Welcome to the Onshape forum! Ask questions and join in the discussions about everything Onshape.
First time visiting? Here are some places to start:- Looking for a certain topic? Check out the categories filter or use Search (upper right).
- Need support? Ask a question to our Community Support category.
- Please submit support tickets for bugs but you can request improvements in the Product Feedback category.
- Be respectful, on topic and if you see a problem, Flag it.
If you would like to contact our Community Manager personally, feel free to send a private message or an email.
"Group" function for assembly
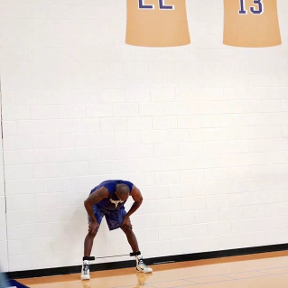
hi all,
I found a bug with the "group" function. here is my problem and suggestions.
Some parts created in part studio can be easily assembled by group function without any mate,
For me, I'd like to create all parts in one part studio then separate the parts to different assembly.
but sometimes, subassembly is needed for my model.
when I have an assembly consist of parts and subassembly(Assembly 3 in the illustration) , I need to put all the parts and the subassembly into a group to keep all the parts fixed,
so I dont need to mate the parts which already in the right position. Then assembly 3 will be insert in assembly 4 as another subassembly.
my problem is, if I change the mates in subassembly(Assembly 2 in the illustration), when I back to assembly 3, assembly 2 cannot be updated automatically unless broke group 1.
all I want is the assembly which already in a group can be updated automatically either!
best regards!
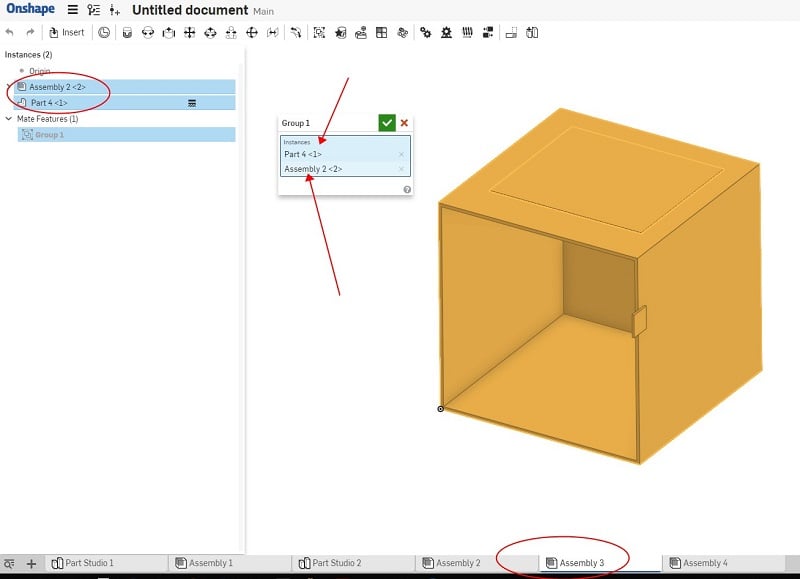
I found a bug with the "group" function. here is my problem and suggestions.
Some parts created in part studio can be easily assembled by group function without any mate,
For me, I'd like to create all parts in one part studio then separate the parts to different assembly.
but sometimes, subassembly is needed for my model.
when I have an assembly consist of parts and subassembly(Assembly 3 in the illustration) , I need to put all the parts and the subassembly into a group to keep all the parts fixed,
so I dont need to mate the parts which already in the right position. Then assembly 3 will be insert in assembly 4 as another subassembly.
my problem is, if I change the mates in subassembly(Assembly 2 in the illustration), when I back to assembly 3, assembly 2 cannot be updated automatically unless broke group 1.
all I want is the assembly which already in a group can be updated automatically either!
best regards!
