Welcome to the Onshape forum! Ask questions and join in the discussions about everything Onshape.
First time visiting? Here are some places to start:- Looking for a certain topic? Check out the categories filter or use Search (upper right).
- Need support? Ask a question to our Community Support category.
- Please submit support tickets for bugs but you can request improvements in the Product Feedback category.
- Be respectful, on topic and if you see a problem, Flag it.
If you would like to contact our Community Manager personally, feel free to send a private message or an email.
Best Of
Re: Cabling, do we really need another featurescript?
I’m in desperate need of a good cabling solution, so hurry up! 😂
Faster Patterns
In the recent update (May 4th, 2018) we modified how Feature Patterns work to improve performance. We didn't shout about it in the forum post, but some of you discovered it anyway!
The new option is called "Apply per instance" which, by default, is off. When this option is selected, Feature Pattern works the way it always has, recalculating every instance. For a large pattern, a lot of feature recalculation is required which can cause unnecessary performance issues.
In most cases, the geometry created by each Feature Pattern instance is identical, so the correct choice for pattern type should really be Face Pattern. However, if your features are complex, that would require a LOT of face selection to get the correct patterned geometry. Most users therefore use Feature Pattern instead of Face Pattern for convenience.
With this in mind, we changed the default behaviour of Feature Pattern to be the same as Face Pattern. With "Apply per instance" set to off (the default), selecting features to pattern will, behind the scenes, select all the faces belonging to the selected features and create a Face Pattern. This provides the convenience of Feature Pattern selection with Face Pattern speed.
Sometimes the pattern preview will show red geometry. This indicates that the "behind the scenes" Face Pattern was not successful, probably due to some geometry condition. When this happens, check "Apply per instance" to get the regular Feature Pattern behaviour. It may be slower, but it is more robust and has the added benefit of recalculating feature references each time to create a pattern with varying geometry.
Anyway, this post is not about Feature Pattern, it's about Part Patterns and ways you can speed them up!
Part Patterns are great and I will always try to use them where possible. However, there is one performance hit that Part Patterns suffer from and that is the number of boolean operations that take place when the "Add" option is being used.
Take this model of a tire tread:
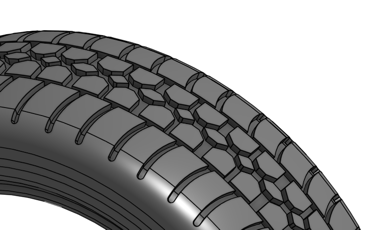
It may not be too complex, but there is a lot of repeated geometry. In my first model, I revolved the tire profile without the tread, then created a small section of the tread by splitting a surface multiple times (using the Split Face feature), then used the Thicken feature. The resultant tread was then patterned once so I could add extra geometry, then again to get the full tread around the tire, then boolean subtracted from the revolved tire. This works fine, but is VERY slow. Why? Because there are 14 boolean operations going on with progressively increasing complexity. Time for Part regeneration ~42 seconds!
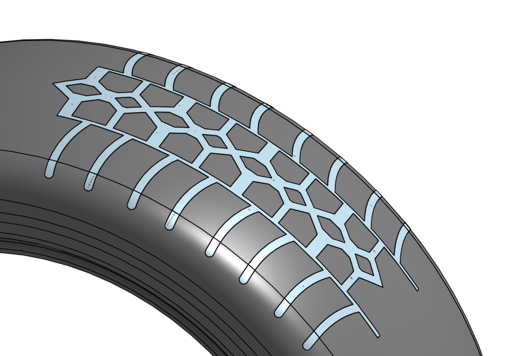
This is clearly not acceptable, so I created a second model, this time by creating a small section of the revolved tyre and creating the tread as before. This section was then patterned around. Much better performance at ~14s. However, there are still 28 boolean operations going on (though much simpler than the previous example).
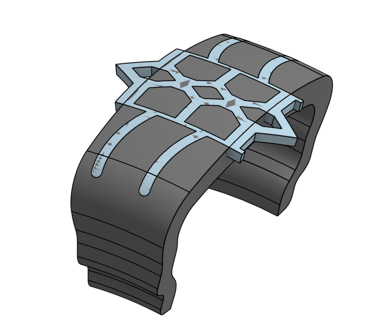
So the task is to reduce the number of booleans. Instead of patterning the tire section shown in the above image 27 times to get the full revolved profile, creating 2 pattern features reduces the number of booleans and therefore increases performance. So, in the last model, I patterned the above section 3 times, then created a second pattern with 9 instances (getting the total of 27 segments as before), only this time there are only 12 booleans occurring and regeneration time is now a paltry 6s!
