Welcome to the Onshape forum! Ask questions and join in the discussions about everything Onshape.
First time visiting? Here are some places to start:- Looking for a certain topic? Check out the categories filter or use Search (upper right).
- Need support? Ask a question to our Community Support category.
- Please submit support tickets for bugs but you can request improvements in the Product Feedback category.
- Be respectful, on topic and if you see a problem, Flag it.
If you would like to contact our Community Manager personally, feel free to send a private message or an email.
Move face
Hi,
The bowl in the image is the "net size". To manufacture the bowl I want to add 20 mm to the top.
I have used the move face command in the past and it works very well. On the bowl shape I am not having much success moving the face past 3 mm. I looked for additional options in the "create selection" box. Am I better of using another method like a sweep? Any advise would be appreciated.
Here is a link to the model: https://cad.onshape.com/documents/4a5ef8feb955c98c3389ac76/w/dbf28cbb1558296eaf92f3e8/e/a403f0485d0e93d549be451e
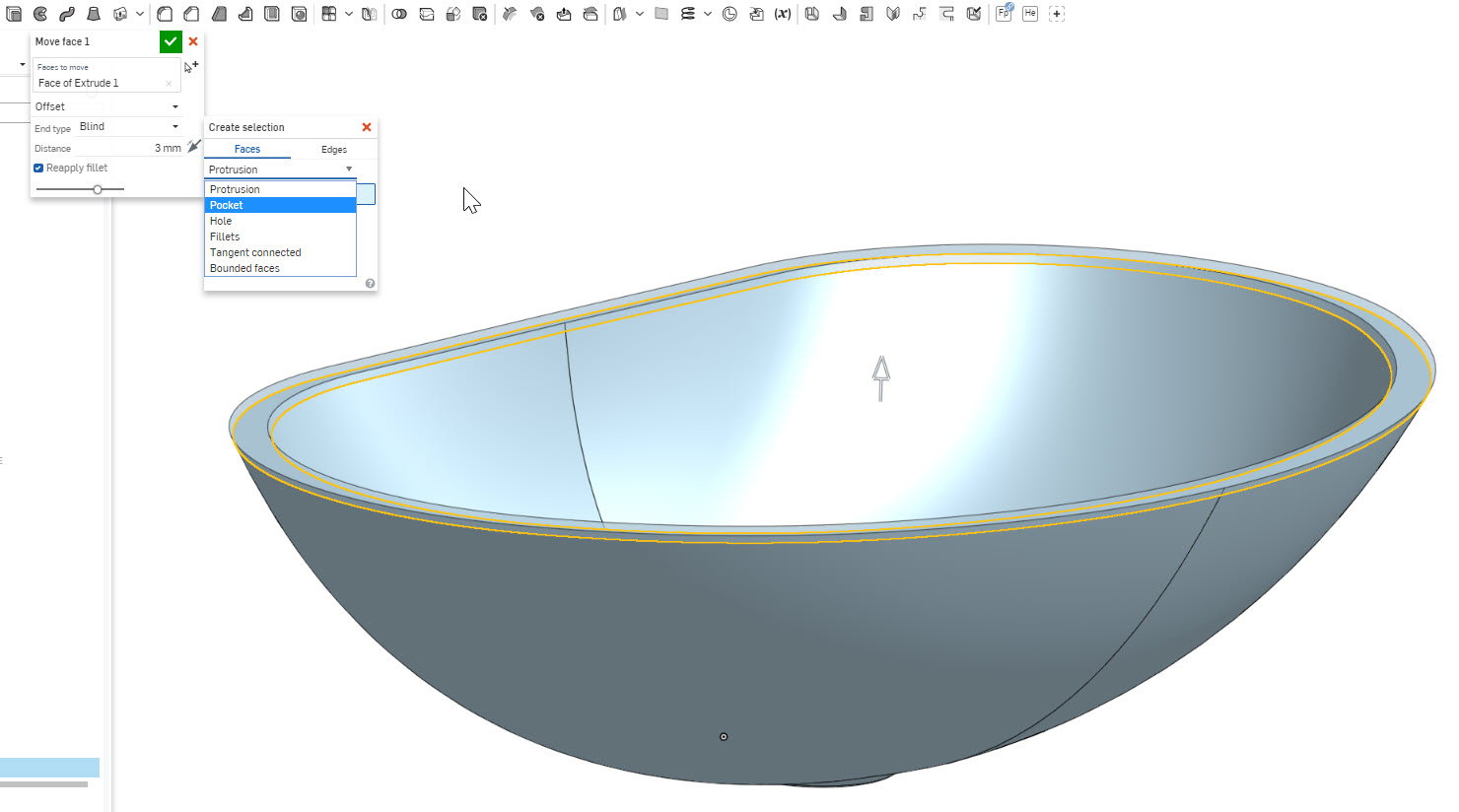
Thanks
The bowl in the image is the "net size". To manufacture the bowl I want to add 20 mm to the top.
