Welcome to the Onshape forum! Ask questions and join in the discussions about everything Onshape.
First time visiting? Here are some places to start:- Looking for a certain topic? Check out the categories filter or use Search (upper right).
- Need support? Ask a question to our Community Support category.
- Please submit support tickets for bugs but you can request improvements in the Product Feedback category.
- Be respectful, on topic and if you see a problem, Flag it.
If you would like to contact our Community Manager personally, feel free to send a private message or an email.
How to model a hose using Onshape?
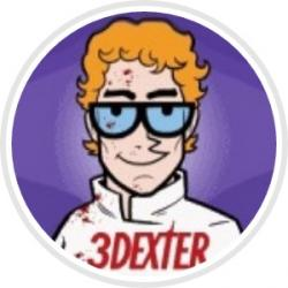
How to model a simple hose using Onshape?
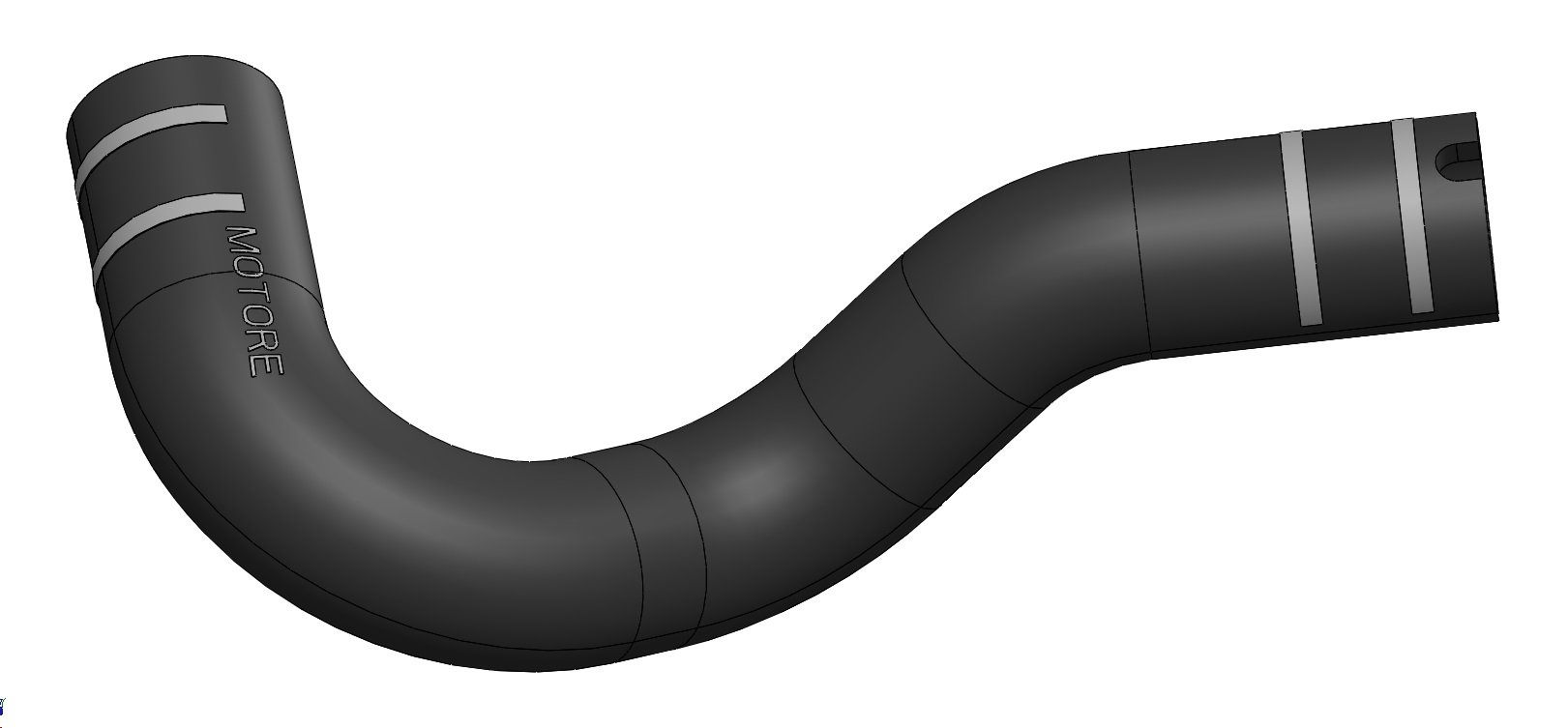
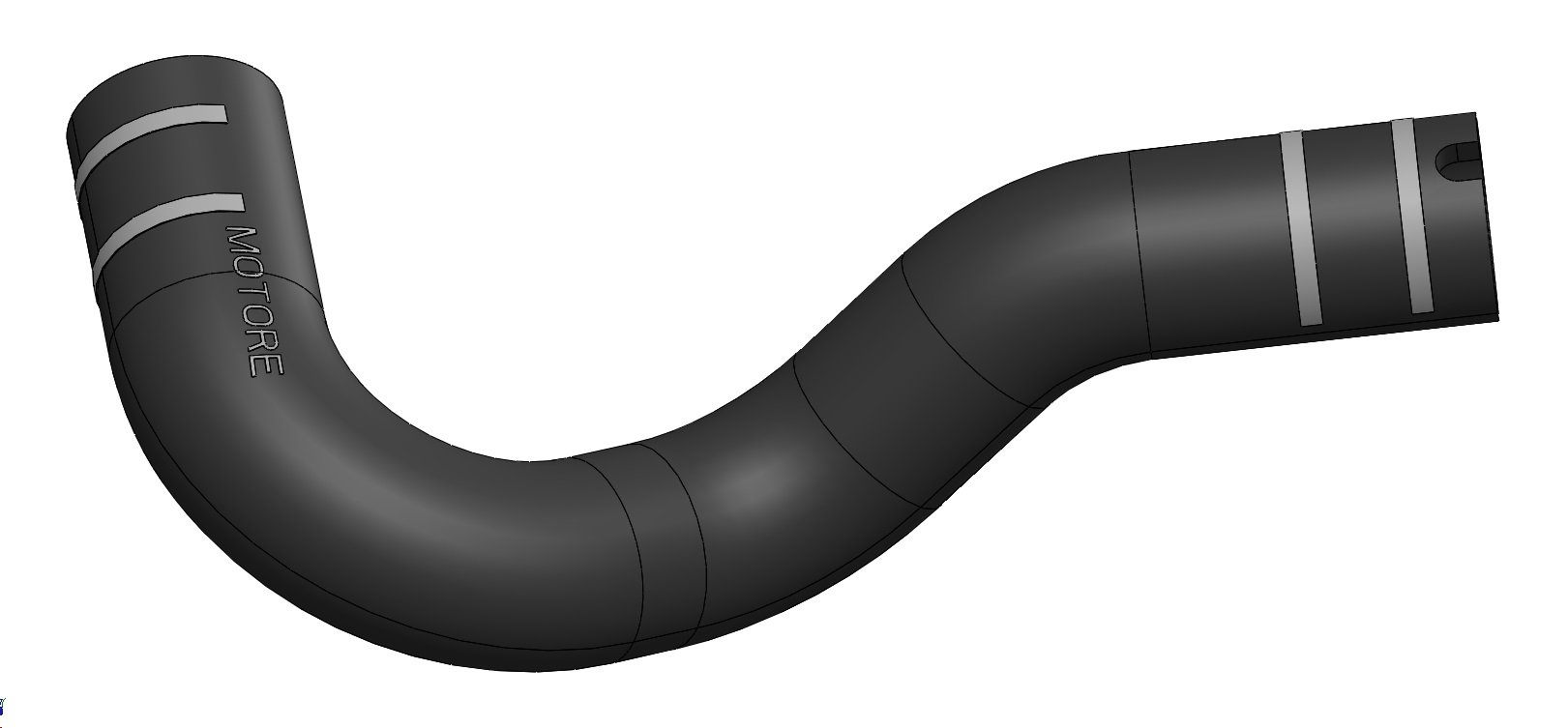
0
Comments
Looking at it, it seems you could fully define the centerline with three workplanes and three sketches. Finally you would perform a sweep with a sketch that defines the cross section.
Good luck!
One problem is the 3D sketch and another is escription (MOTORE) in the hose!
One ugly way to model a hose would be extruding the straight portion, then revolutioning the radius and follow then with the next straigth, radius... notch marks are common extrusions, the same for the timming marks. The only problem by now would be the texts.
Regards!
But it is an alternative to 3D sketch sergio_pluchinsky.
+1 for text in the 2d sketcher
+1 for import of vectors to sketcher (could also get your text in this way)
I know these are all on the Onshape radar. Hopefully we see these tools soon.
Twitter: @onshapetricks & @babart1977
+1 for text and import of vector text.
Did the attached (in Onshape) to see ;-)
Shared at;
https://cad.onshape.com/documents/49f4848957394d45bee990de/w/ab64fca6d874416992627b3f/e/c8da2bf0c06c442281ccf9a9
next look at another main plane and draw out the profile and extrude cut it out of the block