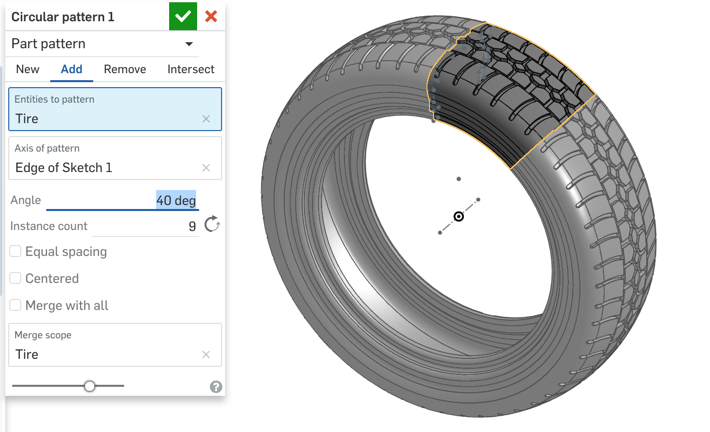
Anyway, the moral of the story is that, by reducing the number of boolean operations created by the Pattern feature, you can dramatically improve the performance of your parts.
Thought I'd pass this little nugget along - the proof of the pudding can be found here:
https://cad.onshape.com/documents/04c350f0aacd4ba7a39f96a0/w/b2c72b1da6a9c50dd95c6e2f/e/4aed42b5742a79a6aceefc53
The new option is called "Apply per instance" which, by default, is off. When this option is selected, Feature Pattern works the way it always has, recalculating every instance. For a large pattern, a lot of feature recalculation is required which can cause unnecessary performance issues.
In most cases, the geometry created by each Feature Pattern instance is identical, so the correct choice for pattern type should really be Face Pattern. However, if your features are complex, that would require a LOT of face selection to get the correct patterned geometry. Most users therefore use Feature Pattern instead of Face Pattern for convenience.
With this in mind, we changed the default behaviour of Feature Pattern to be the same as Face Pattern. With "Apply per instance" set to off (the default), selecting features to pattern will, behind the scenes, select all the faces belonging to the selected features and create a Face Pattern. This provides the convenience of Feature Pattern selection with Face Pattern speed.
Sometimes the pattern preview will show red geometry. This indicates that the "behind the scenes" Face Pattern was not successful, probably due to some geometry condition. When this happens, check "Apply per instance" to get the regular Feature Pattern behaviour. It may be slower, but it is more robust and has the added benefit of recalculating feature references each time to create a pattern with varying geometry.
Anyway, this post is not about Feature Pattern, it's about Part Patterns and ways you can speed them up!
Part Patterns are great and I will always try to use them where possible. However, there is one performance hit that Part Patterns suffer from and that is the number of boolean operations that take place when the "Add" option is being used.
Take this model of a tire tread:
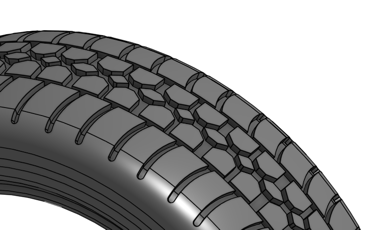
It may not be too complex, but there is a lot of repeated geometry. In my first model, I revolved the tire profile without the tread, then created a small section of the tread by splitting a surface multiple times (using the Split Face feature), then used the Thicken feature. The resultant tread was then patterned once so I could add extra geometry, then again to get the full tread around the tire, then boolean subtracted from the revolved tire. This works fine, but is VERY slow. Why? Because there are 14 boolean operations going on with progressively increasing complexity. Time for Part regeneration ~42 seconds!