I have used the move face command in the past and it works very well. On the bowl shape I am not having much success moving the face past 3 mm. I looked for additional options in the "create selection" box. Am I better of using another method like a sweep? Any advise would be appreciated.
Here is a link to the model: https://cad.onshape.com/documents/4a5ef8feb955c98c3389ac76/w/dbf28cbb1558296eaf92f3e8/e/a403f0485d0e93d549be451e
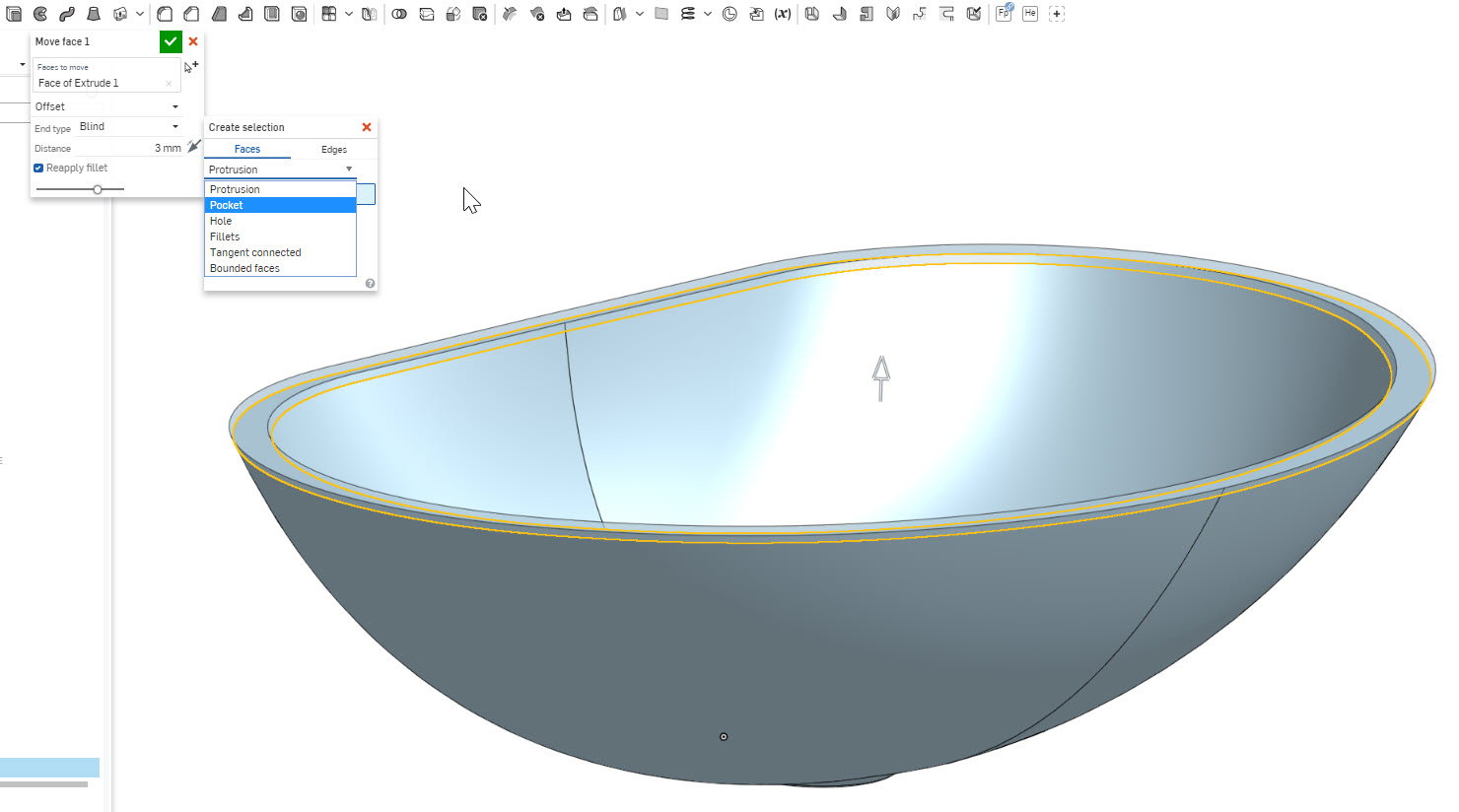
Thanks
Tagged:
0
Comments
IR for AS/NZS 1100
Your loft is a 2 sided surface with 2 poles (0 length edges):
These don't play nicely in subsequent operations.
