Welcome to the Onshape forum! Ask questions and join in the discussions about everything Onshape.
First time visiting? Here are some places to start:- Looking for a certain topic? Check out the categories filter or use Search (upper right).
- Need support? Ask a question to our Community Support category.
- Please submit support tickets for bugs but you can request improvements in the Product Feedback category.
- Be respectful, on topic and if you see a problem, Flag it.
If you would like to contact our Community Manager personally, feel free to send a private message or an email.
Mate Connector Pair
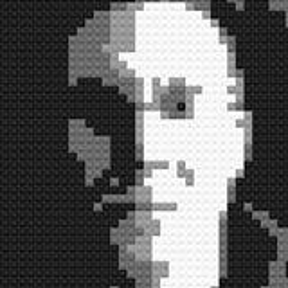
I would like to see an enhancement for a "Mate Connector Pair" - essentially create two mate connectors at the same time at the same location with opposite facing Z-axes and two components to associate. Each Mate Connector would inherit the name of the Pair feature with a "-1" and "-2" suffix.
Matthew Loew
Tera Development Solutions
Tera Development Solutions
Tagged:
0
Comments
Tera Development Solutions
Group the parts first and then mate.
I always forget to group first, so ctrl-z is your friend, then group, then move. I've been doing this a lot.
If any component in the group is fixed, then the group is fixed. Like SW, fixed components are not inherited from a child assembly (every assembly needs the group fixed).
Also, remember there are mate connectors and there are mates. The mate connectors are connected using a mate. Mates allow you define mate connectors on the fly which are limited (can't add translations or rotations to on the fly mate connectors). Stand-alone mate connectors , which I use to position groups must be defined before hand and allow translations or rotations. I typically name these as to not get confused which mate connector controls which group. On the fly mate connectors are neatly tucked under the mate and keeps the tree clean. Stand-alone mate connectors appear in the tree so I use them sparingly because I like to keep things clean & orderly.
I hope I didn't confuse things more.
Right now one has to create two separate mate connectors sequentially. Creating them at the same time would be faster...
Original Post
Ok, so I think I constructed what you guys are talking about.
The Problem
Part studio with 2 blocks:
Assembly with rotate mate connector:
I believe this is new (edit & add move offsets):
You can edit both mate connectors and create a hanging mate connector in space (I really like this):
***Now whats important is that I haven't created a separate mate connector. But as a designer, I not sure this is what I want.
As a designer I want to control the hinge point graphically to make it easier for others to understand what I'm doing. Back in the part studio and create a sketch showing the hinge location:
To pass this location to the assembly I want to access this sketch in the assembly but can't:
A Solution
So I'm forced to create 2 mate connectors in the part studio for each component:
Now I can assembly my controlled hinge point in an assembly to see it move:
I can now move my 2 components with a graphical controlled hinge point using a part studio & assembly:
I think to Traveler's point, is this for real? 2 hinged blocks and it's this complex.
Where is your enhancement going to occur? Will you make this assignment in the part studio or in the assembly?
When editing, do you make the change in the assembly or part studio? Do you have to have a part studio and an assembly for simple motion? Whats the relationship between the part studio and assembly? Can I work in the assembly making all the changes without switching to a part studio?
One thing that's true and little known is that PTC got it wrong with parts, assemblies & drawings and everyone who copied this paradigm got it wrong also. The whole "Top down" and "Bottom up" argument validates that PTC got it wrong and we've all been struggle with this from day one. Sorry about all this, but I joined this forum to have this argument.
I just don't see a clear path on how this should work, I don't think bandaid fixes are the solution. I'd like to see a better foundation for designing with a parametric modeler.
Build a real assembly and see how much bouncing around is required to get something done.
To answer Travelers request, please add motion to the part studio. This is the simplest implementation of 2 bodies that move relative to one another. Why do I need 2 environments for such a simple thing?
I wasn't really suggesting motion for the part studio. It's a really interesting idea. I'm definitely already using underdefined sketches to create these test/exploratory motions. I'll have to think about that....
I agree with you that it would be nice to have sketches available in the assembly for mating or visualization.
We still have the problem that to make a change to a part studio/mate connector, you have to change to that part studio and can't make this change in the assembly. I'm having to bounce around a lot when trying to design in the assembly. In fact, I can't design in the assembly. Maybe I have to wait till rev 2.
I guess it's my request to eliminate the assembly and have one document type in OS. No more bouncing around. Your example of two bodies & a hinge exemplifies this argument. If we continue with part studios/assemblies, you will have to learn how to do this, it's not obvious. Maybe there's some un-realized power coming that I can't see which justifies this approach or maybe it's a hold-over from previous workflows from relic CAD systems. This isn't as simple as turning a light switch on/off.
There's many things that need to happen to make this more productive.
I'm seeing mate connectors as defining motion and DOF's. You're telling me they're datums also.
How would that mate connector update if one of the parts moved? Wouldn't it be better to define a sketch with all the logic and then attach a mate connector to the sketch? A mate connector to many parts, how does it update? Would it be predictable? I guess the proper lingo is it deterministic?
How about this, since a sketch knows it's dependencies due to it's constraints, a mate connector attached to a sketch can find all it's body dependencies. So a mate connector tied to a sketch can automatically define all of it's owners and would allow for predictable change.