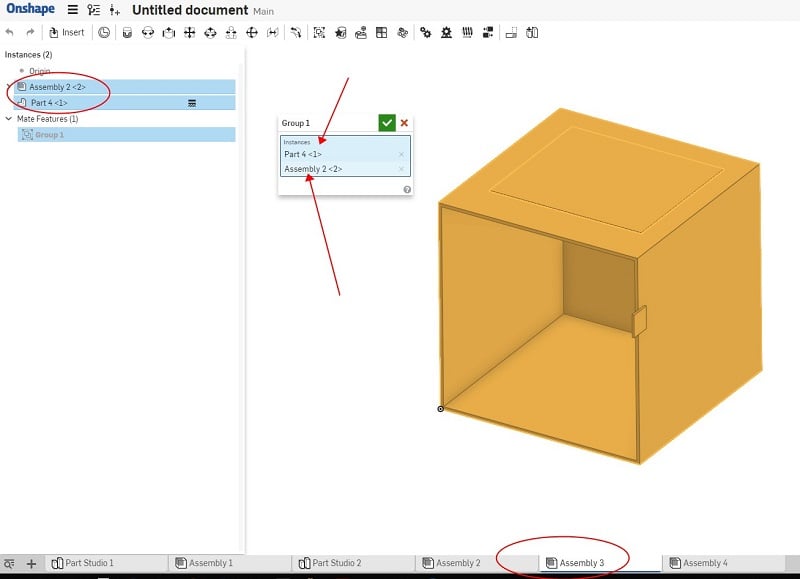
Tagged:
0
Comments
Having everything in one part studio is far from ideal. If you have small projects that only have a small hand full of parts I would say sure.
But you should really give assemblies a second look, they are much more powerful and faster than a part studio.
For example: I imported a project with a few hundred unique parts and flattened them into a single part studio. It took Onshape 5 minutes (+10 crashes with chrome) to load that studio.
I imported the same project without flattening it, and it loaded the main assembly in less than a minute (no crashes).
Having multiple studios feeding an assembly will scale up your performance exponentially. Not to mention "BOM" and "standard content" only exists in an assembly, or the fact than any minor change on the top of the part studio tree will need to regen/rebuild every part and feature below it, increasing your modeling type dramatically.
Even if the assembly only is connecting 2 or 3 parts (weldment/sub assembly) the benefits far outweigh the hassle of a couple broken mates.
In-fact with Onshape's mating system by mate connector, creating an assembly only takes 1/3 or less time than with traditional CAD systems.
Although I hope they implement better tools to reduce the need for re-inserting and re-mating broken part references, and more powerful patterns will be a major benefit (curve pattern, pattern driven component pattern, etc) further reducing the mate count and broken references on part studio regens by far.
If you are having trouble learning assemblies, I could help you if you want to find a time and work on assembly practice.
I'm going to assume most of your problems could be avoidable by a little mate theory. (Only "fix" ONE part per assembly, Only mate to geometry that is unlikely to change, If you need your part centered about a position you should create a mate connector in the part studio and use that to mate.. etc..) Seriously, hit me up, I'd be glad to help.
Movement be damned, assemblies are for everyone.
HWM-Water Ltd
Could it be broken into sub asseblies?
How many parts are in each part studio?
How many mates break on an assembly when you start over?
It appears you put all your parts into an assembly, then insert the assembly and mate it again.
Unless you are using this assembly elsewhere that you want it locked in position (static) then I could see this work around (only because we don't have assembly configs yet)
Also I see you have all your parts "fixed" in the G-Dual assembly, this really doesn't do anything as only one part will be fixed in a sub assembly (otherwise you wouldn't have any motion in A-Dual)
So only fix the "main component / The one all other parts move in relation to"
Then use mates as you did in A-Dual.
see the example here : https://cad.onshape.com/documents/10a06412808fb86acc0344f3/w/4c672ca8d11da336ed7fb60b/e/2252fd71c991f78a7336529d
Also you appear to be explicitly defining a mate connector within the part studio and assembly and mating to those.
This is fine if you have an off offset or something you want to always be mated to for a part (example: a part's center of mass, or a reference point a few inches away from the part)
Unless you find the geometry tends to get de-referenced often after updates in a part studio. You should consider saving yourself some time and stress by just using the mate command in the assembly and using the provided geometry of the part.
I just got an email saying you posted here again as I type. Give me another sec to pour into that
nevermind, didn't read...
Ok got it,
Sounds like you might be describing a need for assembly configurations, which Onshape is planning on (last I hear). And it is in high demand.
But I may not fully understand your problem.
If you need a configured part in an assembly, you should be able to insert it with that config.
When you attempt to use the sub assembly elsewhere you are limited to the pre-configured parts of that assembly.
(right?)
From here, you would be correct to create a duplicate assembly and change configurations of the parts.
If that's your problem, then you are doing the correct work around in my opinion.
If your derived part studio is small, I would go ahead and derive.
If you use incontext, it will require manual context update. So you still need to go back and update manually anyway, so may as well just configure the part studio instead.
assuming the hole quantity changes for larger parts you would still need to dig back to the part studioes and add to your point selections for hole command. So again may as well configure it.
Derive is nice, but can be slow.
Incontext is nice, but requires manual updates.
If you need to touch the final part anyway, it may not be worth the complexity of either for simple features in the long run.