Welcome to the Onshape forum! Ask questions and join in the discussions about everything Onshape.
First time visiting? Here are some places to start:- Looking for a certain topic? Check out the categories filter or use Search (upper right).
- Need support? Ask a question to our Community Support category.
- Please submit support tickets for bugs but you can request improvements in the Product Feedback category.
- Be respectful, on topic and if you see a problem, Flag it.
If you would like to contact our Community Manager personally, feel free to send a private message or an email.
FEA in design
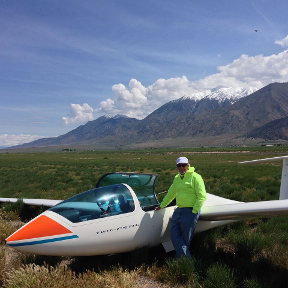
I have a very specific FEA problem that I need an app to analyze. It involves a drum on a rope winch withstanding the constrictive force of a long,slippery rope wound on very tightly. I know how to calculate the constrictive force which can reach over a million pounds total acting inward on the drum core which is the inverse to what a pressure vessel sees. Most of this force is supported by the hoop strength of the drum core barrel. I need to make sure my design is strong enough.
My question: Will any of the FEA simulation apps handle this scenario?
My question: Will any of the FEA simulation apps handle this scenario?
0
Comments
From what I understand, you want to apply a pressure to the outer surface of a cylindrical drum? Can you provide a picture or share the model?
Linked[in]
https://cad.onshape.com/documents/dbc50e4c06a0011863e3b8ea/w/46eeef81efb2a937f3aeaadf/e/742a9e8c69b2b8db96fe8102
The construction will be TIG/MIG welded HSLA steel.
The winch drum is intended to hold as much as 10,000 feet of 3/16" diameter Amsteel Blue (UHMW-PE fiber rope) with as much as half that wound on at 2200 Lbs-F tension. This exerts an enormous constrictive force on the drum.
Linked[in]
Here is the scope of functions:
Perhaps a way to simplify it would be to make concentric bands around the flange, with the same thickness as the rope diameter, and applying deceasing values to the bands. The bands can be made easily in Onshape using the split feature, and parametrically tied to a #ropediam variable like this:
The force profile wouldn't be a smooth ellipse, but rather "stepped" if you know what I mean.
Linked[in]
I prepped the CAD in Onshape using a derived part, and direct modeling techniques, and taking advantage of symmetry. HERE is the model.
Then, in Simscale, I added a torque to the drum and concentric bands of decreasing pressure on the flange. I put in some random numbers. The mesh needs to be bumped up, but this is a solid working model I think. I hope it helps. Here is the link to the project: https://www.simscale.com/projects/fastwayjim/rope_drum/
Linked[in]
The radial pressure on the core can be as much as 13,789,514 Pa with the 1st rope layer exerting as much as 25% of that laterally against the flanges. The torque on the drum can be as much as 2,286 Nm applied to the drum through a "dog clutch" using the 8-hole pattern in the end flange. The rope is Dyneema (UHMW-PE fiber rope) with a 4.7mm diameter. When full the drum can hold as much as 3,000m of rope. Typically, only half the total rope will be wound on at high tension and the remainder at only about 100N. The maximum rope tension is 1,000 DaN limited by a weak-link in the rope. The radial force on the drum is calculated using the formula:
F=2T/Dd where T is the rope tension, D is the drum diameter and d is the rope diameter. The area of the drum surface is divided by the result of the formula times the number of wraps in each layer to get pressure.
If the rope is laid on the drum in parallel wraps, the lateral pressure can be much higher than that as later wraps will try to wedge down between earlier wraps shoving them sideways. The work-around uses an "X-Wind" pay-on technique where each layer is a wide helix with 50mm of distance radially between each subsequent wrap. This causes the wraps in each layer to cross those in the previous layer at about 3 degrees which prevents wedging and significantly reduces the lateral force on the flanges.
Again, thanks for your help
So much for the core, now I have to figure out how to use OnShape Slice to segment the flanges.
twitter: @ken_welch | web: www.altair.com/simsolid
Twitter: @onshapetricks & @babart1977
I'm not an expert on winch drums specifically, but a critical failure mode for hollow cylinders under external compression is often thin shell buckling, which can happen with stresses MUCH lower than the yield strength of the material. Have you considered this failure mode? You might want to do a buckling check in addition to your elastic stress check.
Second, cost is extremely affordable. SIMSOLID has a low monthly subscription plan, not unlike Onshape. Considering the time savings, it is the most cost effective analysis solution in the market.
Third, traditional FEA requires potentially different mesh strategies for each analysis. For example, I would not recommend the mesh as presented for buckling evaluation. SIMSOLID meshless solution is adaptive specific for each analysis performed.
Forth, SIMSOLID analysis is associative to any model update. The analysis definition needs only to be assigned once. Just change the geometry and rerun. SIMSOLID design studies makes it fast and simple to evaluate design change.
I really feel that time well spent is to evaluate the total analysis process and not only the compute platform.
twitter: @ken_welch | web: www.altair.com/simsolid
It's especially problematic when using Dyneema rope since it has a very low coefficient of friction so it tends to cinch up tight on the drum and a very high coefficient of thermal expansion so if it is left wound tightly on the drum it will shrink even tighter on cold nights. Good operating practice is to store the winch with the rope loosely wound onto the drum.