (groups) more useful and powerful.
Maybe I should wait for your response as to why you want groups. I agree that assemblies aren't a good why to gather components.
I don't want drawings and hate dxf.
There are much better geometry standards out there other than dxf. Let's please extricate dxf from our planet.
Working with selection sets sounds interesting. I have not had the opportunity to use spaceclaim. I'm able to do most of what I need to manage a complex design via the hierarchical organization of assemblies but there are a couple areas where selection sets would would help me. The biggest one is for estimating mass parameters for an articulated assembly.
Regarding dxf, I don't have any love for it and I use other formats when I can. It's just the format that every program can deal with and so if Onshape guys on have the resources to do one format of 2D export ASAP... make it dxf.
Twitter: @onshapetricks & @babart1977
my favourite Rhino tool...Bounding Box combined with box edit. Scaling made easy.
I always wonder why people fear splines and I attribute it to acad and it's lack of splines.
@bruce I'm way out there, I realize this more and more every time I post on this forum.
But I've written IGES translators for various companies and g-code for others. I enjoy looking at the
geometry companies are using for their CAD systems and pass judgement based on how well they define their
geometry.
Remember, acad had two siblings when it went to comdex in the beginning which were desktop publishing tools.
Acad was the version that allowed dimensions and people started using it as an engineering tool.
I think it's out of place. Now, you can tell me it generates $billion dollar in sales and I'll tell you
I just don't get it.
SW had really good geometry definitions. Cadkey used a 3x3 with an offset vector (crazy).
Geometry has been defined since 1960's. We should be using a better standard.
Start with iges, then step. We should be barking at the step committee to update the standard to include hole meta data so we know which holes get taped. Some want tolerances and GD&T in the standard. We still have a long ways to go.
Twitter: @onshapetricks & @babart1977
In fact, Trumpf made spaceclaim's sheetmetal really good.
My waterjet guy has one of these:
They mostly do window glazing for the architectural market and they're stuck with all the acad architects. Most of the cuts they make are perpendicular to the glass and all this 5 axis stuff is for show. It will compensate for the waterjet stream expanding and creates the cleanest edges I've seen from a waterjet. So, maybe it's not a total waste.
Guess what this mach4 machine uses for a geometry engine, spaceclaim.
I've been pushing the operator to learn how to run the machine properly and how to use step. To get the machine to cut 5 axis, you define 2 curves in space. The machine then looks at these curves by percentages and defines a vector which it uses to align the head.
Let's say I have 2 curves in space and I want to cut this shape:
Curves always have a start/end (closed splines have special start & stop conditions, but they do start/end). This highlighted vector represents the start on both curves and represents were the waterjet will cut 1st:
This vector represents 25% for both the top & bottom curves and will dictate were the cut head is positioned when 25% complete:
This vector represents 50% and you can to see how 5 axis movements are controlled:
What if the top/bottom curves didn't have a common start point and twisted? Spaceclaim has tools to fix this but it's way out the reach for the kid who runs this machine.
When we waterjet, we have'm cut c'sinks. Why not? just not with DXF.
I looked up .geo which seems to be a trumpf format and is probably gcode. Can you view it? Do you see a bunch of G1, G2 & G3 commands?
How hard would it be to write a .geo output for OS? Not hard, just need access to the API, access to an ordered selection list (possibly chain select), and a little code to remember where you are so you can make proper left/right arc decisions, then write to a file (oops) I'll just email it to you or create a tab with a text file.
One thing I'd check is to send your laser a spline and watch how badly it segments the curve. With iges you'll preserve the b-spline and trumpf may produce a G06. This would produce a nice curve.
There's a lot of golf companies around here and many guys don't like linear interpolated splines. That's what DXF does when converting splines into polylines. I've been fighting for circle interpolation for a long time or some better way to get curves to a controller properly. I'd love to send a controller spline parameters and have the controller produce motor steps based on a spline definition. A lot of guys just grind the facets out after cutting. It's a lot of work.
California Precision has many trumpf machine that do run spaceclaim. I'm not sure what the advantage is other than trumpf now supports step. We just send them SW files and they handled the rest.
Bruce, if all you're doing is lines & arcs. Then use dxf.
Twitter: @onshapetricks & @babart1977
But I know units is still an issue and wonder why autodesk doesn't fix it.
If I send out a DXF I have to change SW units to inches, export dxf, then change SW units to mm. Doesn't sound bad but when you have 50 parts to export, you get tired of this routine.
Do you design in inches? that would make exporting easier.
Most the g-code generators I've created were in Cadkey using CADL. Robert White was a good friend of mine who wrote Fastsurf and got me going with surfaces and curves. That was a long time ago and you don't look that old.
Twitter: @onshapetricks & @babart1977
Twitter: @onshapetricks & @babart1977
Twitter: @onshapetricks & @babart1977