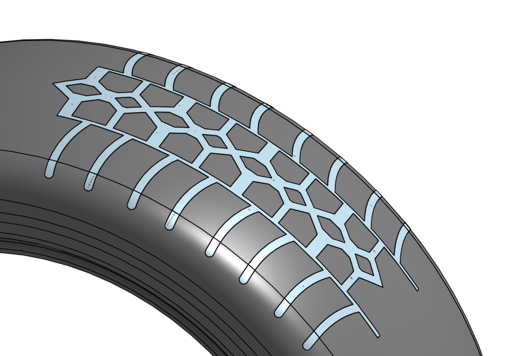
This is clearly not acceptable, so I created a second model, this time by creating a small section of the revolved tyre and creating the tread as before. This section was then patterned around. Much better performance at ~14s. However, there are still 28 boolean operations going on (though much simpler than the previous example).
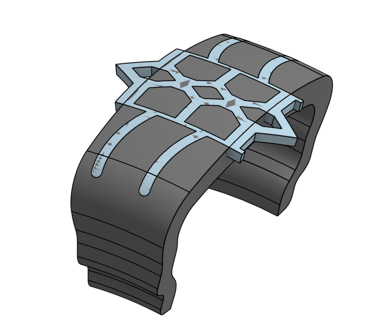
So the task is to reduce the number of booleans. Instead of patterning the tire section shown in the above image 27 times to get the full revolved profile, creating 2 pattern features reduces the number of booleans and therefore increases performance. So, in the last model, I patterned the above section 3 times, then created a second pattern with 9 instances (getting the total of 27 segments as before), only this time there are only 12 booleans occurring and regeneration time is now a paltry 6s!
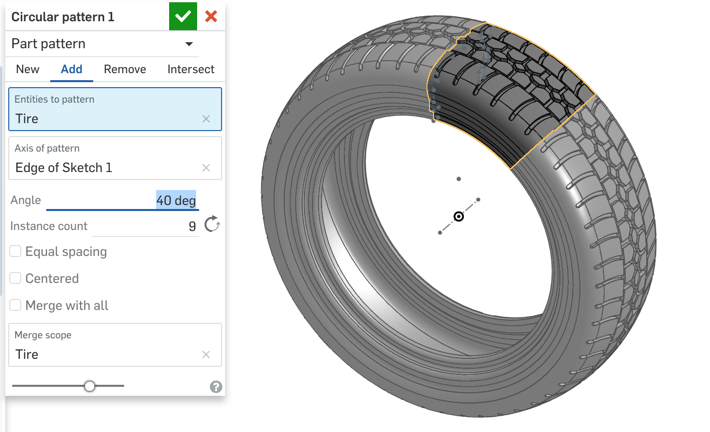
Anyway, the moral of the story is that, by reducing the number of boolean operations created by the Pattern feature, you can dramatically improve the performance of your parts.
Thought I'd pass this little nugget along - the proof of the pudding can be found here:
https://cad.onshape.com/documents/04c350f0aacd4ba7a39f96a0/w/b2c72b1da6a9c50dd95c6e2f/e/4aed42b5742a79a6aceefc53
Re: Evaluate pixels in an image import?
No, this is not possible today. It's not high on our priority list, since you generally don't want to be working with large amounts of non-CAD data in FS during part regeneration.
The alternative I would recommend is doing some preprocessing of the image to make a CSV file, and uploading that.
The alternative I would recommend is doing some preprocessing of the image to make a CSV file, and uploading that.
Re: Improvements to Onshape - July 31st 2020
Great Updates! Thanks again for the hard work and dedication, it really is awesome seamlessly getting these updates.
Mass Properties are moving in the right direction but I am looking forward to being able to roll mass and c of g symbol into drawings, hopefully, this is planned.
Editing properties for the tree is a nice update I will be making use of this.
Also love seeing some improvement to release management, the ability to auto propagate back to open nodes makes a lot of sense, it was a pain to having to create part numbers in multiple places. I'll set mine to all workspaces as I can't see myself releasing a different part number from a branch.
Mass Properties are moving in the right direction but I am looking forward to being able to roll mass and c of g symbol into drawings, hopefully, this is planned.
Editing properties for the tree is a nice update I will be making use of this.
Also love seeing some improvement to release management, the ability to auto propagate back to open nodes makes a lot of sense, it was a pain to having to create part numbers in multiple places. I'll set mine to all workspaces as I can't see myself releasing a different part number from a branch.
Re: Making changes to the array in the sketch.
This is a philosophical idea, with Pro/E, we always claimed features were more stable than sketches. Limit your sketches to 10 entities and replicate with features seemed to be more robust. That was the early 1990's; but I believe it's still true today even after 3 evolutions of CAD systems.
