Welcome to the Onshape forum! Ask questions and join in the discussions about everything Onshape.
First time visiting? Here are some places to start:- Looking for a certain topic? Check out the categories filter or use Search (upper right).
- Need support? Ask a question to our Community Support category.
- Please submit support tickets for bugs but you can request improvements in the Product Feedback category.
- Be respectful, on topic and if you see a problem, Flag it.
If you would like to contact our Community Manager personally, feel free to send a private message or an email.
Assembly: Why do Suppressed Parts Error Associated Mates?
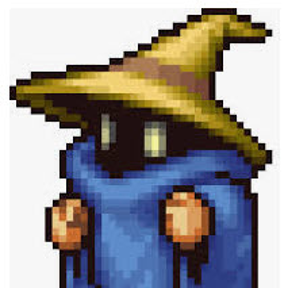
When Parts are suppressed in an assembly the mates corresponding to the parts shouldn't error out in my opinion; they're still valid when the Parts aren't suppressed right? They should be valid with simply some visual indicator that they're those mates are valid, but the Part(s) are suppressed.
¯\_(ツ)_/¯
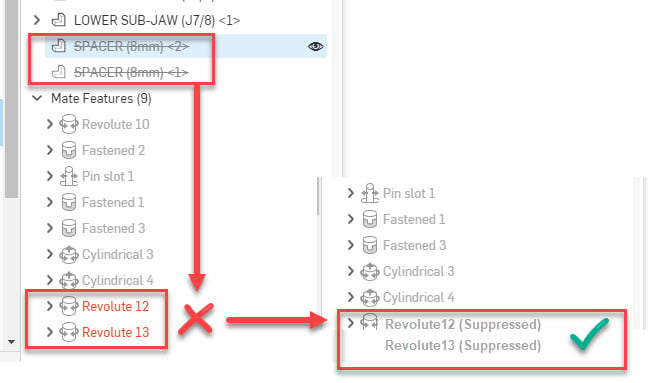
6
Comments
How do you feel about related mates being deleted when a part is deleted? I find some time I first suppress a part to make the mates fail, relink mates to a new part, then delete the original part.
Twitter: @onshapetricks & @babart1977
@brucebartlett I may have parts suppressed temporarily during the design and they may still very well be valid later and I don't want errors showing up in the List as it may interfere later interrogating other "real" errors of newly added mates etc... I would think this will also correspond to working with Assembly Configurations when they arrive.
If parts are deleted then I think the corresponding mates should be deleted as well. The redefinition prior to deleting to other components is a nice workaround. Either way, if we had a visual for which mates are simply suppressed should still work in your case.
Twitter: @onshapetricks & @babart1977
red angry mates tell me there is a problem that needs to be fixed. In these cases, its not a problem. Its just that the parts are suppressed.
This is something we can look into, but will likely be prioritized behind other work that we are doing in Assemblies. Essentially, the current behavior isn't great but it is technically right as the individual mates now fail to solve when including a suppressed instance.
@jakeramsley Thanks for the honest response; I still don't like the exiting behavior. I would think this work would be part of the "Configured Assemblies" spec since components will invariably required the need to be suppressed and suppressed without error; unless you guess have something else planned of course!
Another "error" behavior that unnerving is with the system solving for things that haven't happened yet; and take it too far. When adding mates and selecting the newer green check applying it from the toolbar popup the next mate is already overdefined. This makes me think for a second that the previous mate overdefined the assembly almost every time only to quickly glance again and be reassured it's just trying to auto-solve.... for NOTHING even selected...for the next potential mate. this needs to be changed too in my opinion with the next mate waiting for input not being shown as an error.
Worse yet, it even starts in an error mode to the user which I can get past. But this isn't intuitive.
I think red would be ok in this case. (OR yellow)
HWM-Water Ltd
I find it unnecessary difficult to locate a part or assemblies corresponding mate. It would be nice to be able to right click a part/assembly and press "edit mate" (if any mate has been created). If there are several mates defining this part/asm I think those should belong together so you can edit all at once when you click "edit mate(s)". Today you can press "show mate". After that you need to locate it/them either in the graphics window or the model tree, right click again and find the edit option. Changing a parts position can take some time and I think that's a flaw because you do it all the time when you work in assemblies. Mates should rather be organized as a sub member of the part/assembly and not in a separate - and quickly very long - list which gives no overview as it is today. It should not be necessary to rename the mates to keep track of them. Renaming takes time.
Mating an assembly: Onshape encourages you to choose one part of the assembly and use this to define the mate. If you some time later want to change the assemblies position you have to be a detective to sort out which part was used for this mate. It would have been better if the mate was associated with the assembly itself even tough you use one parts geometry to place it, so that you later can right click the assembly name in the model tree and press "edit mate" directly. Save the detective search work.
Avoid using geometry for mates: In my old CAD system I have found it best to use a more static item (origin/plane/axis) for mates whenever possible/feasible to avoid making mates that fail as parts are changed. Especially I find it good practice to do this when placing sub-assemblies. In Onshape you have to first make a mate connector in the origin in each part and assembly to be able to do this, and this takes some time and you end up with tons of mate connectors in the origin of your assembly. And they add up as you add subassemblies mated the same way. Maybe a default mate connector in all parts/assemblies origin would be a good idea but I am not sure.
One area where Onshape has a superior (in my opinion) mating systems is that you Never use geometry for mates, you're always using Mate Connectors. You can more easily control Design Intent and downstream assembling by adding the Mate Connectors in the Part Studio. These MCs will also be available in the assembly, and they're easier to find because they appear in the Instance List in the dropdown for each Instance.
Another tip that makes the "Show Mates" feature more useful: use the keyboard shortcut to Hide All the Mates first (J). Then, when you "show Mates", it will be the only one that shows.
Lastly - I think I agree with the original post too: When I suppress an instance, I want the Mates to be suppressed too. Now that we have configurable assemblies, this is a common (and useful) workflow. Having all those hanging errors is a bummer when you are changing Configurations, because it will prevent Release of the Assembly.
you have to add the mates to the configuration suppression also.
The point here is this should just be automatic upon suppression of one of the mated parts.
Unfortunately, show mates does not work with sub assemblies, so you have to be a detective and find which part is the mate owner.
All very tedious and unnecessary in this otherwise easy to use software. It is as if Onshape is still on mates version 1.0 and needs to finish what they have started
mate's only support two mate connectors. so if one or both of the parts are suppressed. then the mate connector is un-used.