Welcome to the Onshape forum! Ask questions and join in the discussions about everything Onshape.
First time visiting? Here are some places to start:- Looking for a certain topic? Check out the categories filter or use Search (upper right).
- Need support? Ask a question to our Community Support category.
- Please submit support tickets for bugs but you can request improvements in the Product Feedback category.
- Be respectful, on topic and if you see a problem, Flag it.
If you would like to contact our Community Manager personally, feel free to send a private message or an email.
Options
Mate Limits?
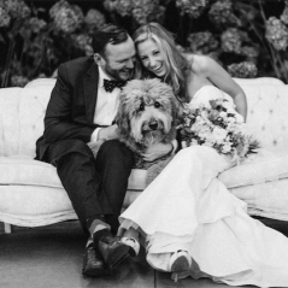
Are there currently mate limits? For example: using a slider mate, allow components to move to x location from face of part but not beyond?
Thanks
Thanks
0
Comments
UX/PD/Community Support
I am also interested in learning how limit would help our users in design tasks/workflow. I can see people dragging a part/parts to a limit position and measuring other parts etc or visually inspecting mechanism but I also want to learn other workflows.
In the attached picture, the yellow captured ring should only be allowed to translate from the faces of the blue end caps but not beyond. It would be nice to select the faces that are the stop-limits as opposed to dimensioning the limiting constraints.
I will pull together some more examples and post them here.
Mate limits are also a lower processing overhead alternative to using physics to constrain travels inherent to a mechanism, like a swinging lever coming against a stop block.
In both cases, it means the mechanism can quickly be taken to the applicable extremes of its range with a simple, fast mouse drag. At this point, it might be measured (as others have indicated) or it may be eyeballed for an interference check, or used to generate graphics or drawings, or evaluated for ergonomic excellence, or used as a visual guide for modelling or positioning further features, or adjacent machines / mechanisms.
- Cumulative mates so that a vertex mate can be added to a planar mate and as per below alignment of faces.
- Alignment so that parts can be positioned by aligned faces rather than mated faces.
- Two and three point mates so that an object can be positioned by a tool and target fixed first points and rotated to align by tool and target second and optional third points vectors or tool and target vertex points and successive tool and target edges.
Triad manipulation:While designing furniture, I would love to manually open drawer to it's max and close until front plate hits the frame. So I would need more than the example @coleman posted, because opening is limited by drawer slide limit and closing is limited to drawer front piece softening pads hitting to cabinet frame (slide can sometimes go a lot further, depends on the depth of the box).
Also opening door as hinge allows would be great, so I would actually see the whole movement and distances in different positions. This would need angular limits.
For me most of the limits would be in sub- or sub-sub-sub..assemblies in basic components like drawer slide or hinge.