Your original part used a lot of patches and 4 sided surfaces-groovy & ugly:
Many patches is actually better. These surface patches behave nicely although they might not look that good.
Notice that your concatenated edges are carrying through to the surface definition and the reason I wrote the fit spline, I'd clean'm up:
I suspect this is your error, these edges are connected with a zero length edge:
So what to do?
There's a reason shapes are made from many patches. Add a few more patches. Above, I divided your surface in half and paid attention to where the pole will be. It's at the bottom. You can see the flow lines rotating about the bottom vertex. This leaves the top edge you want to extend clean. This surface is 3 sided with one pole at the bottom.
Me, I'd still clean this up and get your lofts defined as 4 sided surface patches. To cap your sink off, I'd use a fill which can handle non-poled surfaces best. I could build a parametric model of a sink that would behave, look great, be robust and take over the world.
Don't get me wrong, you're doing great and I like your definitions. You're not that far off from having a robust model. As always, build the inside or outside first, then thicken to make a solid. This is already your basic construct and you're on the right track. Just keep going.
It's not even 7am and I feel like I'm making an enemy. Try the 3 sided approach, I think you'll succeed.
Maybe there's an issue when moving the face up and needing to create entirely new geometry whereas moving the face down is eliminating geometry that's already been created? A bit above my pay grade me thinks....
https://cad.onshape.com/documents/eacfb994138219d594ecc367/w/5307423e6fdeec73a5cbdebc/e/8d33f91de6ada4e513e4d7cf
Surfacing is a mystery for most people and it's not talked about openly in public. Most my information about surface constructs comes from the 1980's when working with IGES translators. @mahir seems to have a more modern perspective on the subject as my understanding may be dated.
@larry_hawes extending a surface & shortening a surface are 2 different things. Most the time extending a surface doesn't work the way you want and you end up adding a patch like Mahir did in his model.
Basic Surfacing
I'm not sure if we should be talking about this openly in public but here it goes.
A surface has 4 sides:
So think of it this way, take this curve (u):
And pull it along this curve (v):
This gives you area:
This is the same thing, a curve (u) along curve (v) makes area:
Now to complicate things, surfaces can be trimmed. By definition a trimmed surface consists of the surface and boundary curves. CAD chooses not to show the shading inside the boundaries and it looks like a hole to us. This was our most sophisticated CAD entity in use in the 1980's and it's still true today.
In the past I used a trimmed surface for my company logo:
So how do you create a hole in a plane? Trimmed surfaces are used everywhere.
@larry_hawes to shorten a surface they typically use a trim. To make it longer they have to re-evaluate the equations and try to stretch the surface using the definitions that defined it. It's not a robust process. Trimming will always work.
Now for the complicated stuff.
I have a surface and I have a boundary:
Make a trimmed surface:
Ok, now what?
A lesson in replicating complex shapes.
Most people would try and loft this shape by picking it's edges and will never succeed:
When you're dealing with complex shapes, define the under lying surface 1st and get it right:
Next, work on the boundaries:
When you see a shape, think about the surface definitions and then the edges. Don't think you'll be able to construct the surface using the edges that you see.
Sorry for the long dissertation on surfaces, probably puts most people to sleep and is the reason it's not talked about openly in public.
Then, once you have a solid (either by thickening or enclosing the surface) you can use more surfaces or other operations to create the final shape you're after. This is because, in my experience, the "edges" of thickened features often behave in ways you don't expect (because the tangency and/or curvature of your surface is tough to control near the edges sometimes).
The next issue I see in the model is selection of edges for the loft. To create a continuous surface across your "right" plane, you need the surface to be normal to that plane. See the selections and boundary conditions below:
There are 3 Profiles (1, 2, 3), and the Start Profile condition (at 1) and End Profile condition (at 3) are set to "Normal to Profile". This means that when the surface is mirrored across the Right plane, you will have continuity across that boundary. For any symmetrical model, this type of continuity consideration at the plane of symmetry is important to consider.
You can see that the mirrored surface is nice and smooth across the mirror plane:
You can also see that with this method of Loft profile & guide selection (with the curvature and edge conditions in good shape) that your original Move Face command works just fine:
Another way to approach this type of part, using a Shell feature instead of Thicken (I've found that Shell features are often more robust for many models where a constant wall thickness is desired) is to enclose the Surfaces to create a solid, then use a Shell to create your 12mm thickness:
Here, the lofted surface and two planes are used to create a solid with clean boundary conditions. Then you can use a shell feature to create your wall. Once you have a solid like this, it's easy to add rims and flanges...and the shell does a nice job of creating the thickness across the rim and fillets:
There are many ways to approach these types of models, but my main workflow considerations are:
- Extend surfaces etc with challenging boundary conditions PAST your final model shape, and use secondary trimming / boolean operations to create your final shape
- Consider surface continuity at boundaries (like planes of symmetry)
- Make sure your constraints are set up to give you the most flexibility for changing dimensions etc, and use basic references whereever possible (planes & sketches rather than model faces, edges & vertices).