Make a plane using the curve-point option at the end of the curve/path
Draw the profile on the newly made plane at the end point of the path
Next sweep the profile on the path as a new solid
Delete the first body defining the path and voila! This took about the same time it would have to define the 3D sketch...
All done with 3 Sketches, 2 extrudes, one plane and one sweep feature
Here is the model
https://cad.onshape.com/documents/a4cba537bda44adf8f377bd3/w/eb41423d8c0949569ae03b3d/e/K17Ex85HZWzDs393swcpRV3j
Second tab is another one done more angular like. Things to note on the second one are:
1. Use of 'Intersect' on the second extrude to reduce features
2. When defining the path you are not stuck to one line you can select multiple sections like the initial lead out, then the following fillet, the next lead out and the next compound fillet.... etc...
Have a look at how I did it and right click on a feature and 'rollback' to see the steps. Pro-tip, the roll back feature and dragging the roll back line up and down are a handy thing to play with in figuring out how others model and diagnostics on what may have gone wrong in models.
All of this done on a cheapie Chromebook, on crappy wifi. So to be up and running in the CAD world is now cheap like borscht! Love it!
LearnOnshape facebook group
If I have your email I can share the file so we can markup and see each others edits as well FYI
LearnOnshape facebook group
Regards
I have found, however, that I cannot sweep a closed 3d path. Once I add the last leg, OnShape seems to get confused on how to mate the beginning and end. Closed paths work great with 2D path sweeps.
In my case there are 2 equal curves that meet with a twist... Although my swept surface is perfectly perpendicular to one of the curves, it doesn't seem well to mate well to the other, although all end points are concurrent.