Welcome to the Onshape forum! Ask questions and join in the discussions about everything Onshape.
First time visiting? Here are some places to start:- Looking for a certain topic? Check out the categories filter or use Search (upper right).
- Need support? Ask a question to our Community Support category.
- Please submit support tickets for bugs but you can request improvements in the Product Feedback category.
- Be respectful, on topic and if you see a problem, Flag it.
If you would like to contact our Community Manager personally, feel free to send a private message or an email.
Pimp my flip phone - critique
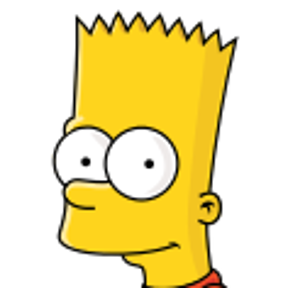
Hi Onshapers
This is a bit off the wall, I'm guessing you don't get many silly topics like this here - sorry if it's pushing the limits of etiquette. As silly as it seems sometimes the best way to learn is to attempt something and then present it to someone more experienced and let them pick it pieces to see where you could have done something better. So this is for the most part a novice model in need of expert critique.
Background story
My boy - 9YO (awesome kid) came home from school with an A4 sheet of paper folded up into the shape of a flip phone. He opens it up and it has all the features of a retro flip phone drawn on the inside, I didn't think much of it first but he's kept it for 2 weeks and it's become his fave toy. Every time he picks it up he tells me about some new feature or capability the phone has, it really gets his imagination going and he just loves it.
So to capture the moment (for him and myself) I thought I'd model something to similar dimensions that we can 3D print and give him something a bit more substantial than a folded piece of paper. I've made a few basic mistakes with the drawing and could have spaced things better or used the pattern tool to equally space the buttons. I did learn a bit in the process of the design but rather than guessing my way through it I thought I'd ask and see if anyone has any suggestions I haven't thought of.
So if anyone can spot any stupid mistakes I've made or show me how I could have employed a more efficient work flow feel free to show me how you'd do it. Feel free to make any suggestions or improvements and point out any mistakes. I have thick skin so be brutal
Tagged:
0
Comments
How thick should the gap be? Welcome to the world of manufacturing tolerances. You stack them all up, cross your fingers, pick a number, then pay half $million to tool up.
Since it's printed, I'd add bumps on the ends to retain the hinge pin and leaving the hinge plastic stress free after pin insertion.
Now we were molding with polycarbonate which has no resistance to press fit stress. In a couple of weeks the hinges cracked often. With FEA the hinge design was proven to be functionally good from a users perspective but the press fit sent the stress through the roof. Gluing wasn't an option, who wants to glue in production?
So, I'd print a bump on the ends (if your printer has the resolution) and then press the pin past the bumps. The plastic will become stressed and then relax once the pin is in it's place. The bumps will keep the pin from falling out and will allow you to create a kids phone without choking hazards.
Of coarse most printed materials are doughy and a press fit might work for your pin. But if you need to make 1,000's, you may want to figure out a good way to keep that pin in place.
Your phone was a nice 1st attempt. watch out i-phone.