You can make a copy of my version of the model here: https://cad.onshape.com/documents/966509c2dd3a9487391a9f0c/w/9f635046929ae2d676bb99ef/e/a0603d6aa844b05951c0549aGood luck!
Romeo
No problem!
Romeo
Here's an extended surface:
Here's a radiated surface:
What's important to remember is that radiated, loft, ruled and sweep as well as many other named surfaces are only referring to the method used to create these surfaces. Once generated, it is a surface. There's only one surface definition. All these names are referring to how the surface was created.
It's the same with a 3 point arc, tangent arc and centered arc, these all produce arcs. They are all arcs even though they have many ways to create them.
Surfaces are no different. There are many ways to create a surface, but what you always end up with is a surface.
Here's a robust surface for Joe's sink which will behave if driven from a configuration. I want this so I can drive the design from my/anyone's website allowing people the ability to order special configurations for a product. Onshape is ushering in a new way to buy stuff off the web, it's what I'm finding exciting and one of the main reason's I find Joe's sink problem interesting.
Creating a Robust Surface
Here's my sink:
The sound in my previous video (above) was set too low, here's a recompiled version that you can hear: last video with better sound
After trying many different surface techniques, I picked the fill surface to generate the prime surface, I picked this surface method because it produced the most robust surface allowing change.
Fill surface definition:
- It's a clean surface, notice the iso grids flow nicely.
- I used @romeo_graham392 tangencial technique for matching the mirrored edge.
- I added extra surfaces in order to work with the fill surface conditions since it doesn't work with sketch conditions. These extra surface definitions allowed me the controls to use the surface fill command.
- I cleaned up all the edge definitions and should probably write up curve definitions for robust surface modeling.
One thing that's different when working with surfaces, it's different from solid modeling, is that you'll build surfaces to define other surfaces. I'm controlling not only the location of the edge, but also the direction leaving the edge defining a better surface. This is a point vector method that runs continuously along my positional edge giving me more control when creating a surface.Robustness Check
If surface extensions is a measure of robustness, then this surface is good.
Surface being extended:
My new curve definitions based on Joe's original curves, they're close, but I made some minor tweaks. Keep in mind that I modeled the inside of the sink and my curves are defining the sink's inside. The shown sketches below are Joe's sketches imposed on my geometry.
Top view of old/new curves:
Front view of old/new curves:
Side view of old/new curves:
Ok, so now that it's built, let's have some fun.
Configurations
Make a deeper sink:
Make a smaller & taller sink:
Change the location of the drain:
So the ultimate situation is to expose your designs to your customers via your website. My ultimate goal is to drive orders from a website and offer custom products to my customers.
Configurations available from any website:
If you have a product and this capability interests you, drop my a line and let's talk. I'm currently building up a server to handle configurations and I want to make it work with any website.
There's a good example of these 2 styles and I want to illustrate the 2 methods highlighting the simplicity of surface modeling to create bitch'n geometry. Let's depart from the world of solid modeling for only a second and let me expose you to something new.
The Inner Sink Surface
The sink was created from the inside perspective with my last defining transition surface highlighted:
Solid Modeling
Now most people at this point would thicken the surface to form a solid:
You'll notice that the cross section thickness is constant, boring, possibly not correct, weak and totally not necessary.
Cross section of surface thicken with constant thickness:
Surface Modeling
If I can model the inside, then I should be able to model the outside. Let's change it up.
Offset surface 2 is 2mm (yellow) & Offset surface 3 (cyan) is 4mm allowing more material at the drain:
I create the outer drain transition & cap off top/bottom gaps:
But os still thinks it's a surface. So I enclose the water tight B-rep:
Geometrically, there's not much difference between the surface manifold/solid manifold and it's just a state of being. Going solids allows you to now use solid modeling commands on your manifold.
Cross section of surfaces solidified with enclose:
I can control varying wall thicknesses very easily staying in a surface model vs. switching to a solid model at the 1st cross roads. Most my designs will eventually end up as solids. It's just that, for me, I ride the surfacing wave a little longer than most.
At this point I'd run an analysis using SimSolid and optimize the design in making it the lightest, strongest and the best part possible.
Nicely done. Surfacing gives so many control options, and is generally very robust.
I agree totally with your surfacing assessment.