Welcome to the Onshape forum! Ask questions and join in the discussions about everything Onshape.
First time visiting? Here are some places to start:- Looking for a certain topic? Check out the categories filter or use Search (upper right).
- Need support? Ask a question to our Community Support category.
- Please submit support tickets for bugs but you can request improvements in the Product Feedback category.
- Be respectful, on topic and if you see a problem, Flag it.
If you would like to contact our Community Manager personally, feel free to send a private message or an email.
Transformable Boolean operation (Sweep with body as tool)
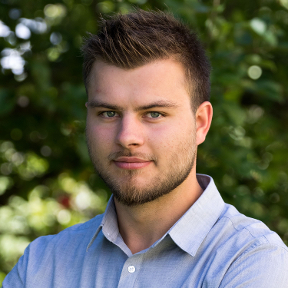
Recently I had to design a guiding slot. The function was to transform a horizontal rotation of a ring into a vertical angle change of a pin. The basic concept looked like this:
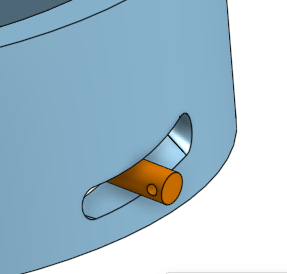
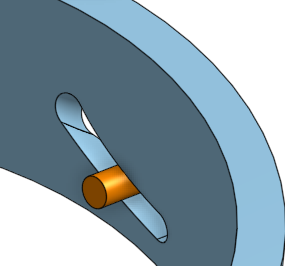
In CAM or real world milling, such geometries are no problem since you can define all axis of a tool and move it around as you please. But in the CAD design itself, it's a real pain. I managed to create the geometry by using several rotation cuts, a lofted surface which got thickened afterwards and finally a Boolean subtraction.
I've added the above example so you can understand the origin of my idea and my motivation. I started to program a custom feature which does a Boolean subtraction by moving a body in 3D space. With this feature, very complex surfaces could be created in a short amount of time without having to play around with curves, extrudes and subtractions. Simply put, a sweep which is able to use a 3d body. This is where I stand right now:
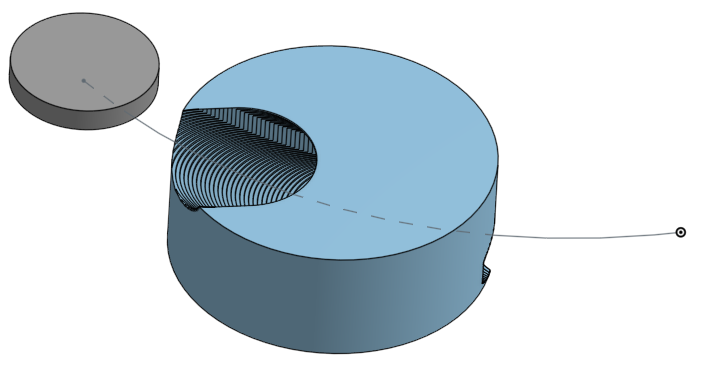
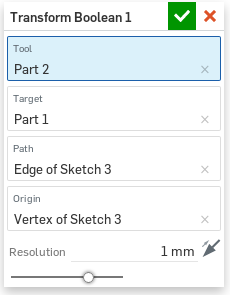
The procedure is to move the tool by certain increments along the curve
and do a subtraction after every transform. It works better than
expected but the resulting surfaces aren't usable since they are not
tangential to each other.
@Jake_Rosenfeld and @NeilCooke already helped me with the transform along the curve. Now comes the tricky part, has anyone any idea/concept of how to smoothen the cut surface? I really appreciate any help and I hope I can create a stable and reliable feature in the end that's also useful to others. I've just got into featurescript.
Feature plans are to add the possibility of using several curves to define the orientation fo the tool. For example one curve that guides the tool by its origin and aligns the tool axis normal to the curve, and a second curve that defines the orientation of the tool.
0
Comments
IR for AS/NZS 1100
https://cad.onshape.com/documents/4c823d07455a41d1f8da02fe
IR for AS/NZS 1100
IR for AS/NZS 1100
A very simple example is correctly representing a blind chamfer:
As you know, a chamfer + a fillet won't work, since the fillet can't be applied in the correct "orientation" to accurately represent the spinning mill in this case.
I make a body (this is very simple because the edge I am using is straight) that represents the mill during motion AND at the end of the path, then do the Boolean to subtract:
Could this FeatureScript you guys are talking about include the "end condition" that I'm talking about?
Could it be the vertex at the bottom of the part that makes it fail? (I did try it with a non-pointy bottom end and it still failed).
What's the state of the art in 2025 of how to do what @johannes_w was initially trying to do? I have the same problem/brief.