Your sketch scares me.
Your sketch scares me.
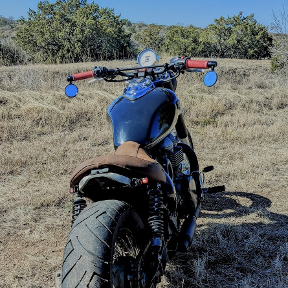
5
Onshape Education Enterprise FREE - COVID-19 Response
Hello Educators,
We understand that the COVID-19 health pandemic has caused a lot of financial and emotional strain on educators. In an effort to alleviate this burden, Onshape will continue to provide the Education Standard plan free, and will also provide its newest education offering - the Education Enterprise plan - free for one year to schools and universities that sign up by November 20, 2020. I've spoken with many of you over the past few weeks and you've shared that budgets and timelines are tight, and we are committed to doing everything we can to remove barriers to rolling out Onshape to your students.
If you are interested in signing up please fill out the form here: https://www.onshape.com/education-enterprise
Additionally we will be holding webinars where Educators will share information on their transition to Onshape along with tips and resources for getting started.
We understand that the COVID-19 health pandemic has caused a lot of financial and emotional strain on educators. In an effort to alleviate this burden, Onshape will continue to provide the Education Standard plan free, and will also provide its newest education offering - the Education Enterprise plan - free for one year to schools and universities that sign up by November 20, 2020. I've spoken with many of you over the past few weeks and you've shared that budgets and timelines are tight, and we are committed to doing everything we can to remove barriers to rolling out Onshape to your students.
If you are interested in signing up please fill out the form here: https://www.onshape.com/education-enterprise
Additionally we will be holding webinars where Educators will share information on their transition to Onshape along with tips and resources for getting started.
- Making the Switch to Onshape for K12: Tuesday, August 18th from 10:00-11:00AM EDT
- Making the Switch to Onshape for University: Wednesday, August 19th from 9:30-10:30AM EDT
Re: Struggling to recreate Configured Part Studio Reference Parameter
Hi Sam,
You correctly identified a bug, and this issue was fixed in the latest release of Onshape (1.117) last Friday. The right-click menus for these parameters should now always be appearing correctly.
In the future, you can use the "Report a bug" or "Contact support" option in the "?" menu for a faster response time, and an email notification when the issue is fixed.
Let me know if there's any further issues!
– Kevin
You correctly identified a bug, and this issue was fixed in the latest release of Onshape (1.117) last Friday. The right-click menus for these parameters should now always be appearing correctly.
In the future, you can use the "Report a bug" or "Contact support" option in the "?" menu for a faster response time, and an email notification when the issue is fixed.
Let me know if there's any further issues!
– Kevin
New Featurescript: Captive Nut
Captive nut makes it easy to add screw/nut joints to parts.
→ Here's a link to a video tour of the feature.
→ Go here to add the feature.
Below is an illustration of the three main insertion styles that can be achieved with the feature. Use it and let me know what you think!
