Welcome to the Onshape forum! Ask questions and join in the discussions about everything Onshape.
First time visiting? Here are some places to start:- Looking for a certain topic? Check out the categories filter or use Search (upper right).
- Need support? Ask a question to our Community Support category.
- Please submit support tickets for bugs but you can request improvements in the Product Feedback category.
- Be respectful, on topic and if you see a problem, Flag it.
If you would like to contact our Community Manager personally, feel free to send a private message or an email.
Designing for OS performance.
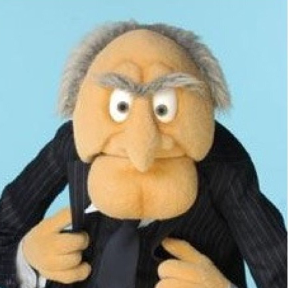
Hi folks.
This might be a case of overthinking things but as CAD models get more complex performance takes a hit. Better hardware helps of course but should we as designers be using any best practice methods to help Onshape out?
For example there are many ways to design the same part.
Example 1, a plate with 100 holes in it.
(Method 1) Sketch with circles in it, extruded in one step.
(Method 2) Plate with many sketch points, that uses the hole tool to make 100 holes.
(Method 3) Plate with one point, one hole tool use and then the additional holes set up as a feature pattern.
Example 2, a solid with a fillet.
(Method 1) Sketch with radiused corners that's extruded.
(Method 2) Plain sketch with fillet feature after extrude.
yada-yada.
Does it make sense to design with a couple of brain cells set aside to try to optomise the model for efficient regeneration, or does it make very little difference in the grand scheme of things?
Cheers,
Owen S,
This might be a case of overthinking things but as CAD models get more complex performance takes a hit. Better hardware helps of course but should we as designers be using any best practice methods to help Onshape out?
For example there are many ways to design the same part.
Example 1, a plate with 100 holes in it.
(Method 1) Sketch with circles in it, extruded in one step.
(Method 2) Plate with many sketch points, that uses the hole tool to make 100 holes.
(Method 3) Plate with one point, one hole tool use and then the additional holes set up as a feature pattern.
Example 2, a solid with a fillet.
(Method 1) Sketch with radiused corners that's extruded.
(Method 2) Plain sketch with fillet feature after extrude.
yada-yada.
Does it make sense to design with a couple of brain cells set aside to try to optomise the model for efficient regeneration, or does it make very little difference in the grand scheme of things?
Cheers,
Owen S,
Business Systems and Configuration Controller
HWM-Water Ltd
HWM-Water Ltd
1
Comments
Onshape, Inc.
It's 2017, we can do modeling with our cell phones and send email from wrist watch - Onshape devs, keep up the good work and give us cad that optimizes performance even though I would make 1000 circles into sketch (that doesn't sound very complex task for modern computers). Don't give up, you will find a way to bring high performance for ordinary people who think human like - if I can draw this to paper, it should be easy for computer.
Or if that's too much, then Onshape could suggest changes if it finds performance hit in my design?
In the meantime, it wouldn't bother to have 'best practices' guide to select the best approach to most common tasks like the one @owen_sparks mentioned.
I think it's important to have strategies for managing data:
-hide removes things from the display list
-suppress removes it from regeneration & display list
We'll always create more than a computer can handle.
Making data go away and then come back is the key.
A panel with 1000 holes, I'd suppress that pattern when not printing out a picture. I'd sketch a rectangle indicating the hole boundaries when pattern is suppressed. A perf panel can kill your project.
I like my projects to be snappy and responsive which is not automatic by any means.
So, overall I think there should be an approach of optimization which will take care of both easier editing and good performance.
@timrice
Is there any chance we could have a few more examples of how we can be more efficient in our choice of methods?
I love linked docs but was wary, thinking that long chains of links and derived parts might also hit performance. In my limited coding experience I was amazed at how small a percentage of the code actually does the work, and how much is spent updating the screen and generally making things pretty for the user.
@3dcad
Interesting idea about OS monitoring it's own performance and offering tips to the user as to how they might like to change their methodology.
@billy2
Great tip on making a substitute "simple" part to represent a more complicated one and then suppressing the complicated one when not needed. A method to link features to their parts would be useful here, so we only suppress features that don't link to the stuff we do want to show. I'd imagine with multi-part modelling from single sketches etc. this may be complicated as things stand?
Cheers,
Owen S.
HWM-Water Ltd
I have being thinking and testing this quite a bit and there are some surprising differances with onshape and other CAD systems.
While we do have to be careful about best practices on onshape they are definetly less important. I recently tried the generating lots of holes to see how onshape works and while it is faster to model a linear pattern in with one part using faces and then use union to remove they from your part than to do a linear pattern of remove extrudes features this is only for this one feature. After the feature is done both parts operate with the same performance as its only the graphical power you have to struggle with.
This has being true for many aspects that while they may slow the individual feature they don't slow down the whole document or part studio.
Things to be aware of though are (as of my latest knowledge) the document loads all the information when you load a document. If you can move sub-assembles or standard parts to other documets it will improve the loading alot.
Also loading expernal files saves a copy. Several of my documents have become >300Mb because of this, to combat this you can either delete the part and make a copy of the docunent to remove history (have seen >98% reductiob in file size) or when you start you can create a temp document that you load parts into and tidy them up in and thrn move them when you are happy.
Additionally mates can slow the model down if you chain them. Of you can link most of your mates to a couple of key parts and use offset to get correct position you can see a improvement in your documents.
Finally if you deal with large assembles, you can use the branching to create a high detail and low detail version of your parts and use linked documents to build up complex assembles with low detail and individual part drawings with full detail.
Have to say that with a bit of effort and lateral thinking you can improve the performance alot. Hope this helps.
Carl