Welcome to the Onshape forum! Ask questions and join in the discussions about everything Onshape.
First time visiting? Here are some places to start:- Looking for a certain topic? Check out the categories filter or use Search (upper right).
- Need support? Ask a question to our Community Support category.
- Please submit support tickets for bugs but you can request improvements in the Product Feedback category.
- Be respectful, on topic and if you see a problem, Flag it.
If you would like to contact our Community Manager personally, feel free to send a private message or an email.
Transform by mate connector bloat
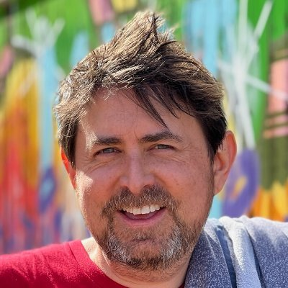
I build mostly machines in onshape so I end up using a lot of different parts more than once. Because of this a large chunk of my main part studio feature list is filled with derived parts of this pattern..
derived - name a
mate - name a
mate - name a
transform - name a
derived - name b
mate - name b
mate - name b
transform - name b
.
.
This is both tedious and creates a lot of bloat in the feature list. Is there a better way to go about this?
derived - name a
mate - name a
mate - name a
transform - name a
derived - name b
mate - name b
mate - name b
transform - name b
.
.
This is both tedious and creates a lot of bloat in the feature list. Is there a better way to go about this?
1
Best Answer
-
lana Onshape Employees Posts: 736
If base part studio has a mate connector attached to PartA, it will be present in the part studio deriving partA. Optional transformation in derived feature is a good idea. Please submit an improvement request.1
Answers
As for using an assembly context I am forcing myself to build within a main part studio and only use an assembly for visualizing moving parts. It has been a painful process since I am used to using an assembly for, well.. assembling. That said I am starting to become productive again and hopefully it will pay off in the future with better robustness in my models.
I'll go ahead an submit an improvement request for an optional transformation in derived feature.
https://forum.onshape.com/discussion/5317/multiple-transforms-in-one-feature-within-derived
What I am now wondering is what other things am I missing that are right in front of my face!
https://forum.onshape.com/discussion/5255/derive-to-grouping-in-part-studios-improvement-request
Cheers, Owen S.
HWM-Water Ltd
Twitter: @onshapetricks & @babart1977
For my workflow, I don't try to repeat/instance parts in the part studio only drop parts with the derive for reference and I add the original in the assembly mainly because of BOM/Product/Assembly structure which is limited by the part studio lack of instancing. I use the part studio as the place for modelling and linking of parts, therefore my part studio will contain parts which make sense to be linked together but may be grouped completely different to the final assembly structure of the manufactured product.
Twitter: @onshapetricks & @babart1977
Twitter: @onshapetricks & @babart1977