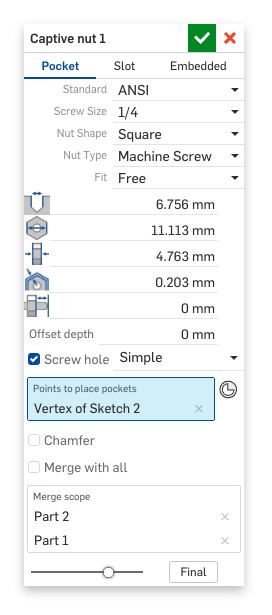
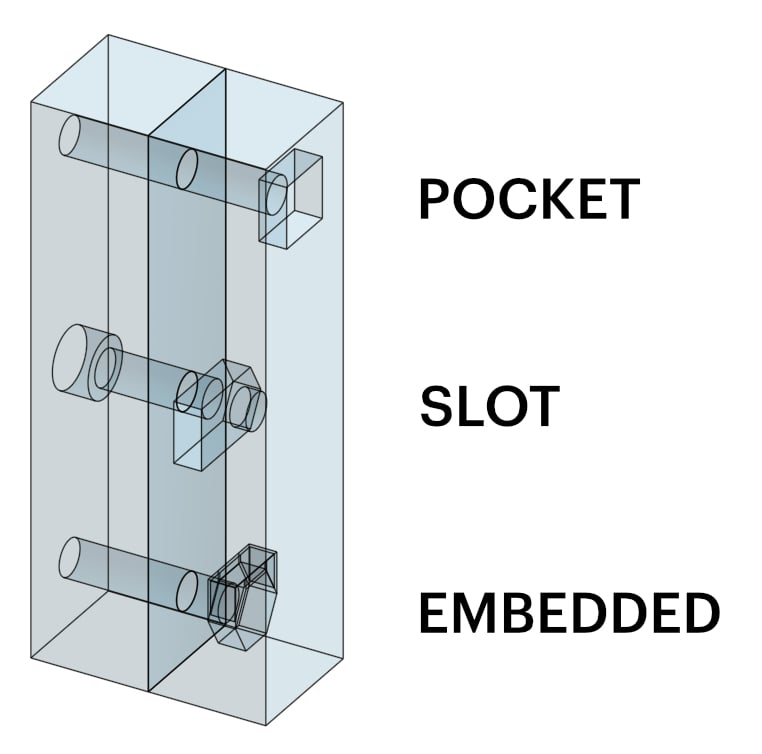
→ Here's a link to a video tour of the feature.
→ Go here to add the feature.
Below is an illustration of the three main insertion styles that can be achieved with the feature. Use it and let me know what you think!
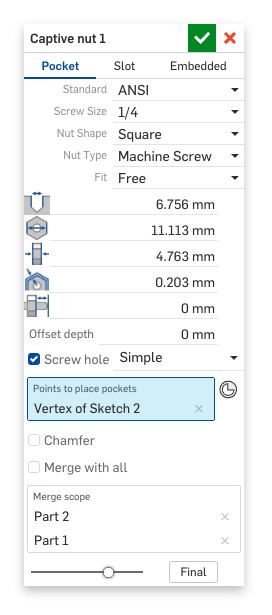
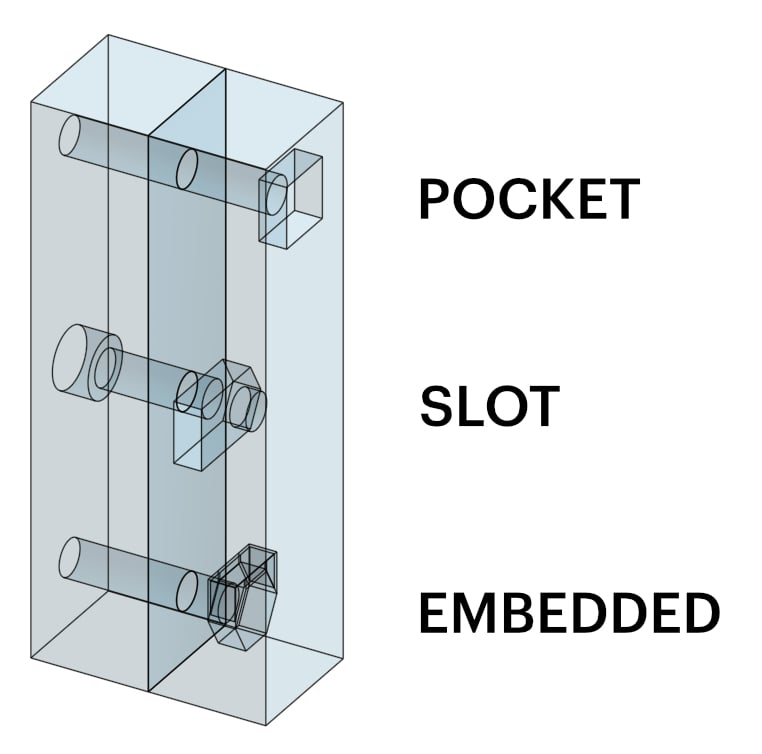

12
Re: Improvements to Onshape - July 31st 2020
Love the new Custom Mass Properties capability. When we have 5,000 grades of plastic resins, it is great to be able to plug a material's specific gravity and get the accurate part weight. I can actually plug in the formula which I use: SP.GR * .0361 * 1 * 453.6 All I need to do is find the Specific Gravity of the resin, and plug in the formula. This is something I have been waiting for for a long time. Thank you.